
Auto Manufacturing Excellence
Fuel Frontline Performance
Set the industry standard in quality, safety, and productivity with a solution built specifically for automotive manufacturing performance. Create continuity by transferring the expertise of your senior workforce to the next generation of workers.
Partnering With The Best
More than 580 companies in 38 countries have partnered with us on their frontline digital transformation journey. Join us.
Driving Quality and Efficiency in Automotive Manufacturing
It’s never been more important to look for innovative solutions. Auto manufacturers need digital solutions to face the compounding challenges of recruitment, retention, and retirements. Industry leaders partner with Dozuki to capture internal expertise, create standardization, improve training, and increase retention.




Optimize Production Performance
Top automotive manufacturers are leveraging Dozuki to control standards, improve quality, and increase efficiency across their frontline operations at scale.
-
Reduce Quality Issues
Boost quality metrics by connecting people and process
With the globalization of production, auto manufacturers are under increasing pressure for consistency in finished product, regardless of production location. Meanwhile frontline operators are facing more complexity in their daily work and expectations of repeated precision in execution.
Dozuki drives better quality through in-process quality checks, real-time capture of critical production data, and the ability to scale standards across shifts, locations and language barriers. -
Control Standard Processes
Deliver updated standards to the frontline instantly
The production facilities of leading auto manufacturers operate as a synchronized environment of people, processes, and equipment. A single operator working outside of the standard can create ripple effects resulting in lost market share.
Our Connected Work Instructions ensure that every change to your standards are reviewed and approved by operations stakeholders (ex. production managers & process engineers), while operators are uninterrupted in working from the latest approved version. -
Increase Frontline Efficiency
Improve efficiency through connected frontline workers
The frontline workforce is stretched thin. Even new hires are expected to perform complex procedures that evolve by the shift, fill in for absent colleagues on different lines, and troubleshoot issues that few know how to solve.
Dozuki empowers workers to face these challenges with instant access to guidance at their workstation, so they can operate with confidence, and troubleshoot issues on-demand – across shifts, lines, and facilities. -
Continuously Upskill Operators
Manage workforce skills through ongoing standards training
Automotive innovation is transforming facilities and processes at a rapid pace. As continuous improvement drives change on the factory floor, it’s critical that frontline workers are able to keep pace and pivot when procedures are updated, or shift to new assignments fast.
Dozuki provides a system to manage the upskilling of your workforce, by turning your documented standards into training curriculum. Assign workers to complete training assignments based on recurring schedules, changes to standards, or other criteria.
Boost quality metrics by connecting people and process
With the globalization of production, auto manufacturers are under increasing pressure for consistency in finished product, regardless of production location. Meanwhile frontline operators are facing more complexity in their daily work and expectations of repeated precision in execution.
Dozuki drives better quality through in-process quality checks, real-time capture of critical production data, and the ability to scale standards across shifts, locations and language barriers.
Deliver updated standards to the frontline instantly
The production facilities of leading auto manufacturers operate as a synchronized environment of people, processes, and equipment. A single operator working outside of the standard can create ripple effects resulting in lost market share.
Our Connected Work Instructions ensure that every change to your standards are reviewed and approved by operations stakeholders (ex. production managers & process engineers), while operators are uninterrupted in working from the latest approved version.
Improve efficiency through connected frontline workers
The frontline workforce is stretched thin. Even new hires are expected to perform complex procedures that evolve by the shift, fill in for absent colleagues on different lines, and troubleshoot issues that few know how to solve.
Dozuki empowers workers to face these challenges with instant access to guidance at their workstation, so they can operate with confidence, and troubleshoot issues on-demand – across shifts, lines, and facilities.
Manage workforce skills through ongoing standards training
Automotive innovation is transforming facilities and processes at a rapid pace. As continuous improvement drives change on the factory floor, it’s critical that frontline workers are able to keep pace and pivot when procedures are updated, or shift to new assignments fast.
Dozuki provides a system to manage the upskilling of your workforce, by turning your documented standards into training curriculum. Assign workers to complete training assignments based on recurring schedules, changes to standards, or other criteria.
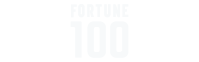
“
Before Dozuki, one checklist was pencil whipped by our employees, causing 2-8 hours of downtime 3 times per week. Now with Dozuki those lines have been running 3 weeks straight with zero downtime.”
–
Fortune 100 Heavy Equipment Manufacturer
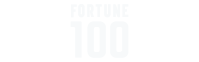
“
Dozuki gives technicians the information they need, where they need it.”
– Manufacturing Engineer
Fortune 100 Equipment Manufacturer
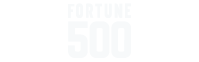
“
The Dozuki platform has allowed us to roll out fast, we can quickly share standards with hundreds of employees. The format is simple and easy to understand.”
– VP of Technology
Fortune 500 Transportation and Logistics Company
See the Dozuki Difference
We help you capture and standardize knowledge to easily distribute it across your workforce, building simple and engaging training programs so everyone has the same guidance. The result is faster, safer, and better manufacturing.
Connected Work Instructions
Create standardized, audit-ready procedures that are easy to author and quick to implement.
Go
Operational Training
Distribute accurate knowledge across your workforce and track training progress, all from a tablet.
Go
Continuous Improvement
Capture insights straight from the floor to assess performance and discover opportunities for improvement.
Go
Transformation Services
Lean on our expert team to create an implementation plan, run change management, and help you deploy.
Go
Additional Resources
View All Posts5 Ways to Fix the Skills Gap on the Factory Floor
7 min read
Properly addressing the skills gap takes time. But before you start forming an internal task force or scheduling strategy meetings, consider what impact you can have on the...
Continue Reading
Standard Work
How to Reduce Changeover Time with Standard Work Instructions
8 min read
Many manufacturers see reducing changeover time as a golden opportunity to improve operational efficiency and reduce waste. For good reason, a simple reduction in changeover...
Continue Reading
Continuous Improvement
How to Scale Technology Across Manufacturing Operations with 3M
42 min read
Most manufacturing companies don't have people dedicated to evaluating and deploying modern tools. At best, IT or HR takes responsibility for new technology and doesn't have...
Continue Reading