
Training
3 min read
How to Deliver People Centric Manufacturing Training
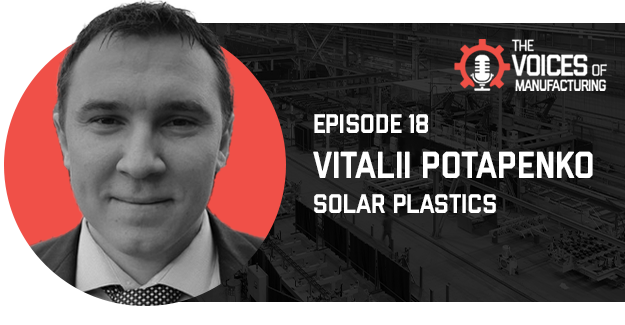
“The supervisor is the customer of the training.”
When Vitalii Potapenko of Solar Plastics first shared these words with us, we knew their company was doing something special in the manufacturing space.
Savvy manufacturers are evolving training programs into more inclusive, people centric directions.
Solar Plastics has fifty years of design and engineering expertise creating custom rotational molding for large, customer, low-volume and hollow plastic parts.
Vitalii holds a unique role at this organization, in that he manages daily production activities, as well as the engineering department and training. He excels at delivering people centric manufacturing training.
We chatted with Vitalii and learned valuable insights on promoting quality, reducing cost, and identifying and implementing process improvements. Vitalii’s company is an ideal case study about why the person who is doing the training will shape the impression a new employee has of the company for a long time.
The way Solar Plastics develops their frontline employees inspired us, and we know it will do the same for you.
Show notes:
05:47 — Building a robust training program in Mexico
09:51 — Focusing on quality, not speed
12:25 — Matching employee personality with training opportunities
15:15 — Hanging career path posters at every location to inspire growth
20:13 — Reinforcing training over time
23:54 — Treating the supervisor as the customer of the training
32:04 — Making video work instructions to cross language barriers
Additional Resources:
- A New Model For Manufacturing Hiring: Constraints, Currency, Clarity
- Effective Ways To Reduce Employee Training Costs In Manufacturing
- The Cardinal Rule of Process Documentation: Read the Comments
Related Posts
View All Posts
Work Instructions
Why You Need a Custom Library of Digital Process Knowledge
5 min read
No worker operates in a vacuum. Human output potential is a function of our tools, our training, and our mental engagement. Your facility has state of the art tools, a...
Continue Reading
Continuous Improvement
Operational Resilience Explained
11 min read
America was built on manufacturing.And manufacturing was built on resilience. Our country has proven to be a place where workers who are skilled with their hands (and have...
Continue Reading
Training
Knowledge vs. Skills: Why Manufacturers Must Train For Both
5 min read
Two terms manufacturing leaders use a lot are knowledge and skills. You’ve probably read material and even participated in training programs around topics like tribal...
Continue Reading