
Frontline Digital Transformation
13 min read
The Myth of Augmented Reality in Manufacturing
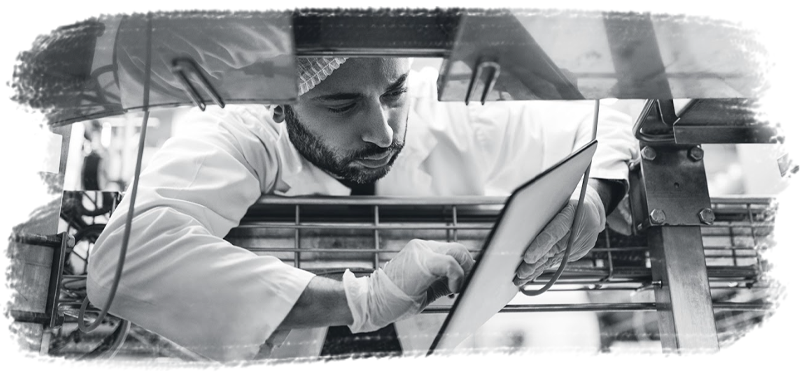
Do you remember Glass?
Not the epic 2019 finale to the superhero trilogy with evil genius Samuel Jackson.
I’m referring to Google’s failed launch of their smart glasses.
Back in 2013, the tech behemoth confirmed long held rumors about their augmented reality project. Google released the world’s first smartphone-like, hands-free, optical head mounted display. Wearers could communicate with the internet via voice commands, among other cool features.
As part of their launch, Google distributed a few thousand prototypes to qualified beta testers and influencers, dubbed Glass Explorers. My boss at the innovation studio where I worked was one of those people. And for a few months before the official release date, everyone at our office had a chance to test Glass’s features.
Can you guess what happened?
Google Glass made us all physically ill.
Anytime our voices triggered real time information like maps or weather data right in front of our eyes, we quickly developed the holy trinity of motion sickness: nausea, vertigo and a headache.
Imagine the frontline workers at your manufacturing facility feeling that way while operating hundred thousand dollar pieces of machinery.
Unsurprisingly, the smart glasses drew a lot of criticism and concern. Not only for its astronomical price ($1,500 a pair), but also because its use could violate privacy, safety and customer service regulations. Google eventually announced that it would stop producing the Google Glass prototype shortly thereafter.
What lesson can manufacturers learn from this failed augmented reality experiment?
Walk before you sprint.
And understandability, the appeal of augmented reality has excited businesses across industries. The technology shows great promise.
But when it comes to Frontline Digital Transformation (FDX), the hype exceeds the practical application. We believe the myth of augmented reality in manufacturing can be broken down into several components:
- The Lack of Confidence
- The Conflict of Environment
- The Obstacle of Confusion
- The Improbability of Scale
Below, we break down each of these issues, along with practical recommendations to help your manufacturing company achieve its transformation goals.
The Lack of Confidence
Hands free augmented reality devices are appealing for environments that want innovative solutions.
But the reality is, much of the current workforce lacks the skills and confidence to use them properly. AR devices sound appealing at first, but frontline workers have to interact with a new wearable device in completely foreign ways.
Unlike connecting a phone via bluetooth technology, augmented computer systems are highly complex. And with a lack of standards for how to build procedures, environments and other augmented reality content and events, company adoption would be costly and time intensive.
To quote from the bestselling classic, The Toyota Way:
“The notion of plug and play may work for hooking up a printer to your laptop, but most computer systems are far more complicated, and there is plenty that can and does go wrong.”
Consider the release of the first iPhone in 2007. Touchscreen devices have taken over a decade to gain widespread adoption and standardization. Pinch to zoom, swipe to scroll, double tap, only recently have these standardized and learned behaviors become the norm.
Given that most people don't interact with AR headsets on a regular basis, learning to interact with foreign technology may be an uphill battle for not only frontline workers, but also for the operation and training managers who are tasked with leveraging them for their intended use.
Don’t ask workers to run a marathon when they’re only learning to walk.
🔎 MYTH BUSTER 🔍
Are your leaders treating digital technology the same as hardware and machines? What will happen if your company picks tools that are too advanced or high tech for the frontline workers to adopt?
The Conflict of Environment
Dozuki teams perform site visits at plants, factories and other facilities every month. Our consultants lead training in numerous environments, from subzero temperatures to sweltering climates complete with their own metal forges. One observation our teams have reported back is, AR devices face a variety of challenges if they are to hold up to the extreme conditions present in many industrial environments.
Current AR devices allow the user to interact with two primary means of communication, which are gestures and voice commands. Researchers from Iowa State University have investigated the use of voice command as a technique, and while it does seem to be effective in certain situations, they concluded that loud industrial environments may cause interference with auditory feedback and verbal input methods.
The report found that personal protective equipment such as gloves, helmets and masks, may interfere with gesture recognition as well.
Additionally, many frontline manufacturing workers have loads that involve heavy lifting and strain from repetitive tasks.
Just imagine asking an operator to wear an AR headset throughout their physically exhausting shift in a 100 degree factory. They may look at you like you have three heads. Having to make a change like that to their work attire may interfere with balance, vision, focus and put workers under undue stress or even conflict with safety requirements.
Remember, the manufacturing industry benchmark is still using paper manuals and over the shoulder training. People are working with content written in the 1960’s, working with notes written on masking tape on the document in the big, dusty, heavy binder. Most operators are comfortable walking, so creating an environment centered around running is a huge ask.
🔎 MYTH BUSTER 🔍
Will making the leap right to augmented reality be a potential disruption for instruction and training? How might that negatively impact worker confidence?
The Obstacle of Confusion
Advanced technologies like augmented reality can certainly bring a new level of harmony to your operation. Especially from a recruiting standpoint. Once you get futuristic technology into younger workers’ hands and grab their attention right off the bat with the cool factor, working for your manufacturing facility becomes more compelling.
Keep in mind, however, while these solutions are part of many companies’ tech stacks, they are also a lot harder to use than people give them credit for. When a new technology is convoluted, it hinders your frontline’s ability to be proficient on the shop floor.
Productivity takes a backseat to cool.
Take a popular AR feature like dynamic information display. Among the main challenges for AR interfaces is how and when to direct user attention to the instructional content. If information pops up too soon or in the wrong context, this display method can cause confusion and create safety risks.
Say your shop worker is executing a changeover, but the visuals are only triggered when she is looking directly at a designated object or specific direction. If she works in a constantly changing industrial environment, displaying information with such visual cues is problematic.
Compare that approach to traditional digital instructions, where the information is not location dependent. The simpler technology choice prevails.
🔎 MYTH BUSTER 🔍
What if implementing new technologies and upgrading existing systems was only the beginning? Are you overlooking the heavy lifting of aligning digital change with your overall business strategy?
The Improbability of Scale
In a recent conversation on The Voices of Manufacturing Podcast, we sat down with Isaac Brown, Associate Partner at Landmark Ventures and has worked with countless industrial companies to help evaluate and deploy new technology.
On the topic of augmented reality in manufacturing, he summarized the scaling myth aptly:
“I think augmented and virtual reality solutions are part of the portfolio. And I think that they're useful. But I don't think they're going to solve all the problems. I think you're going to still need other sources of knowledge and training and work instructions that aren't AR solutions.”
Isaac suggests we consider the scaling issue from an enterprise standpoint. Because buying industrial technology is not like a traditional enterprise purchase that rolls out company wide. Augmented reality would likely begin at the site or regional level. Uniting the buying center for digital industrial technologies is something that still hasn't fully happened yet.
In fact, there are many categories of digital technologies where nobody's even sure whose product it is:
“Is this an IT product? Is it an HR product? Is it an EHS product? Is it a manufacturing product? Who has to pay for it? Who gets in trouble if it doesn't work?”
Even with the appointment of the Chief Digital Officer at an industrial company, the budget or authority to rollout across all factories is in short supply.
🔎 MYTH BUSTER 🔍
Does your factory really need to buy and implement the most high tech digital tools? Or would it be more transformative to thoughtfully integrate the right technology with your existing people and processes?
Practical Recommendations
Now that we’ve unpacked the myth of augmented reality, it’s important to note that we are not dismissing the technology entirely. AR may simply need some time before manufacturers are ready to dive into adoption.
If you want to focus on the next stage of your digital transformation and progress from there, here are several practical recommendations:
👭 Focus on people, not just equipment and process.
Your current system likely was not built for augmented reality. Don’t assume that merely dumping digital complexity onto your existing platform will solve your documentation and training problems. That may only make them harder to fix. You need to build a dedicated team to think holistically and evaluate and deploy digital technology on the frontline.
👷 Meet your frontline where they are.
Manufacturing leaders who have previously introduced advanced technology to their workforce know that the best chances for success are standardized interactions that workers are already familiar with. The tablet has become ubiquitous, both in people’s personal and professional lives, because of its user friendliness. Start there and, if it makes sense to upgrade to a more sophisticated technology, the team will be equipped. Without beginning from this place of familiarity, most workers will slow to adapt and might require constant training to use advanced tech effectively.
🙌 Seek approachability before ubiquity.
When plant managers are overwhelmed or intimidated by digital projects, they may think it’s a pipe dream. It’s a nice-to-have that will take years and a lot of work. As such, make your programs approachable by taking small steps. Aim to accomplish several smaller things first, then demonstrate how to do it on a larger scale. Remember, digital transformation is an evolution, not a revolution. Focus on the fundamentals before taking on an advanced system like AR.
🖥️ Unify your process documentation.
Before jumping into the digital deep end with augmented reality, look for a software tool that allows you to create, control and distribute digital work instructions from one place. This can be tricky, as some tools focus only on distribution when the control and management features really become more important as you scale your efforts. Get in the habit of capturing knowledge where the work is done, on the shop floor. Include photos and videos of expert workers executing tasks to make passing on valuable knowledge much easier. Learn more about how Dozuki enables visual learning, the dominant learning style for workers.
Conclusion
Ultimately, augmented reality can be a powerful and useful means of presenting information in a new way. The factory of the future very well may include frontline workers walking around the floors with smart glasses showing them the way.
But if the tool lowers confidence, creates environmental conflict, raises confusion and reduces the likelihood of scale, then there might be a larger organizational challenge to solve.
In your company, technology is only as powerful as the knowledge inside of it. All information still needs to be documented, accurate and easy to consume for the manufacturing workforce. Focus your transformation efforts by creating a body of digital materials that workers can become familiar with and learn to trust.
And from there, identifying technologies to share those instructions with can become much more attainable.
When the time for AR comes, manufacturing will be ready.
In the meantime, Dozuki is here to help you kickstart your digital journey.
Topic(s):
Frontline Digital Transformation
Kickstart with Practical Digital Solutions
Dozuki has helped hundreds of manufacturers enable their frontline workers with the knowledge and skills they need to perform to standard.
Related Posts
View All Posts
Work Instructions
The Cardinal Rule of Process Documentation: Read the Comments
5 min read
We’re told the cardinal rule of the internet is, “Never read the comments.” This catchphrase is used to warn users of the toxic parts of the internet. One minute you’re...
Continue Reading
Work Instructions
5 Instant Benefits of Digital Work Instructions
5 min read
Unlike other digital transformation projects, making the simple switch from paper-based work instructions, SOPs, and other documentation to digital work instructions provides...
Continue Reading
Frontline Digital Transformation
How 3 Leaders Tackled Key Workforce Challenges
4 min read
A recent survey by the National Association of Manufacturers underscores a pressing concern for manufacturing executives. Nearly 75% identify attracting and retaining a...
Continue Reading