
Industry News
5 min read
Practical COVID-19 Tips for Manufacturing
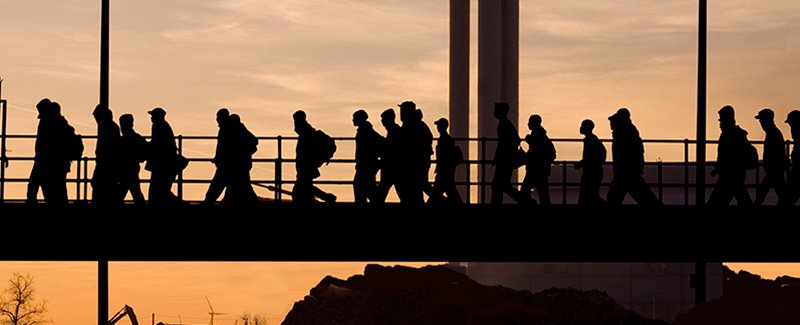
We are hearing a lot of great advice from our audience and customers about how to keep manufacturing and industrial operations running smoothly in the midst of a global coronavirus (COVID-19) pandemic. This article is intended to centralize a lot of this information so others can continue to operate while protecting the health and safety of their workforce.
Be Active with Shift Management
- Consider staggering shift start times and lunch breaks to avoid large numbers of people being at the same place at the same time. Separating shift start times can help reduce the impact if one of the shifts becomes affected.
- Reduce movement from one area of a facility to another by encouraging shifts/work areas to stay to themselves. This reduces the risk of germs moving quickly through the workplace.
- For those that operate on a day shift only basis, risks can be reduced by splitting into 2 or 3 shifts to limit contact between workers and teams, while keeping production levels up.
- Wherever possible, it might be necessary to run skeleton crews for the time being in order to follow expert advice on self-isolation and social distancing.
Review Necessary In-Person Staffing Needs
- Have support staff work remotely from home. To reduce the number of people in the building, it might be a good idea to have only essential operations staff remain in your facility. Doing so reduces person-to-person interaction and allows for suggested social distancing protocols.
- Only allow critical staff members to enter production areas to protect the health of your production team. Keeping staff roughly 6 feet apart from one another where possible to avoid transmission of germs.
- Use digital tools to your advantage. Many office functions can be accomplished remotely.
- Meetings can be conducted via phone calls or virtual meeting tools like Skype or Zoom.
- Email communication helps stay connected with one another.
- Chat tools like Slack or Teams also provide for more real-time communication needs.
Implement Rigorous Cleaning and PPE Protocols
- Use disinfection best practices to regularly clean all high traffic surfaces. This includes machines, tablets, handles, and other frequently touched surfaces.
- Place hand sanitizing stations throughout the facility to encourage use by all employees. These can be especially important in any cafeteria or food break areas.
- Designate a specific person or team to be responsible for cleaning and sanitation efforts.
- If available, consider distributing masks and gloves to reduce the chance of infection spread.
- Share expert guidelines on hand-washing and personal hygiene to protect the health of everyone, even beyond the walls of your facility.
Address Work Absences
- Take a deep dive into what levels of absenteeism can be hit before a build rate gets lowered, or worse, shut down for a period of time.
- Be flexible with your staff. Those with children are likely juggling school and daycare closures or some may live with high risk individuals. Many of these circumstances are beyond their control.
Communicate Openly and Frequently
- Things are changing from day to day, this can create a high level of uncertainty for your employees. By doing your best to share updates often, you can help alleviate their stress and concern.
- Keep communication brief and straightforward, focus on the necessary information. This will make everything easy to understand.
- Be aware that there is a high risk of people hiding their symptoms for fear of retribution. By creating a culture of open communication, you can help reduce the risk of spreading an infection to others.
- Remain calm and put yourself in their shoes. Employees are likely thinking of the health of themselves and their family, while also considering a slew of other factors. Approach communication from a place of empathy, you can help deliver a sense of safety during a time of need.
Develop a Plan if Someone Gets Sick
- Create and communicate a plan for your employees if someone is feeling sick. This is important to help avoid the spread of any contagious disease.
- In the unfortunate situation of an entire shift or team getting ill, fill-ins need to be prepared to do their work to keep operations running. To help these efforts, make sure documented procedures are up to date and able to be shared with those who need to be filling in temporarily.
- While we hope it doesn’t happen, it’s important to also have a specific action plan in place if there is a confirmed coronavirus case at your facility.
For even more actionable advise, OSHA has a helpful guide for preparing workplaces for COVID-19.
As industrial and manufacturing operations continue to shift based on global events, we remain dedicated to being a helpful resource for best practices and actionable advice.
Is your company implementing other measures to maintain production while protecting the health of employees? Please share them in the comments for others to learn from as well.
In the meantime, we wish you, your colleagues, and your families enduring health, productivity, and security in the months ahead.
Topic(s):
Industry News
Related Posts
View All Posts
Standard Work
Best Practices of Food Manufacturing Hygiene Standards
32 min read
Food manufacturing companies have a responsibility to their customers to maintain high-quality control measures and hygiene standards. These practices are necessary to ensure...
Continue Reading
Training
6 Common Manufacturing Facility Hazards & Effective Solutions
20 min read
Manufacturing facilities serve an important function in a country’s economy, as they create jobs, increase wealth through added value and taxes, promote trade, and support...
Continue Reading
Continuous Improvement
Gemba Walk Template for Digital Transformation
7 min read
Gemba Walks are an essential tool to understand the challenges of your manufacturing frontline. Each manufacturing facility is unique. The best way to solve your unique...
Continue Reading