
Continuous Improvement
5 min read
The Ultimate Lean Glossary
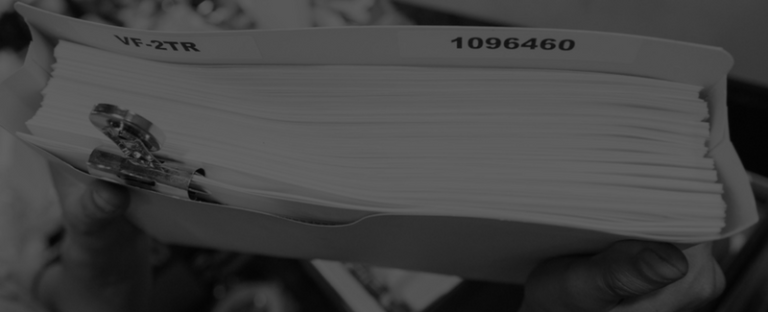
The world of Lean Manufacturing is full of acronyms and industry buzzwords. No glossary could encompass the full breadth of terminology, but it’s always helpful to have a consolidated resource to use as a reference.
Tip: Bookmark this page for reference when you need a definition quickly.
The Ultimate Lean Glossary
5 Whys
An approach to problem-solving that suggests asking “why” five times to get to the root cause of the problem.
Andon
A feedback system developed by Taiichi Ohno that allows floor operators to stop production and fix a mistake.
Autonomation
Otherwise known as Jidoka, the ability of intelligent machines or processes to stop themselves if a problem occurs.
Bottleneck Analysis
By identifying the points in production where the smallest throughput is enabled, management can try to remedy this obstacle and increase overall production capacity.
Continuous Flow
Compared to a batching production system, continuous flow moves the product through production without placing it into a holding area for later processing.
Continuous Improvement
A method for creating a culture where teams are invested in company goals and streamlining processes.
Cycle Time
The actual time to complete one production cycle of a product.
Gemba
Literally translated, ‘gemba’ means “the real place.” The concept that real work occurs on the plant floor and management should actively visit and evaluate operations there for better insights.
Heijunka
Otherwise known as level scheduling, this form of production uses smaller batches that mix product variants to make just-in-time production possible and avoid excessive batching.
Hoshin Kanri (Policy Deployment)
A methodology and policy that makes strategic goals known company-wide. This helps ensure that the actions of all employees are strategically aligned with the goals of the company.
Iceberg of Ignorance
An analogy used to represent the lack of knowledge that upper management can have of problems on the plant floor, keeping a majority of insights known only to front-line employees.
Industry 4.0
An industry concept that encompasses the innovations and solutions provided by internet-connected software and hardware (the Internet of Things, IoT).
Just-In-Time (JIT)
A methodology focused on reducing flow times with a production system, enabling operations to deliver goods to the customer in the right quantity and quality, exactly when they are needed.
Kaizen
A strategy for continuous improvement that focuses on small, achievable goals in order to improve a company.
Kanban (Pull System)
Signal cards and scheduling system that helps indicate when more goods are needed.
KPIs (Key Performance Indicators)
Metrics designed to track and encourage progress towards critical strategic goals.
Lean Manufacturing
Synonymous with Lean Production and first coined by the Toyota Production System (TPS) as a philosophy and structure for waste minimization.
Muda
A system for evaluating waste by asking what does and doesn't add value to the product from the customer’s perspective.
Poka-Yoke
Otherwise known as “mistake or error proofing,” poka-yoke is the process of eliminating all potential points of (human) error.
Pull Production
As opposed to push production, this production method relies on only producing goods when a customer has actually requested it, preventing unnecessary inventory.
Six Big Losses
Six categories of productivity loss that are almost universally experienced in manufacturing: Breakdowns, Setup/Adjustments, Small Stops, Reduced Speed, Startup Rejects, and Production Rejects
Six Sigma
A lean business methodology that uses strategies and tools to improve business capability by increasing performance and decreasing process variation.
SMART Goals
Goals that are: Specific, Measurable, Attainable, Relevant, and Time-Specific.
Standard Work
Living documentation that records and evaluates best practices, SOPs, work instructions, training materials, and more.
Takt Time
The pace of production cycle time that aligns with customer demand. To calculate, divide planned production time by customer demand.
Total Productive Maintenance (TPM)
An “all hands on deck” approach to preventative maintenance that empowers operators, not just maintenance personnel, to perform daily activities to help maintain equipment and prevent downtime.
Value Stream Mapping
A visual representation of every step required to bring a product from order to delivery. This shows the state of processes in an informative way the can often highlight opportunities for improvement.
Visual Factory
Data and insights conveyed visually, allowing for the quick dissemination of information.
Related Posts
View All Posts
Standard Work
What's Wrong with Standard Work?
8 min read
66% of companies fail in their attempts at Standard Work. This begs the question - what’s wrong with Standard Work? How can a seemingly simple methodology be so challenging...
Continue Reading
Continuous Improvement
Streamlining Production: How Lean Manufacturing Can Revolutionize Your Business
23 min read
Manufacturing is a delicate process. So many moving parts must come together just right if the aim is to produce goods of the highest quality in the most cost-effective way...
Continue ReadingThe Most Common 8 Wastes of Lean Manufacturing & How to Manage Resources
23 min read
Manufacturing is all about making the highest quality products at the lowest cost. Reaching that goal means searching for and eliminating causes of wasted time, wasted...
Continue Reading