
Continuous Improvement
4 min read
Lean, Six Sigma, and Quality Management Systems
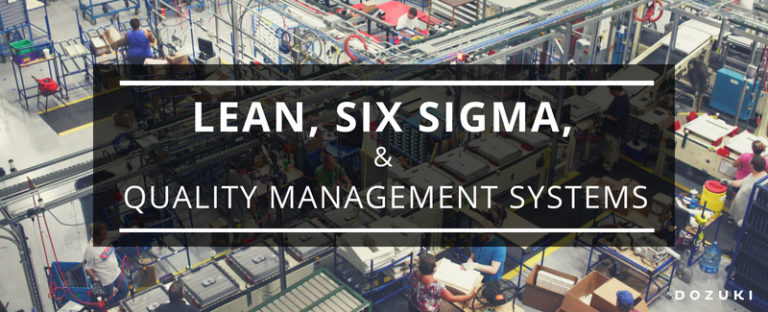
Six Sigma, Lean, and Quality Management are distinct approaches to reducing waste, defects, and providing value to the customer.
With so many approaches to process excellence, it’s important for continuous improvement professionals to understand the differences between the three and how to put it all together for optimal improvement. By allowing these systems to engage with one another, companies can elevate both their continuous improvement and risk management processes.
What is Six Sigma?
Reduce Process Variation and Special Cause Variation
Six Sigma is a philosophy for pursuing process improvement to increase customer satisfaction. While it is often used in conjunction with Lean, they are not the same. Six Sigma focuses on reducing process variation to improve consistency, while Lean focuses on other forms of waste.
This perspective focuses on inconsistencies that generate waste, using data analysis and statistical tools to reduce process variation.
What is Lean?
Reducing Process Waste and Production Cycle Time
Lean is a culture that relies on respect for people, including customers and employees. In turn, this respect translates to better feedback and continuous process improvement. By focusing on culture, innovation is centered on reducing wastes of all kinds.
Lean pursues perfection by putting the customer first, defining waste as any activity that doesn’t add value to the customer. Reducing cycle time is at the heart of measuring process improvement in Lean systems.
What is a Quality Management System (QMS)?
Focusing on Customer Needs via Interconnected Processes and Tools
A Quality Management System (QMS) is a set of interconnected processes and tools that help companies meet customer demands to continuously improve their processes and performance. Previously confined to production environments, all industries have adopted quality management systems to improve various aspects of an organization.
Part of this holistic approach to quality means that providing value to the customer begins with leadership, and then engages all departments.
Lean, Six Sigma, and Quality Management
These frameworks can present a mixed web of concepts and beliefs, but when fully understood, these systems don’t compete, but actually support each other.
Both Lean and Six Sigma use a proactive, data-driven approach towards improvement and waste elimination. Likewise, quality management systems rely on evidence-based decision making to solve problems and drive improvement. This creates concrete and measurable evidence of improvements and demonstrates value of Lean and Six Sigma activities.
Comparable Concepts
Lean & Six Sigma |
Quality Management Systems |
---|---|
Respect for the individual | Engagement of people |
Value creation for the customer | Customer focus |
Statistical tools to reduce process variation | Evidence-based decision making |
Leadership must be engaged | Leadership |
PDCA and DMAIC iterative problem solving | Process approach (PDCA) |
Perfection is attainable | Continuous improvement |
Eliminate waste and reduce cycle time | Focus on process and performance |
By eliminating waste with Lean, risks and opportunities become more visible. By reducing variation with Six Sigma, the predictability of process outcomes are improved. When combining these approaches, the path to quality management becomes much clearer. This increased transparency allows for better strategic decision making and a clearer understanding of customer needs.
When used together, Lean, Six Sigma, and QMS are a powerful group of tools to drive quality and improvement.
Implementing New Tools and Managing Risk
Improvement and risk management are two sides of the same coin. Improvement reduces risk, however, the act of improving or changing a process can carry its own risk.
Organizations should continue to assess opportunities and risks associated with improvement efforts. Evaluating a QMS and adapting to technological advancements requires a thoughtful and strategic approach.
Related Posts
View All Posts
Standard Work
Quality Assurance in Manufacturing: An In-Depth Guide to Achieve Customer Confidence
23 min read
It’s time to talk about quality. In this industry, quality is everything, and competition between manufacturers is fierce. Table of Content 1. Key Principles of Quality...
Continue Reading
Continuous Improvement
A Quick 5 Step Guide to Lean Product Development
8 min read
In the fast-paced world of product research and development, lean methodology can help reduce waste and shorten delivery times. This guide outlines five quick steps to bring...
Continue Reading
Standard Work
11 Benefits of Standard Work
5 min read
Taiichi Ohno, a founder of the Toyota Production System (TPS), had this to say about Standard Work, “without standards, there can be no Kaizen.” As the foundation for all...
Continue Reading