
Standard Work
7 min read
Manufacturing The Heavy Way: Unlocking Productivity Gains
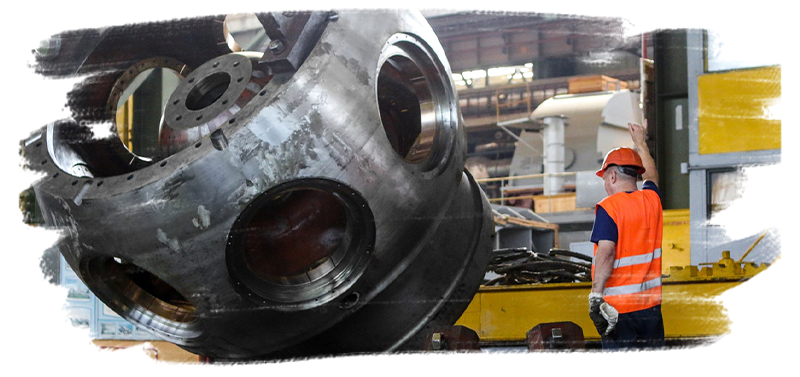
Disruption is the new status quo in heavy equipment.
Supply chain challenges continue to impact production.
Covid accelerated labor trends that impact every part of the industry.
Companies struggle to retain young, engaged, productive frontline workers.
But savvy companies are capitalizing on the rising demand for heavy equipment.
Dozuki has spent over a decade working with top brands in this industry. Below, we’re going to share success stories from our heavy machinery customers, insights gleaned, and tactics you can put into action immediately to build the frontline of the future.
Before we jump in, here’s a short film with an overview on the industry:
Transition The Ownership of Processes
Simplified and standardized formatting is paramount for work instructions in the heavy equipment industry. Engineers can easily spend too much of their valuable time trapped in PowerPoint, creating and updating documents. And that’s not the most productive use of their time.
Dozuki has a customer that specializes in remanufacturing, so they’re main processes are breaking down heavy equipment, cleaning and either reassembling the parts, or building something new.
They have a lot of processes to account for. They need to create startup, operational and maintenance instructions. And the team is heavily impacted by supply chain issues, absenteeism and labor shortages.
When we first started working with them, we came onsite to help them build our processes initially, to lighten the burden of their subject matter experts. One of the engineering managers put their struggle into perspective with the following numbers:
This project was not a quick fix. Implementation took us the better part of a year.
But what we learned was, the incremental progress created compound interest. Once we transitioned to digital work instructions and training, we started getting some of that responsibility off their managers’ and supervisors’ plates.
By slowly transitioning the ownership of the processes to workers through self-guided programs, that removed some of the burden on the folks inside the organization. Now they could shift gears into other projects and concentrate on scaling their world-class facilities.
Are your operators tapping the screen, or tapping a coworkers’ shoulder? How could you help them take ownership over productivity gains and process improvements?
This facet of digital transformation cannot be ignored. When you run enormous facilities manufacturing very large pieces of heavy equipment (with legacy machines that have been around for decades), the ship is going to turn around slowly. Organizational change will feel painfully slow at times.
But that doesn’t mean you’re not making progress.
As our customer above taught us, any team can incrementally build a perpetual motion machine of continuous improvement. Self-guided digital solutions can empower operators to turn complex concepts into simple visual training. And do so in a way that doesn’t need micromanagement like the outdated approaches to process documentation and training.
Standardize Your Containment Strategy
Containment planning is what a company does when a problem is identified and they want to minimize impact. Our entire planet learned the value of this strategy during the pandemic, when containment took on new meaning.
We were all urged to “stop the spread,” meaning, break the chain of transmission and prevent the coronavirus from spreading to new people.
In heavy equipment manufacturing, containment is equally as important.
When there’s a safety or quality issue on the line, and it’s not detected, documented and distributed for the broader team, then that quality disruption can impact everything from productivity to parts to customers and suppliers.
Our customer success team recently ran their quarterly best practices session with one of our heavy equipment customers. The topic of containment came up, and we talked about One Point Lessons (OPL). These are quick yes or no visual references (go/no go) to help the operator see what’s good versus not good, or what’s correct versus not correct.
When it comes to continuous improvement training for safety, quality and equipment operations for manufacturers, containment is key to prevent issues from happening again.
The challenge is, although manufacturers face this issue pretty regularly, they typically put temporary solutions in place (like OPLS) to contain the problem, but never include it into their standard way of doing their job.
Without standardizing their containment strategy, issues can pop up again with only temporary countermeasures in place.
Dozuki provides a way for manufacturers to easily include these solutions into everyday life. With our documentation and notification systems, after containing the issues, teams can go one step further. They can add these safety or quality alerts into the standard work to become part of the operator’s normal routine.
If you want to ensure quality and consistency across your line, use digital solutions to detect, document and distribute problems in real time. Don’t settle for temporary solutions that merely solve one problem, but use permanent ones that become organizationally aligned.
Focus on tapping screens, not tapping your coworkers' shoulders:
As the rising demand for heavy equipment continues, figure out how you can transition ownership of processes to frontline workers, and contain problems in a more democratic and distributed way.
Then you can spend the rest of your energy scaling your world class facilities.
Topic(s):
Standard Work
Related Posts
View All Posts
Industry News
What The Doc Ordered: Better Performance in Medical Manufacturing
9 min read
The landscape of medical manufacturing has gotten more complex. Pandemic related shutdowns created global supply chain disruptions A batch of macroeconomic and regulatory...
Continue Reading
Frontline Digital Transformation
Frontline Of The Future, Part 3
5 min read
Accessibility Creates Profitability Manufacturers that don’t provide broad access to essential knowledge are at a significant deficit. This form of content debt comes at a...
Continue Reading
Work Instructions
The Cost of Bad Work Instructions
10 min read
Bad work instructions are the norm. Documentation is often created to check a box for audit or compliance purposes. But once completed, those work instructions get trapped...
Continue Reading