
Standard Work
6 min read
How Auto Manufacturers Can Avoid Production Potholes
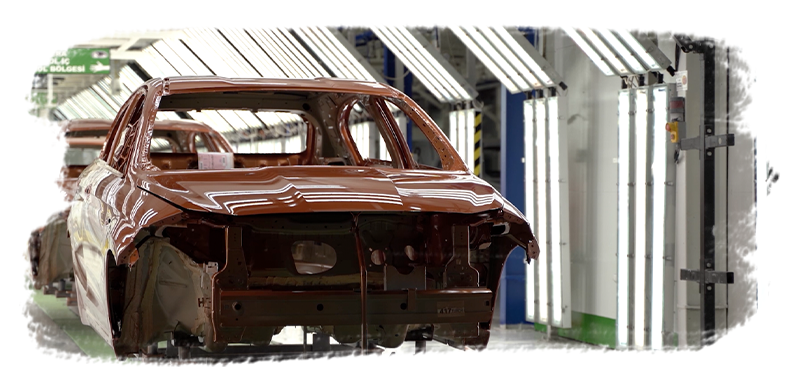
Automotive manufacturing has been a windy road.
Here are a few of the social, economic and cultural trends currently impacting automotive manufacturing.
But automotive manufacturers have navigated extreme adversity before.
Now there’s a chance to shift into high gear. And to compete in an increasingly competitive market, your facility needs to accelerate its digital efforts.
Dozuki builds the leading work instruction and training solution for over 600 industrial businesses across the world. Including top tier manufacturers in the automotive industry.
Below, we’re sharing success stories from our automotive customers, insights gleaned, and tactics you can put into action immediately to build the frontline of the future.
1st Gear: Optimize Production Performance In Real Time
Protecting your facility from the negative impacts of absenteeism is essential for long term success. We speak to automakers nearly every day, and plant managers and supervisors are constantly trying to fill frontline vacancies on short notice. And the companies that aren’t digitally tracking their training programs are falling behind on production targets.
If you’re not organized about who is trained to do what, that leaves your organization in a vulnerable position. Without systems in place, you can’t quickly reference your training records, see who the best person would be to fill in at that position on that particular day, and get back to work.
During a recent onboarding call with one of our customers, their lead engineer explained that their training department had a lot of hiccups when it came to documentation. They were still using printed material of their procedures, and it caused irregularities and errors in their frontline tracking.
Managers may mistakenly write down the incorrect job codes, or have poor handwriting that was unreadable. One department supposedly had a dry erase board to track all of their frontline training. Which was beautifully designed, unfortunately it also could have been erased instantly with a quick wipe of a hand!
Such a resource can’t help managers when multiple employees are out sick and they need to man the line quickly.
How easy can you fill frontline vacancies on short notice?
The harsh reality about absenteeism is, it comes unannounced. Frontline workers might miss work for a number of reasons, and if you’re not equipped with the right digital tools, then you won’t capitalize on opportunities to optimize production performance in real time.
Think of it like switching gears, an apt metaphor for this industry. We recommend that automakers create a dynamic workforce with star players who can fill in and do a bunch of roles during inevitable absenteeism and even turnover. With proper digital tracking of your training programs, you will know within seconds exactly who can fill in during a pinch.
2nd Gear: Multiply Your Training Leaders
The number one obstacle to digital transformation success is a company culture that resists change. All humans fear change to some degree, but there are measures you can take to make change feel less like driving a stick shift uphill in a blizzard. Just know that getting everyone on the frontline trained is possible, but requires slow progress.
It’s key to start small and strategic with a pilot program, before considering a full scale rollout. Accelerating from zero to sixty in two seconds (like driving the new Tesla model) doesn’t scale across the entire manufacturing organization. Starting small with digital training proves that basic understanding is there. Then you can move forward and collaborate with other locations organically. And set the stage for rapid expansion.
There’s a concept that our customers often use when it comes to this process called multiplication. It’s most helpful for manufacturers with multiple locations or facilities. Here’s an explanation of multiplication from our customer, a global supplier to the automotive sector:
Our implementation plan focused on multiplication. We started by developing a key author of process documentation at each plant. That local champion would train new authors, and so on, and so on. This ultimately inspired the assembly of a steering team (no pun intended!) during onboarding that helped drive the digital transformation vision.
Soon their frontline had standardized best practices, and trained their teams accordingly.
How well do you share information across shifts, lines, and facilities?
For technological progress to be fun rather than scary, positive word of mouth is critical. Frontline workers need to see digital tools (tablets), as an improvement over the current manual process (dusty binders). They also need to see salaried staff and engineers taking a test drive with those resources, so to speak.
If you want operator engagement and adoption on your floor, start by putting tablets in the hands of culture leaders. The others will look up to them. They’ll see them using the tools, and it will be much more likely to be adopted.
3rd Gear: Drive The Path to Successful Transformation
Now that the status quo has shifted gears in automotive manufacturing, it’s time to abandon outdated training and documentation practices. If you want to create controlled standard procedures, reduce quality issues and increase efficiency, you’re well on your way with Dozuki.
Start by optimizing production performance in real time, and follow that up with leveraging leaders to train the masses.
Your journey to building the frontline of the future will have significantly fewer potholes.
Find out more about how we can help your automotive organization.
Topic(s):
Standard Work
Related Posts
View All Posts
Frontline Digital Transformation
Frontline of the Future: Part 1
8 min read
Historical Forces Impacting Manufacturing At Dozuki, we have our finger on the pulse of manufacturing trends. We believe it’s part of our mission to formulate clear...
Continue Reading
Continuous Improvement
How the Best Plant Managers Solve Production Challenges
6 min read
As a manufacturing plant manager, meeting production targets, reducing downtime, and filling empty roles are all ongoing goals. The best plant managers know that these goals...
Continue Reading
Frontline Digital Transformation
Frontline Of The Future, Part 6
7 min read
How To Staff Your Front Line Without ExcelOne of our customers, a plant manager at a chemical manufacturing company, made this observation:“Getting the time to train every...
Continue Reading