
30 min read
What Makes a Good Digital Work Instruction Software?
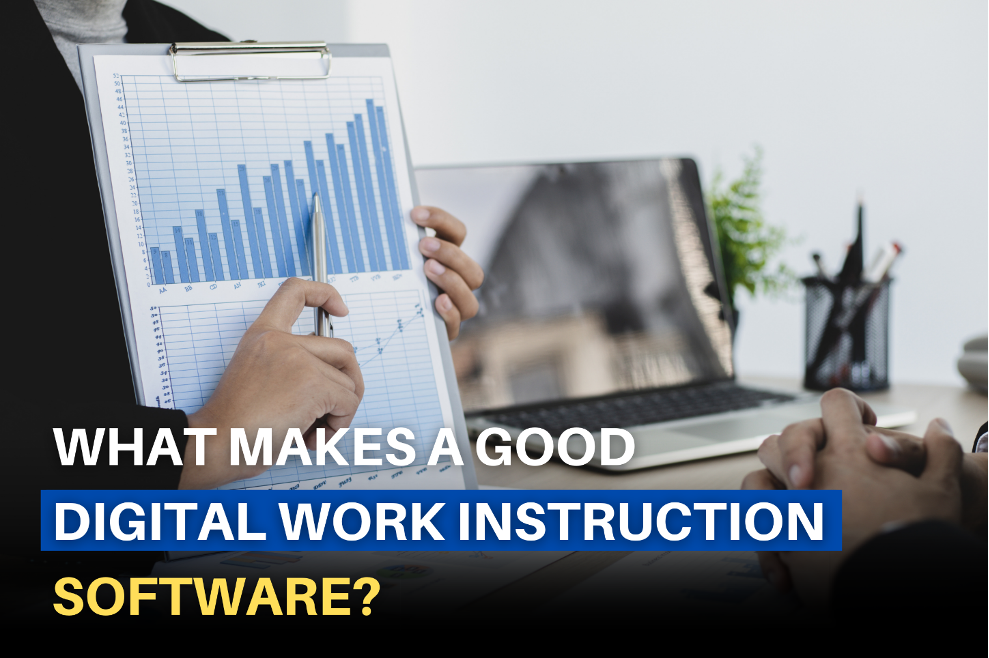
When Bob Dylan sang the lyrics, “the times they are a-changin’,” he probably never envisioned what the world would look like just six short decades later. The rise of digital technology has transformed just about every aspect of our lives, and there are no signs of the trend slowing anytime soon.
Those companies that operate in the manufacturing sector understand this better than most. Manufacturing companies face an ever-changing landscape that threatens to up-end those who aren't willing to ride the wave of progress.
These rapidly changing environments mean that companies must learn to adapt their processes and embrace advancements or get left behind. One of the biggest ways companies are doing this is by switching to digital work instructions.
Digital work instruction software is a way for manufacturers to easily document, update, and communicate process instructions for employees to use on the plant floor. By utilizing intuitive, interactive, and adaptable software programs, companies can gain many benefits while expediting the learning process for workers.
In this article, we will outline exactly what digital work instructions are and how companies who implement them can gain a competitive advantage. We will also discuss:
- What features to look for in digital instruction software
- How to ensure employees get the most out of the software
- How to write digital instructions effectively
- What questions to ask when evaluating digital instruction software programs
- How companies can decide which software program is best suited for their needs
Keep reading to learn more about why digital instruction software is the best way for manufacturing companies to stay ahead of the technology curve.
What Are Digital Work Instructions?
When companies use digital work instructions as opposed to old-fashioned paper instructions, they are using a much more streamlined and effective way to direct and instruct processes. Digital work instructions usually include step-by-step guides that are supplemented with visual aids, and contextual data, and may even utilize augmented reality (AR) or mixed reality (MR) applications.
Work instructions can be digitally created, easily updated, and centrally stored, making them easily accessible at any time and from anywhere. They are commonly accessed using a computer, a mobile device, or even with a wearable device. The flexibility in creation and ease of use makes digital work instructions a game changer for manufacturers.
The ways manufacturing companies can use digital work instruction software are as numerous and varied as the processes themselves. Because it is fast and easy to create custom instructions, companies can direct the use of these digital instructions to a wide range of scenarios, such as:
- Process, procedure, and assembly instructions
- Inspections, quality assurance, and control procedures
- Safety processes and procedures
- Maintenance procedures and checklists
- Training and development of workers
- Tracking and documenting performance, metrics, and real-time KPIs
Benefits of Using Digital Work Instruction Software for Business
The benefits of digital work instruction software can be easily recognized by companies who implement them correctly. And the great part is that workers, supervisors, and companies as a whole all stand to benefit.
More Adaptive Learning Processes
Research has shown that the way human beings learn is drastically affected by the methods used to communicate information.
For example, studies have shown that the more similarity that images and depictions in instructions have to their real-world counterparts, the easier they are for humans to process. Research also shows that humans learn better when information is presented in both verbal and visual formats because it stimulates different parts of the brain simultaneously.
A More Engaged Training Experience
Because digital work instructions can be self-paced and interactive, employees who use them become more engaged with the information.
It’s proven that training methods which include personalization, interactivity, and micro-learning processes drive employee engagement and increase knowledge retention. This means that workers will be able to master and understand processes and procedures faster and more accurately than they would with paper instructions.
Streamlines Workflows and Reduces Errors
When workers have access to clear, easy-to-understand instructions, it helps them to complete tasks more quickly and with greater accuracy. Digital work instructions allow users to easily access information when they need it, and visual aids help convey information in the most streamlined way possible.
Another benefit for companies comes in the form of real-time performance data and traceability. When workers use digital work instructions software, they gain the capability of tracking analytics which can be used to pinpoint areas that need improvement.
Easily Updatable
Change in the industry is unavoidable, so manufacturing companies need a way to easily adapt their work instructions to reflect updates to machinery or processes. With paper instructions, this would mean adding confusing addendums or republishing manuals entirely. But with digital work instructions, updates can be made instantly and reflected globally within seconds.
Saves Time and Money
There's no denying that digital means faster. And when referring to work instructions, that means faster to create, faster to publish, and faster in regards to employees' understanding and internalizing the information. For any company, processes that can be completed faster directly lead to savings of both time and labor, meaning more revenue left at the end.
Customizable and Sizeable
Digital work instruction software can be a benefit for companies of all sizes and complexities. Because the instructions can be created easily and quickly, the design can be customizable to the needs of the business. Whether you have ten employees or ten thousand, digital work instruction software can help streamline every process involved with the production.
Automatically Translatable
Many software applications offer the ability to translate work instructions into various languages instantaneously. This means that companies who have facilities in multiple locations or countries can use a single digital instruction for workers without the hassle of translating and publishing paper instructions in multiple tongues.
Capture and Share Tribal Knowledge
The skill gap in the manufacturing industry is a well-known and much-discussed issue. It's been theorized that by 2028 there will be approximately 2.4 million unfilled positions in the manufacturing sector. Older workers are retiring and taking their expertise with them and there is a shortage of skilled workers to replace them.
That's where digital work instructions can save the day. By allowing employees who have a detailed knowledge of processes to aid in the creation of the instructions, they are leaving a valuable legacy behind in the form of tribal knowledge. By digitizing that knowledge, companies will be able to share it with the next generation of workers.
What Makes A Good Digital Work Instruction Software Program?
Choosing which digital work instruction software is right for a company may seem overwhelming. For businesses to get the most out of their investment, it's important to investigate offerings beforehand.
Here are some of the most vital features that every good digital work instruction software application should include:
Easy and Intuitive Design
The entire point of implementing digital work instructions is to streamline the processes involved with instructing employees and operating machinery.
So creating the work instructions themselves shouldn't be overly complicated. Look for programs that offer customizable templates or drag-and-drop tools so creators don't get bogged down in the process. Ensure that using the instructions is intuitive and easy to understand so workers will be able to capitalize on the tool.
Reporting and Analytics Tracking
One of the biggest benefits of digitizing work instructions lies in the capability to track performance and instantly document results. Look for a program that offers in-depth, real-time reporting. Make sure that reports and analytics are clear and easy to understand so that efforts towards continuous improvements can be executed with greater success.
Visual and Multi-Media Embeds
Every digital work instruction software program should offer instant embeds for visual and multi-media aids. Workers who are offered clear, step-by-step instructions through the use of video, pictures, and 3D models will be able to better perform tasks and processes correctly and safely the first time.
Compatible with Mobile Devices
Digital work instructions should be easily accessible on a variety of platforms. Companies should look for applications that are compatible with mobile devices like smartphones or tablets, or wearable devices, such as smart glasses. Give employees the ability to access information from anywhere, at any time.
Customizable Permissions and Easy Updating
Look for a digital work instruction application that allows for customizable permissions both in the authoring process and on the plant floor.
This will help companies delegate the creation and authoring of process instructions to designated creators and ensure that standardized tools and formats are used every time. It should also allow customizable permissions regarding the assigning and executing of tasks.
Internal Communications
The ability to quickly and easily communicate problems, concerns, and feedback will help companies manage potential problems daily. Internal communications will allow employees to feel more comfortable asking questions and can help departments share information quickly and easily. There should also be the ability for supervisors to assign tasks and training to specific workers instantly.
Integrations
Having software programs that can be easily integrated with existing systems, such as an ERP or MES system, can solve problems instead of creating new ones. This allows for an easy transfer of information and data between multiple systems.
Scalability and Company Solvency
Choosing digital work instruction software should be a process that involves looking into the future. This means evaluating the needs of the business today and imagining how growth may change those needs in one year, five years, or even ten years down the line. Is this software able to grow with your company? And will the business that creates and oversees the software itself be solvent enough that it will be around to offer support all those years later?
Ensure That Your Employees Use the Software Effectively
A manufacturing company is only as good as its employees. And the same can be said for the tools used within a facility, including digital work instruction software.
Humans are, in general, resistant to change, especially when that change means the potential for more work and aninterruption of an established routine.
Because front-line workers are the ones who will be interacting with digital instructions the most, it’s important that companies take the right steps from the very beginning when implementing it, and support workers throughout the process.
This will ensure that the entire workforce is able and willing to use the software to the greatest benefit.
Here are a few considerations companies should take when implementing digital work instructions and introducing the program to employees.
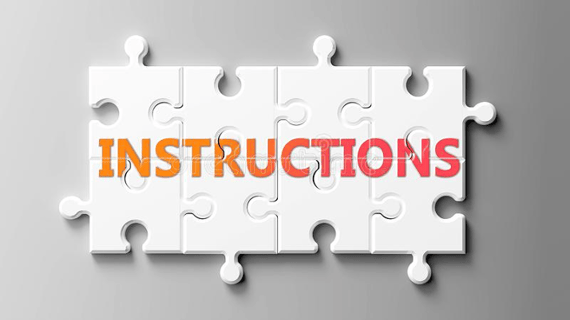
1. Involve Workers From the Beginning
Employees should feel like they're a part of the team, and that includes being consulted when changes are made. Workers are unlikely to embrace new technologies as beneficial unless they are given the information to understand how these new tools will benefit their lives regularly.
It’s more likely that they will regard this as an inconvenience unless they are involved with the process from the start and are made to feel like their input matters.
Designating upper management staff to be advocates for the process can help implement changes from the top. There should be one clear voice to avoid relaying a muddied or mixed message.
2. Answer Questions and Concerns
Nobody wants to feel like new information was sprung on them suddenly. Introducing the concept of a new tool as large as digital work instructions should be organized and premeditated. Clear and open communication with workers will help foster confidence and trust in the process and leave them less likely to feel ambushed.
A companywide meeting or departmental luncheons will leave workers feeling much more engaged and involved than a quick email or memo. If launching new digital work instruction software means as much to a company as it should, then employees need to feel that energy as well. Give them time and space to ask questions and voice concerns.
3. Allocate Time for Training
While digital work instructions are a training tool in and of themselves, employees will need time to learn how to operate and navigate the system. This may be the biggest turnoff for employees, who probably already feel like their schedule is full enough without extra work being loaded on top. That's why they need to understand that they won't be punished with the expectation to learn important new skills without being given the time and space to do so.
4. Provide a Clear Schedule For Launch
When it comes time to launch the new software, it should be done quickly and completely. It may be tempting to roll out new technologies slowly to test their performance and effectiveness. But with software that is designed to streamline the operational processes, having any combination of old and new information may be detrimental.
Allowing employees access to legacy systems after attempting to implement digital work instructions will create uncertainty, and confusion, and leave employees feeling unconfident in the process. It may even cause some employees to build resistance to the change altogether. Having a complete switchover in a single day will get much better results.
5. Gather Feedback Before and After Implementation
Gathering feedback from the workers who are using the digital work instructions is the best way for companies to gauge their success. Ask the right questions regarding their understanding of the processes, how easy or complicated the tool is, and if they have noticed any benefit. And allow workers the space to speak openly about their experiences.
Leveraging employee feedback will be invaluable during the early days and weeks of implementation. Companies must take the time to communicate with workers about what’s working and what’s not. Only then can improvements be made and instructions be tweaked for better performance.
6. Provide Support Throughout the Process
Whether it’s a go-to manager, technical support staff, or a help desk phone number, employees must feel like they’re not alone in this process. Providing a clear point of contact is essential for ensuring employees feel supported from day one. Employees need to know there’s someone there to offer a lifeline if it’s needed.
How to Write Work Instructions
Every manufacturing facility is different, and each process within that facility is individualized. That’s why digital work instructions can be so beneficial for manufacturing companies. But creating step-by-step instructions for every process involved with production may seem overwhelming.
The good news is that with digital work instruction software, it doesn't need to be. It's much easier to create and customize instructions digitally than it would be to draft paper manuals for each process or procedure. So let's discuss a simple flowchart that companies can use to draft their digital work instructions.
First, let’s outline what digital work instructions should be:
- Clear and concise, without any ambiguity
- Step-by-step instructions for processes
- Include a list of tools, equipment, or materials needed
- Easily accessible and centrally located
- Up-to-date with current procedures
- Standardized and consistent
- Include valuable and effective visual aids
With these requirements in mind, companies can follow these steps to create digital work instructions for individual processes:
1. Title and Introduction
The title and introduction should be clear and concise and refer exactly to the task that the instructions will explain. It will be the first thing the user sees and should include language that is easily searchable so that employees can find and access the information quickly and easily.
2. Include a List of Needed Materials
Employees should have every piece of the required information at their fingertips when using work instructions. This includes a clear list of every piece of equipment, tool, or material that will be required to complete the task.
3. Choose a Consistent Design and Format
Digital work instructions should serve the purpose of streamlining the transfer of information. This means that the look and feel of each instruction should be the same throughout, including text, font, and layout. This will help the user easily process the information without being overwhelmed with unnecessary additions and a muddled delivery message.
4. Step-by-step Explanation
Step-by-step guidance is the most important feature of work instructions. Be sure to break complex steps down further to prevent confusion and leave the user with no question about the sequencing of activities. For example, if more than one action is required for something, then more than one step should be outlined.
5. Add Graphics, Visual Models, and Multi-Media
The biggest benefit of digital work instruction software is the capability to enhance the design with the inclusion of clear and helpful visual aids. If the process being outlined is basic and doesn’t involve practical applications, the choice of graphics and stock imagery can be included, but be cautious not to over-burden the user with unnecessary inclusions.
When a step in the process involves actual machinery or equipment and outlines a task to be completed with such, it can be beneficial to include a visual image or video of the actual process being performed. This utilizes the training method known as, “tell, show, do.” But with digital work instructions, the “show” portion can be demonstrated through the use of multi-media.
6. Proof Read, Double Check, and Finalize
Because work instructions are created to help employees perform tasks safely and accurately, they must be accurate themselves. Read through the instructions to ensure every aspect is correct, clear, and concise. Look for sequences that may be further broken down or information that is missing or incomplete.
7. Test and Revise
Testing the efficiency and effectiveness of work instructions should be done in real-time, by an actual employee on the plant floor. There is no better way to ensure the clarity of the instructions than by testing them in action. Gather feedback regarding where instructions need to be fleshed out or simplified, and whether or not the expected result was obtained at the end.
Questions to Ask About Digital Work Instruction Software
Choosing the right software to transform work instructions from traditional paper methods to a more streamlined and advanced digital platform is a hefty goal. There are many factors that companies should consider to ensure they get the best tool for their individual needs and requirements.
Having a succinct understanding of the benefits that can be gained by implementing digital work instructions in a manufacturing facility might be reason enough for some companies to make the jump. But the decision, as with any important business decision, must not be taken lightly.
Asking questions and outlining the responses is one way to be sure that the software chosen is the right one for the job. Nothing would be worse than investing both time and money and then discovering that the tool chosen was not the best one to meet the needs of a company's situation.
Here are some questions manufacturers should ask and answer before choosing digital work instruction software:
What Are the End Goals?
Having clear and actionable goals in mind before choosing digital work instruction software will ensure that the choice is made with the desired results in mind. Is the goal simply to replace outdated paper instructions? Is there a defined productivity gain that should be met as a result? Are there improvements in safety, quality, or defect rates that stand out as vital gains?
Is the Software User-Friendly?
Work instructions absolutely must be user-friendly, intuitive, and easy to use. If employees cannot quickly and easily create, publish, and use work instructions then the entire point of the exercise has been lost. The software chosen should solve a problem, not create new ones with complicated or time-consuming designs.
What Needs Should Be Met?
Every company is different and will have individual needs regarding must-haves for digital work instructions. Some companies will require the use of AR or MR programs, while others may be able to use simple multi-media. Some operators may be able to hold tablets on the plant floor, while others may require the use of wearable devices so they can perform complex tasks with both hands.
Consider the needs of each process that instructions are required for and evaluate the software to ensure it meets the demands.
Does the Software Capture Real-Time Data?
One of the most valuable components of digital work instructions is the ability to capture real-time data. Whether it's recording who performed what task and at what time, tracking material use, or documenting KPIs, the variety of data that can be obtained is extremely useful for companies and should be the main consideration when deciding which software to choose.
Is the Software Able to Be Integrated?
Having software that allows for integration with multiple systems can make life easier for everyone involved with the manufacturing process. It will save time, money, and headaches in the long run because information and data can be automatically shared and transferred within systems.
Reducing Human Error when Using Digital Work Instructions
Studies show that 90% of workplace-related accidents and errors are due to human error. So it can be easy to lump all errors together and lay the blame on the individual worker. But when investigating the direct cause of those errors, it becomes clear that the fault of many of those accidents may lie within the systems themselves.
A poorly designed or faulty system that includes human intervention will inevitably lead to error at some point. Both humans and the system must work together harmoniously to reduce the risk of mistakes.
Having digital work instruction software in place can help manufacturing companies robustly reduce human error. Clear, accurate instructions are one of the best tools employees can use to perform tasks accurately and safely.
Here are some tips companies can use to ensure that employees who access and utilize digital work instructions have the best chance of performing tasks safely and without error.
Foster Communication
Creating and implementing digital work instructions involves multiple departments and numerous staff members at all levels. That's why having clear and precise communication is key to ensuring that work instructions can be utilized effectively. Every employee involved with the process, from drafting, overseeing, training, and operating, should have the same information and be able to communicate with each other easily.
Avoiding Multiple Interpretations
Digital work instructions should be created so that any user, regardless of their skill level, experience, or expertise, can use them to the same effect. Consider it like a textbook for beginners. Even though workers may have skills and experience going into a task, the work instructions should be accessible and understandable to anyone at any point in their development.
Easy to Understand Steps
The most important aspect of work instructions is that they clearly outline each step in a process. Ensuring that step-by-step instructions are defined, explained, and demonstrated so that the operator understands and can safely complete every action without any misunderstanding or guesswork will help to prevent accidents and errors.
Aim For Clarity and Conciseness
Worker safety should be a number one priority, so instructions must be clear and understandable. Avoid including an excess of technical jargon that can create confusion if it doesn't add any value to the explanation of a process. Keep language precise and outline steps clearly, without leaving any space for misinterpretation or ambiguity.
Craft Instructions With Safety Procedures in Mind
Each step in the instruction of a process should include clear language in regards to necessary safety procedures and protocols. Safety information should be highlighted or clearly called out so it won't be overlooked.
Dozuki | The Best Software Option for Continuous Improvements
Dozuki is the best choice for implementing digital work instructions. Dozuki can help companies streamline multiple processes, freeing up valuable time for more critical tasks and projects focused on growing a successful business.
Dozuki Gets Proven Results
Companies that switch to Dozuki for their digital work instruction software report proven and measurable benefits, such as:
- 40% reduction in employee training time
- 61% reduction in time spent creating documents
- 67% report improved communications
Dozuki offers a variety of features that can benefit a company’s bottom line. It can help track progress, assign tasks, and monitor process performance. Dozuki is the ideal choice for companies that need to increase the engagement of their workforce, train more efficiently, and focus on continuous improvement every day.
Here are just some of the features companies gain with Dozuki for digital work instructions:
Create Custom Work Instructions
- Easy to set up and manage
- Super intuitive interface and easy-to-use creator tools
- Standardize and document processes and procedures
- Easily update and communicate changes and updates globally
- Instantly embed video from anywhere
Workforce Training and Development
- Build comprehensive curriculums based on approved standards
- Auto-assign training and retraining based on programmable triggers
- Include testing for competency directly into procedures
- Track and document training and certifications
Focus on Continuous Improvement
- Improve processes and procedures
- Focus on production goals
- Build leaner processes and reduce waste
- Utilize analytics, real-time data, and performance tracking
Quality and Safety Management
- Ensure workers have access to only the most up-to-date instructions
- Built-in forms to expedite internal and external audits
- ISO compliance, OSHA training, and FDA process validation
Data Collection and Analysis
- Real-time view of training and production metrics
- Analyze valuable feedback to improve processes
- Full traceability of processes and results
Valuable Built-In Tools
- API integrations
- Easy communication
- Accessible mobile application
- Migration services
- Single sign-on (SSO) and security features
- Over 100 language translation options
- A dedicated team of experts to guide companies through every step of the process and beyond
Final Thoughts
Digital formats are faster, secure, and more efficient than their analog counterparts. The benefits that companies can gain when switching to digital work instructions are apparent.
Manufacturing companies, and businesses in general, should aim to create a culture focused on continuous improvement. This means that the goal should never be to sustain what is simply "good enough." The goal should always be to end each day better than the day before.
With the implementation of digital work instructions, companies can take huge strides toward that goal of continuous improvement. Creating easily updatable, accurate, and accessible standardized work instructions allows manufacturing companies to streamline their training and production processes.
This leaves more time, energy, and revenue to spend on projects that aim to improve and build the business. It also helps build a safer and more efficient working environment for all employees. Digital work instruction software helps position companies to better compete in an ever-changing and advancing technological landscape.
Topic(s):
Related Posts
View All Posts
Work Instructions
Benefits of Procedures & Work Instructions in Manufacturing
24 min read
Ah, the lingo of business. If there’s one thing that the world of business and industry loves, it’s terminology. Every industry has developed its own language, with specific...
Continue Reading
Product
How to Use Dozuki for Work Instructions
7 min read
Dozuki is the leading digital work instruction tool for industrial businesses all over the world. Our platform enables better employee performance by improving how you...
Continue ReadingA Complete Guide to Visual Management in Manufacturing | 2023
19 min read
Visual Management is a concept that can apply to everyday life - and life on the plant floor as well. As we go about our day, we encounter visual management cues in different...
Continue Reading