
Continuous Improvement
5 min read
Dozuki's Secrets to Drastically Cut Scrap Waste
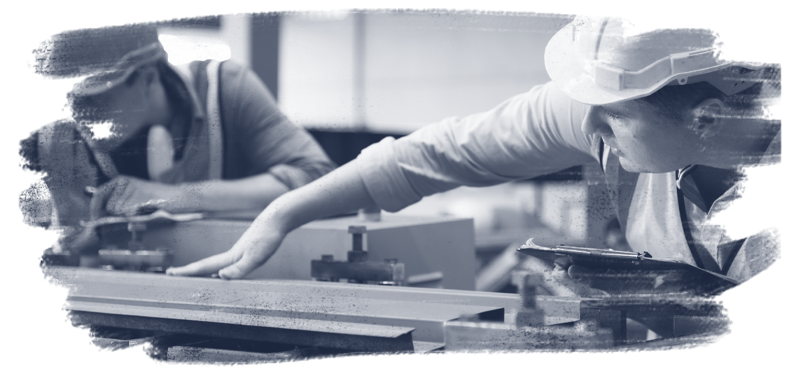
Snuffing out the waste in manufacturing is difficult, but not impossible.
Facilities who are successful in their waste reduction efforts will gain benefits in terms of cost savings, environmental impact, reputation, and compliance with regulations.
This is an aspect of manufacturing digital transformation that Dozuki discusses with all of our customers.
Operations and production directors can’t afford to ignore this critical issue. Lucky for them, Dozuki can help directly reduce scrap waste with our connected worker solution.
Below, the waste reduction strategies are broken down into three categories, including a case study for each one:
- Reducing scrap waste by adhering to standardized, controlled processes
- Reducing scrap waste by maintaining proper changeover processes
- Reducing scrap waste by recovering lost time and materials
Standardized, Controlled Processes
When the wrong parts are ordered or engineering design changes aren’t communicated to the assembly floor, scrap and rework pile up. Standard work prevents scrap by giving an accurate account of the materials needed to maintain proper workflows. This way, when processes are altered or changed, the resulting effects can be predicted and prepared for, preventing costly rework.
Shockingly, we have spoken with countless supervisors and operators at Fortune 500 companies that rarely use work instructions. This results in process variation and ultimately results in rework, scrap waste, and safety incidents.
One Dozuki customer, a global flooring company, calculated that someone accidentally setting up a key machine wrong was costing the company $7,500 dollars a month — or $90,000 a year.
After implementing Dozuki, that cost was cut by 10% and was able to save $18,000 in scrap reduction over two years.
Maintaining Proper Changeover Processes
Another opportunity for scrap waste reduction is changeover time. Particularly for the manufacturers who are seeing employees retiring en masse. They want to capture tribal knowledge and share it digitally with new hires.
But the all too common practice is keeping everything in veteran employees’ heads. This leads to operator confusion and multiple ways of doing processes, delays in changeover, rework, and of course, scrap waste.
Dozuki works with a construction manufacturing company that needed to digitize their documentation practices to reduce changeover time.
Not only did they accomplish that goal, but the scrap waste metric followed suit. This company experienced annual changeover time savings of $71,000, and that further led to a scrap waste reduction of $392,000.
It’s amazing how shaving 45 minutes off a changeover process, and documenting that in digital content, can have a ripple effect through the entire organization.
Recovering Lost Time & Materials
Lean manufacturing is about minimizing waste and maximizing efficiency throughout the production process. This methodology is particularly critical in environments where cost effectiveness is critical and surplus inventory decreases overall profits.
Now, while having a zero waste culture is certainly admirable, there are ways firms can recover lost time and materials through digitization. A key driver of that savings is with a strategic upskilling initiative.
Dozuki works with a multinational abrasives manufacturer that uses our connected worker solution in their loss deployment program to improve operator training and efficiency. Managers began targeting key processes that produced the most waste and audited the process to understand how they need to improve operator training to limit waste generation and increase efficiency.
Their challenge was to refocus on foundational skills and aspects of work instructions that were not previously referenced, and with a lot of dedicated work, their team was about to reduce excess inventory significantly.
In 2021, they saw $75,000 total in savings. 90% of their users were trained in the first quarter, and after implementation of Dozuki, they experienced 82% reduction in waste generated over the year. $14,000 in rework waste during Q1 plummeted down to $2,500 in Q4!
Ultimately, snuffing out the scrap can save your company hundreds of thousands, or even millions of dollars per year. If you standardize changeover processes, and find ways to recover lost materials, the financial burden won’t weigh so heavy.
And now your frontline will be empowered to meet production targets efficiently.
Topic(s):
Continuous Improvement
Related Posts
View All Posts
Success Stories
How Dozuki Streamlines Knowledge Transfer
4 min read
Dozuki is changing how companies operate by eliminating unnecessary steps from critical workflows. This article explores how to drive efficiency and highlights a real-world...
Continue Reading
Continuous Improvement
Implementing Continuous Improvement with Dozuki
3 min read
Is your company interested in reaping the benefits of continuous improvement (transparency, efficiency, cost reductions, etc.) but aren't sure where to begin? Dozuki has you...
Continue Reading
Success Stories
How Dozuki Streamlines Authoring Time
6 min read
Traditional methods of updating and distributing process documentation can be incredibly time consuming. For one Fortune 100 heavy machinery manufacturer, the manual process...
Continue Reading