
Training
15 min read
Driving Fear Off The Factory Floor
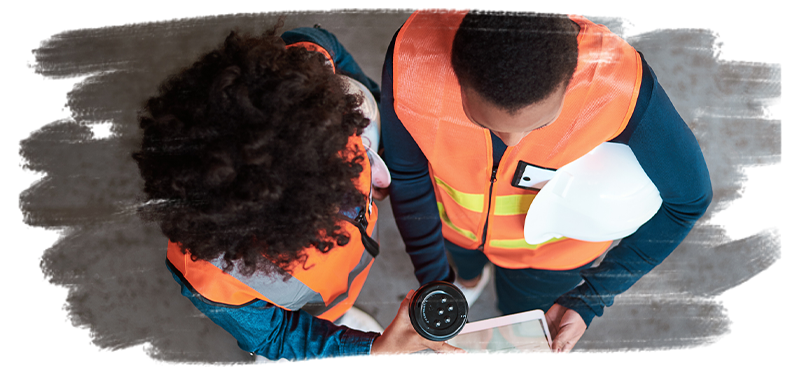
Did you know there are five fears that all human beings share?
Below is the official list, according to the widely cited psychological research outlined in Karl Albrecht’s popular book, Practical Intelligence.
Here are the five core fears out of which almost all of our other fears are created:
- Extinction: Annihilation, death, ceasing to exist.
- Mutilation: Bodily invasion, injury or attack.
- Loss of Autonomy: Paralysis, restriction, control.
- Separation: Abandonment, rejection, loneliness.
- Ego Death: Humiliation, shame, failure.
In manufacturing, operations managers and training leaders must contend with a unique set of similar fears. Particularly in the face of an economic downturn, everyone is worried to some degree.
How will we retain current employees?
How will we attract and engage new workers?
How will we keep our competition from doing so better and faster?
Plus, these reasonable fears get exacerbated by public events. In recent years you might have read about one of the following manufacturing stories:
- Chipotle experienced a string of food safety scares that caused customers to lose trust and stock prices to fall. The root cause for hundreds of customers who got sick was in part related to poor training.
- The Waste Isolation Pilot Plant had poor revision control practices that led to a half billion dollar mistake; shutting down the facility for three years and sending six workers to the hospital, thanks to radioactive cat litter.
- Fiera Foods had the death of a temporary worker when her hijab became entangled in a piece of equipment at their bakery. The industrial bakery pleaded guilty to violating the Occupational Health and Safety Act and agreed to pay a $300,000 fine.
These examples are extreme cases, but just because something is not probable, doesn’t mean it’s not possible.
Manufacturing leaders must be vigilant about operator training, critical process documentation and continuous improvement in order to meet industry standards and avoid ending up in the headlines themselves.
Below, we will share use cases from manufacturing companies just like yours, and how they’re using communication, documentation and affirmation to drive fear off of the factory floor.
Eliminate The Fear of Extinction With Communication
Have you ever read the FDA’s safety portal? You’ll find a list of industry press releases regarding product recalls, market withdrawals and safety alerts.
Being featured on such a list is every manufacturer’s worst nightmare. If your company is a food or beverage maker, it’s an existential threat to the organization. Nothing is scarier than having a reason to believe that your product may cause consumers to become ill.
During a recent Zoom call, one of our customers, a production manager at a food company, shared his thoughts from both an operational and strategic perspective:
“My biggest fear as someone working in the food industry is, I don't want to be the guy standing in front of the plant with a bunch of news reporters asking us what we did, or why we did it.
Even if your competitors experience a recall, you feel the impact of that too. If one small mayonnaise company gets a bunch of people sick, customers don't stop buying your brand, they stop buying mayonnaise in general.”
This concern is (of course) about the health of customers, but also the health of the company and the entire industry. One bad apple may only ruin the bunch, but potentially the entire farm.
If you want to eliminate this fear at your company, here are communication tactics you can take action on right away:
- Decentralize information flow and empower workers to make knowledge fluid between various departments and personnel.
- Support recruiting goals using your frontline’s compelling technology and training to entice and retain new hires.
Eliminate The Fear Of Humiliation With Documentation
Frontline workers need to bypass their fear of making suggestions that might seem wrong or silly. This type of empowerment is up to the leaders. Building a strong documentation culture can help operators relieve some of their anxiety and stop wondering if they are doing their job correctly.
Even if an employee has high anxiety around using an intimidating machine or performing a complicated process, they should be able to quickly watch a video to quickly quell their fears and do their job with competence and confidence. This is what makes them think to themselves:
“I believe this, I can do this, I think I’m willing to try this.”
It’s not unlike your personal home repair project that seems scary at first, but once you watch a handful of YouTube videos, you realize, “Wow, installing a window mounted dryer vent isn’t as complicated as I thought!”
Dozuki recently spoke with one of our automotive customers that had $300,000 worth of scrap waste. Their head of operations reported that much of that waste came from quality issues tied to operator error, particularly from new hires who were being trained ineffectively. It’s a key reason the automakers began doubling down on documentation. Not only did their digital transformation initiative lower the annual tonnage of scrap, but also lowered the abundance of fear.
If you want to eliminate this fear at your company, here are several documentation tactics you can take action on right away:
- Build a reliable help chain so employees can feel confident troubleshooting production problems, even if their experience is minimal.
- Require anybody who asks the same question more than twice to make a document for that issue.
- Gamify continuous improvement by keeping a tally of who makes the most suggestions, and rewarding both the quality and quantity of employee contributions.
Eliminate The Fear Of Paralysis With Organization
Digital transformation initiatives can feel convoluted, slow and confusing. When a new program kicks off, leaders might give sighs, but they also make groans of additional work. Because the whole team knows they're going to have to start from scratch. It’s paralysis and overwhelming.
Let’s bring this fear to life with a few more uses cases from Dozuki customers.
First, a plant superintendent at a fiber manufacturer:Next, an operations leader from a chemical manufacturer:
Finally, a training coordinator at an optics manufacturer:
Can you relate to those kinds of fears? Most manufacturing leaders can. The overwhelming number of documents, processes, training sessions, all multiplied by the number of frontline workers at multiple facilities, leads to paralysis.
In our experience, when plant managers are overwhelmed or intimidated by frontline digital transformation projects, they think it’s a pipe dream. It’s a “nice to have.” They can’t do it now, and it will take a lot of work.
Meanwhile, with so much data and information available at their fingertips, employees may also feel overwhelmed and unsure of how to prioritize and process it all. To avoid this, manufacturers need to focus on providing employees with the right information at the right time.
That way it never feels like starting from scratch or going back to ground zero.
If you want to eliminate this fear at your company, here are several organization tactics you can take action on right away:
- Sell transformation up by calculating organizational benefits like authoring time savings, rework labor savings, and onboarding time savings
- Start your digital transformation efforts small with single serving solutions that can be implemented, improved and scaled easily across locations
- Choose a pilot solution that provides service and support along your journey, so they can also support you at scale.
Ultimately, operating in a “tap your teammate on the shoulder” culture is no longer sustainable.
This tribal knowledge based approach has been used for decades, and it’s reached a point of diminishing returns. And here’s why:
Imagine how many shoulders were never tapped in the first place because a frontline employee feared looking incompetent for doing so.
Fear is a very human thing, and it’s not going away anytime soon. Whether you fear retaining current employees, engaging and training new ones, or keeping your competition from doing so faster and better, you’ve come to the right place.
Dozuki builds digital transformation solutions that take fear out of the equation.
Topic(s):
Training
Related Posts
View All Posts
Frontline Digital Transformation
How 3 Leaders Tackled Key Workforce Challenges
4 min read
A recent survey by the National Association of Manufacturers underscores a pressing concern for manufacturing executives. Nearly 75% identify attracting and retaining a...
Continue Reading
Continuous Improvement
Firefighting In Manufacturing
12 min read
Why It Happens, What It Costs, and How To Stop It Firefighting is a burning issue in manufacturing. Not only are facilities dealing with safety measures like flammable...
Continue Reading
Continuous Improvement
Dozuki's Secrets to Drastically Cut Scrap Waste
5 min read
Snuffing out the waste in manufacturing is difficult, but not impossible.Facilities who are successful in their waste reduction efforts will gain benefits in terms of cost...
Continue Reading