
Continuous Improvement
11 min read
Operational Resilience Explained
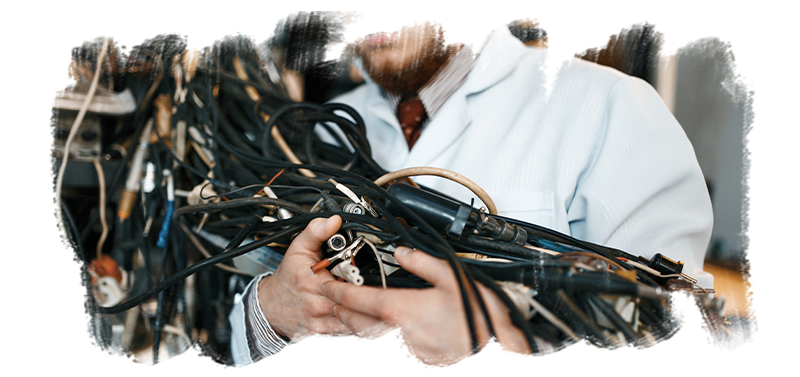
America was built on manufacturing.
And manufacturing was built on resilience.
Our country has proven to be a place where workers who are skilled with their hands (and have a head for all things mechanical) can flourish. Even during difficult times.
The value of resilience has been etched into the soul of our most famous products:
Thomas Edison’s Phonograph in 1877…
Henry Ford’s Model T in 1908…
Elon Musk’s Tesla Roadster in 2008…
Without the consistent application of this value, these industrial giants who went on to shape our nation’s history would have disappeared.
Would you say your company’s operational resilience is high? Do you have the processes and technology in place to prevent, recover, and adapt to the next manufacturing uncertainty?
In our recent series, Create The Frontline Of The Future, we’ve been sharing strategies and success stories from our customers who demonstrate operational resilience in the face of new challenges. It’s inspiring to see how those manufacturers are fortifying their culture with digital transformation initiatives, empowering and equipping their teams for the changes coming next.
Below, we’re going to continue that thread with operational resilience recommendations so your organization can increase its adaptability and responsiveness.
How to Hardwire Resilience Into Your Operation
First things first. What is operational resilience? It’s the ability of a company to immediately respond and adapt to the changes in processes, systems and environments in a people-centric way.
For additional context, The World Economic Forum, in collaboration with McKinsey, conducted research on the topic of operational resilience. According to their report, leading companies are building new levels of resiliency in many ways, not the least of which is moving quickly to digitize operations end to end.
Their study reported that companies often achieve significant and simultaneous improvements in multiple performance measures when they integrate advanced digital technologies across the value chain. Participating manufacturing organizations reported:
- Productivity increases of up to 90 percent
- Lead time reduction of up to 80 percent
- Speed-to-market improvements of up to 100 percent
Now the challenge becomes, how do you hardwire these behaviors into the organization so that it is stronger in the years ahead?
Dozuki has a customer in the wireline openhole logging services industry. During the pandemic, when a large number of their employees worked remotely, their field staff spent a lot of their time working at reservoirs as the response teams to customer needs.
Particularly during the lockdown, without a traditional office space, communication and accessibility were more critical than ever.
We spoke with one of their documentation leads, who said his field staff was already quite resilient. But sometimes a snag would come up out in the wild, and workers would need reassurance to double check work instructions to ensure they didn’t have an issue.
Previously, frontline workers at well sites were historically reaching out via cell phone to get instructions on what to do.
But with their digitization efforts, now those calls were no longer needed. Every possible scenario to troubleshoot was available at their fingertips, updated in real time, on the Dozuki platform.
Read more about this important issue Forbes via Dozuki Co-Founder Brian Sallee:Operational Resilience: Fortifying Your Company Against Disruption.
Here’s an excerpt from that article to reiterate:
When manufacturers standardize their knowledge management efforts globally, companies can be more operationally resilient, without dramatically increasing costs.
Frontline employees are literally hardwiring resilience into their operating system, and in turn, figuratively hardwiring that pattern of behavior so it becomes instinctive.
Now that you’ve elevated the collective intelligence of the team, our next topic is training.
Create A Centralized Hub For Employee Training
Did you know that in the 1940’s, 70% of our country’s manufacturing was focused on wartime production? We recommend reading a fascinating book called Freedom's Forge: How American Business Produced Victory in World War II.
Here’s some trivia to blow your mind. American factories during that time were:
- Redeploying a wartime focused facility every 5 minutes
- Producing one 150 tons of steel every minute
- Launching 8 aircraft carriers a month and 50 merchant ships a day
Resilience was the order of the day. Manufacturers had no choice but to respond quickly to the country’s needs and supply our soldiers with everything they required to survive during the most difficult time in our nation’s history.
Thankfully, our economic needs are not as acute as they were during wartime. Technology has advanced astronomically. However, every generation has its own crises to contend with.
Marissa DeWhite, one of our Dozuki team members, has spent the past two years helping companies implement a culture of continuous improvement that empowers their workforce. Marissa explained that Dozuki still hears from customers to this day about the effects of the pandemic on their manufacturing operations:
“Expert veteran folks have already retired, or they have expedited their plan and will retire soon. However, many manufacturers we talk to haven’t discovered a foundational way to capture tribal knowledge before it walks out the door.
Life throws these massive curveballs that we have recently experienced and being prepared for the unknown is important. Only with the right platform (and mindset paired with it) can organizations have a better chance at staying afloat.”
If your company wants to raise your operational resilience, you need tools and systems that enable you to capture content (both written and visual) more efficiently than with the traditional tools you have been using.
Without a centralized hub for all your content and best practices to be able to use to train the constant influx of new people, you’ll be behind. Speaking to a more technically savvy generation that relies mostly on pictures/videos in their everyday life will be hard.
This strategy directly impacts employee retention, an urgent issue many manufacturers have been struggling with. The revolving door of new people coming in calls for faster response times in terms of training needs, and more compelling and clear career paths for those employees.
If your company can showcase both the technology and the trajectory that’s possible when working for you, your employer brand will thrive, even during a down economy.
How to Sell Digital Transformation Internally
Dozuki has a customer in remanufacturing and distributor of drivetrain products. Behavioral safety is absolutely essential at their facilities. And just recently, their director of technology shared a remarkable story with our Customer Success team.
TL;DR – Four and half years of bad behavior was corrected to a safety process in a single day because of the program and the ability to make comments on guides.
Here’s their story.
A frontline employee was reaching under one of the automotive units, while it was on a hook, to remove an oil plug. That person commented on the work instructions:
“Wait a minute, why are we reaching underneath a 750 lb unit when it’s only strung up by a nylon strap? If that strap ever went wrong, we’re going to lose a hand and a wrist. Why don’t we leave the plug in and do it in later steps when the unit is standing upright on the bench?”
The following day, another one of their operators (with a four and a half year tenure) who had been doing this procedure hundreds of times, sent that change down the pipeline. He changed his behavior without even being asked. The next day he performed that task in front of a safety supervisor from the parent company. The operator left the plug in the transmission until it was upright, four or five steps later. Because the insight was undeniable.
And here’s the best part of the story.
The safety supervisor who witnessed this change in behavioral safety called his lean supervisor and technology team. They were so impressed with the ownership the frontline team took over the process (and the technology that enabled it) that they reached out to Dozuki to pilot our software at other facilities within the organization.
How are you using knowledge and access to create more agility and velocity? Can your team members contribute to learning from their valuable experience as you define your perfect process?
One interesting framework comes from Cambridge’s Automation Lab. Their team uses a model for operational resilience that has applicability here:
- Awareness: What is known about what might go wrong?
- Preparation: What preparation can be made in anticipation?
- Management: What decisions are needed to manage potential disruptions?
- Disruption Response: What can physically happen in response to disruptions?
Ask these questions early and often, so eventually they become internalized and instinctive.
Remember, Dozuki’s system is so agile, that if there’s a change that needs to be made within your training or documentation, it can be updated in real time, approved, and retrained on right away.
- - -
Ultimately, the global pandemic may have shakes things up. But operational resilience is here to stay. This value has been here since the dawn of our nation’s history.
If you want to protect your manufacturing business against events beyond your control, there is a way forward. Use a system that equips you to immediately respond and adapt to the changes in the processes, systems and environments.
Topic(s):
Continuous Improvement
Related Posts
View All Posts
Frontline Digital Transformation
Frontline of the Future: Part 1
8 min read
Historical Forces Impacting Manufacturing At Dozuki, we have our finger on the pulse of manufacturing trends. We believe it’s part of our mission to formulate clear...
Continue Reading
Continuous Improvement
How to Create a Daily Management System
3 min read
Do your frontline employees know if they’re winning or losing each day?The answer to that question is simple, but not easy.Michael Muilenburg spent 35+ years at 3M building a...
Continue Reading
Standard Work
Push vs. Pull System in Manufacturing: A Complete Overview for Optimizing Production
20 min read
Manufacturing companies must carefully balance expenditure and revenue to remain profitable. It might sound simple when put that way, but every manufacturer knows that the...
Continue Reading