
Frontline Digital Transformation
6 min read
Frontline Of The Future, Part 3
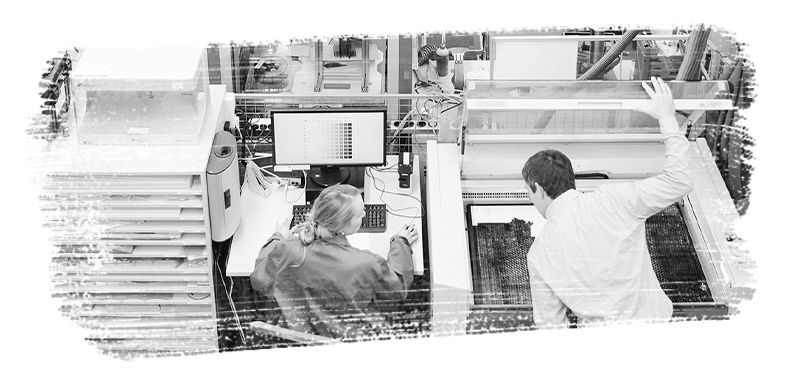
Accessibility Creates Profitability
Manufacturers that don’t provide broad access to essential knowledge are at a significant deficit.
This form of content debt comes at a very real and very expensive cost, both at the frontline and managerial level.
Our first two parts of this series focused on the evolutionary forces impacting manufacturing frontlines, and how processes can be digitized for maximum efficiency.
The logical next step in this progress is to talk about who can see what, aka, accessibility.
When companies lean on legacy document management systems (see also: dusty binders) that makes it difficult and time intensive for employees to access standard work instructions.
Tribal knowledge needs to be accounted for and made available to all. Teams that aren’t intentional about getting what’s inside of people’s brains out and into an accessible and useful form, can’t scale.
In our experience, a huge benefit of accessibility is people's desire to see this information. When workers know that their path to information, work instructions or general company knowledge is streamlined, they often become excited to engage with it.
A customer of ours, a logistics manufacturer, observed a pattern when they started focusing on frontline accessibility:
“This is the first time that I’ve done a project where more and more people volunteered to join the pilot. We started in one area of our warehouse, but have since expanded now to all logistic departments. Now team leads came to my desk asking to get access and try out this new digital platform.”
Our customer has come a long way from their old habits, which mostly included Excel & Word one pagers.
If only that was the standard when it comes to accessibility.
More than not, it looks like this:
Format? Only available on paper, maybe a pdf if you’re lucky.
Viewership? Often requires supervisor assistance to see production processes.
Distribution? Documents are cumbersome to share, particular as physical objects.
As we usher in the fourth industrial revolution, we see the industry headed to new standards, benchmarked below:
Is your accessibility ready for the frontline of the future? Here’s what we recommend:
-
Move away from paper based solutions. The worst case scenario of accessibility is not only using paper documentation, but storing in a different room than the factory floor. And understandably, many manufacturing environments are such that paper won’t survive. If you work in food processing, chicken fat might splatter onto your work instructions. If you work in heavy machinery, binders may catch on fire from three and four digit degree temperatures. Point being, your training material needs to be digital, but also available right there on the floor. Not in a series of unnamed folders deep inside the archives of your shared network drive where people aren’t comfortable navigating. Make sure it lives on multiple tablets that provide operators a simple way to access the procedures. Just remember, complicated is almost as bad as inaccessible.
-
Install digital codes on machines. Imagine the production manager at a facility where the frontline staff is not English speaking. Workers haven’t used tablets much before in previous jobs, and they’re required to perform a task on a wiper gasket. But they don’t want to search through a digital breadcrumb trail through folders. Dozuki users benefit from instant communication of procedures via a quick scan of a QR code. Create a code for any page, stick it on the machine, and now the worker can scan it and go straight to the process for the machine. You can even use multiple codes for each machine, one for operating training instructions, one for maintenance, one for training and one for safety. No searching, no mystery and no using the wrong outdated procedure.
-
Get support for hardware acquisition. Dozuki has created the most comprehensive resource on the internet for rolling out a fleet of tablets in industrial and manufacturing environments. Learn about the benefits of tablets, how to evaluate them, which ones have our highest recommendation, and which accessories are the best fit. Additionally, our team regularly consults with facilities and even helps them acquire the hardware and build the QR codes themselves. Our customers ask our sales and customer success teams about tablets all the time, and we’ve got answers ready for you. Dozuki's Professional Services Team can help with hardware acquisition. We told you we got your back!
Ultimately, digital transformation is a function of access.
Manufacturers that don't make procedures accessible are at a significant deficit.
With Dozuki, we ensure your team's tribal knowledge is accounted for and made available to the right people who will benefit from it most, when they need it the most.
Now that your process and accessibility are getting into proper shape, you’re ready to level up your frontline training. We talk about that in the next installment, part four.
Topic(s):
Frontline Digital Transformation
Related Posts
View All Posts
Frontline Digital Transformation
Creating The Frontline Of The Future, Part 7
9 min read
Technology Enables Resilience Do you know what the first manufacturing technology was? Let’s go back to prehistoric times, over two million years ago. The Stone Age...
Continue Reading
Work Instructions
5 Instant Benefits of Digital Work Instructions
5 min read
Unlike other digital transformation projects, making the simple switch from paper-based work instructions, SOPs, and other documentation to digital work instructions provides...
Continue Reading
Product
How to Use Dozuki for Work Instructions
7 min read
Dozuki is the leading digital work instruction tool for industrial businesses all over the world. Our platform enables better employee performance by improving how you...
Continue Reading