
Standard Work
4 min read
Vienna Sausage: A Story of Standards and Tribal Knowledge
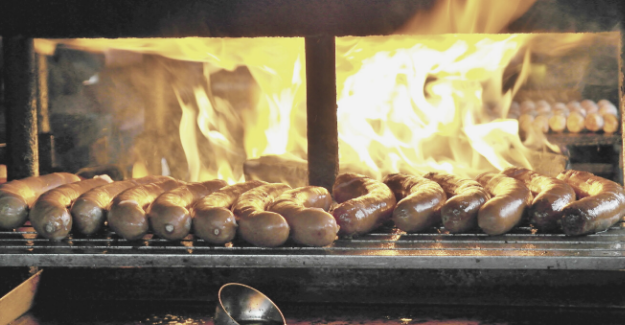
Imagine that you lost the ability to make your key product.
What if your core revenue driver was suddenly different...
And you didn't know why.
We recently came across a radio segment that outlined a similar problem that Chicago-based Vienna Beef had with their hot dog production. After the company made the transition to a new production facility, their staple product changed — and nobody knew why.
8 Decades, The Same Hot Dogs
The signature product of the Vienna Beef company is their natural hickory-smoked Vienna sausage. Each time a customer bites into one of these hot dogs, they expect the same consistency that the company had been reliably providing for 79 years.
Unfortunately, when production began at their new facility, product consistency took a turn for the worse.
With a long history of customer loyalty and product consistency, you can imagine the shock that management experienced when their famous dogs lost some of their renowned qualities. Jim Bodman, the Chairman of the Vienna Beef company had this to say about the problem:
“They tasted ok,” he says, “but they didn’t have the right snap when you bit into them. And even worse, the color was wrong. The hot dogs were all pink instead of bright red.”
Jim Bodman, Vienna Beef
Same Spice,Different Dogs
On all accounts, it seemed nothing had changed to the production process after the move to the new facility. The ingredients and spices were all the same, maybe it was the water source at the new facility? Was the new equipment impacting the taste?
Despite all their best efforts and hypotheses, the Vienna Beef company couldn’t resolve the consistency problem. After a year and a half of troubleshooting, a casual post-work conversation revealed the missing ingredient - inefficiency.
The Secret Spice: Irving
It turns out that a worker by the name of Irving was responsible for transporting uncooked sausages to the smokehouse at the old factory location. Because this facility was designed less efficiently than the new facility, Irving had to weave through a maze of machines and rooms, and up an elevator, to deliver the sausages to the smokehouse.
The combination of travel time and the heat of the rooms that the sausages travelled through was the reason for the flavor and color difference. During this trip, uncooked sausages were slowly warmed as they moved through the various rooms that led to the smokehouse. This allowed the smoke to better penetrate the sausages and reach familiar flavor profiles.
This trip to the smokehouse was the missing ingredient. Unfortunately Irving, the man responsible for the transport, didn’t move with the new facility.
The Impact of Tribal Knowledge
How does a highly successful company fail to meet standards after nearly 80 years of a good track record?
When the Vienna Beef factory moved locations, the company unknowingly lost out on some incredibly valuable tribal knowledge. While Vienna Beef moved location for good reasons, they underestimated their reliance on tribal knowledge.
Ultimately, the procedures that Irving were performing every day were not properly documented. So while the facility may have moved, his process knowledge did not.
Had Vienna Beef properly leveraged standardized work instructions to document their core processes, this mistake would not have occurred. Unfortunately for Vienna Beef, their over-reliance on tribal knowledge was discovered too late.
It took two years and a factory remodel to add Irving’s “secret ingredient” back to the sausages. While some may chalk this up to be a story of the cryptic nature of success, we think the story was fairly simple: Start recording procedures now so the fate of your factory doesn’t rely on the “Irving” at your company.
Related Posts
View All Posts
Industry News
The Manufacturing Skills Gap is an Opportunity
4 min read
There is a pending manufacturing skills gap impacting the United States workforce. Millions of positions are expected to go unfilled in the coming years, with reports...
Continue Reading
Training
What is Tribal Knowledge?
5 min read
Many industrial businesses have heard of the dangers of relying on tribal knowledge. But what exactly does tribal knowledge mean? How does tribal knowledge impact my...
Continue ReadingInsights from the Field: Training is More Than Onboarding
5 min read
I was recently on a trip to visit a manufacturing facility for one of our clients. My connecting flight didn’t arrive on time, which delayed my arrival and put me on a tight...
Continue Reading