
Continuous Improvement
7 min read
Kaizen and Standardization with Dr. Robert Maurer
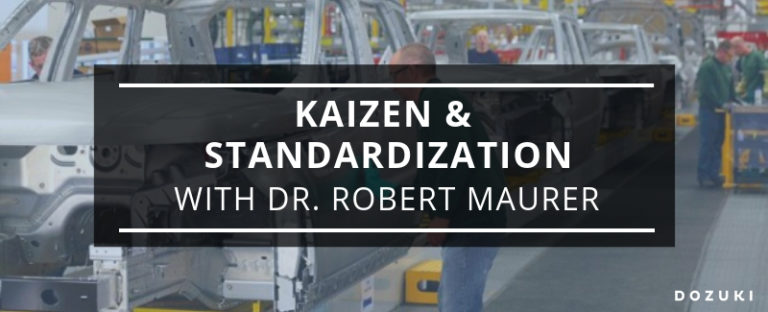
We spoke with Dr. Robert Maurer, author of “Spirit of Kaizen,” a leading expert in the field of psychology and organizational change, about Kaizen and the role of standardization in improving processes and creating an efficient culture of continuous improvement.
Kaizen = Good Change
Translated literally, Kaizen means “good change.” We typically think of change as radical transformations that revolutionize businesses. But science would suggest that this is not how successful change happens.
Radical change is:
- Uncomfortable
- Unsustainable
- Risky
Instead, a Kaizen approach (good change) sets out to take small steps towards larger goals.
Using Kaizen, Smaller Goals & Tasks Help:
- Avoid the pre-conditioned response of fear and resistance
- Create a sustainable culture of acceptance
- Mitigate the inherent risk of change
The Origins of Kaizen Methodology
Dozuki: You’ve said before, “The good news is the brain is a creature of habit. The bad news is the brain is a creature of habit.” What do these concepts have to do with manufacturing?
Robert Maurer: Although Kaizen has its origins in ancient philosophy, it was used systematically first in WWII to increase the quality of military equipment. Because we entered the war so suddenly and with very little human or material resources, the United States had to train workers on the line as they were turning car factories into tank factories.
American manufacturers looked for extremely small ways that they could improve the process or product; to their surprise they found that very, very small steps led to big changes. This methodology was adopted throughout the nation and essentially reintroduced to Japanese manufacturers after WWII.
Kaizen and Standardization
D: Standard Work is the process of standardizing, training, gathering feedback and data, and then using that information to change processes for the better. In your mind, how might standardization fit into the idea of Kaizen and small improvements?
RM: Some of the industries that have made the most innovations and improvements to products and processes are those that needed standardized processes — for example, automotive, aerospace, or healthcare — places where you have to have very rigid protocols.
What happens is two key things:
A) In order for protocols (standards) to continue to improve, you have to have a workforce that’s thinking, “what small step could I take today to improve the process or product?” Standardization allows everyone to look for incremental ways to make improvements, even as you formalize the process.
B) Kaizen also works with those standardized processes by breaking down problems. Because these processes tend not to be perfect and the people implementing them are not perfect, there’s always going to be errors. So with standardization and Kaizen, very small mistakes are identified early, and improved upon, before they get too big to ignore.
Key Takeaway:
In the same way Kaizen breaks down improvements into small steps, standardization works with Kaizen to catch problems early and break them down into more manageable sizes.
Using Kaizen to Boost Morale
D: While the concept of Kaizen makes a lot of sense for Standard Work and process improvement, people might understand less about how Kaizen works to improve company culture. In “The Spirit of Kaizen” you talk about using Kaizen not only to cut costs and improve quality, but also to boost morale. Can you shed some light on this lesser known benefit?
RM: When you focus on making very small changes, workers arrive each day knowing that they can find ways to make their job easier and more efficient — which will ultimately improve quality and reduce cost. As a result you’re going to naturally have people that are more engaged and proud of what they’re doing because they feel that the people up the line are actually listening to them.
"people are more engaged and proud of what they’re doing because they feel that the people up the line are actually listening to them"
This is in contrast to organizations who implement big new programs from the top down, which inevitably falls out of favor with employees. Six months later, company leaders bring in more expensive consultants for a new program, and people get more cynical and detached as new innovations are tested.
If everybody is coming to work each day thinking “what small step could I take that might improve the process or product?”, then change is an essential part of the culture and people are anticipating change rather than reacting to it.
Key Takeaway:
By allowing small improvements to take place, it naturally increases engagement, which will in turn improve morale and culture.
Case Study: General Motors vs. Toyota
D: What’s one example of the impact Kaizen can have on improving culture within a company?
RM: One of my favorite examples is how Kaizen got reintroduced into the United States. The Japanese were starting to make cars that were stealing market share from American carmakers. American carmakers were sure it was because the Japanese unions were passive and their costs were lower, among other excuses. Until there was a plant in Fremont, California that General Motors had shut down because it had such union problems. The unions were so angry at management they were literally sabotaging the cars, and admitting to it.
Same People, Different Management
RM: At one point, when the Japanese were starting to impress American manufacturers, GM reopened that same Fremont plant with the same exact workers. Those same workers were making a car that was designed by Toyota, using Toyota management principles (Kaizen). A year later, the plant was turning out the highest quality cars in the General Motor’s system and Kaizen took on a whole different meaning.
I’ve heard interviews of those who were sabotaging cars, who were now showing up in dealers’ showrooms, standing in the corner with pride, looking at how salesmen were bragging about the cars that they were building. GM workers went from sabotage to pride, based on nothing other than a different set of ways to manage people.
To read more about Kaizen and Dr. Maurer's work, check out our book club synopsis of "The Spirit of Kaizen." His latest work, "One Small Step Can Change Your Life" applies Kaizen principles personal development and growth.
Related Posts
View All Posts
Continuous Improvement
Book Club: "The Spirit of Kaizen"
12 min read
About the Dozuki Book Club: Your go-to place for industry books and resources. Our team works hard to curate knowledge from industry experts, letting you quickly identify key...
Continue Reading
Continuous Improvement
The Ultimate Lean Glossary
5 min read
The world of Lean Manufacturing is full of acronyms and industry buzzwords. No glossary could encompass the full breadth of terminology, but it’s always helpful to have a...
Continue Reading
Continuous Improvement
What is Standard Work?
6 min read
Lean operations and manufacturers have used Standard Work for decades, yet many companies lack clarity when it comes to this fundamental lean methodology. How is Standard...
Continue Reading