
Frontline Digital Transformation
7 min read
6 Strategies to Maximize Worker Safety
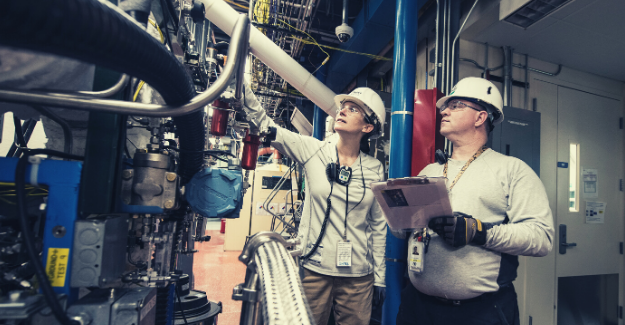
In industrial companies, workplace safety is the #1 driver behind many key decisions. Not only is safety essential for protecting workers, it’s also essential for consistent production. According to the U.S. Bureau of Labor Statistics, there was a 39% increase in fatal injuries resulting from machinery between 2017 and 2018. In addition to fatal injuries, 2018 saw 2.8 million nonfatal workplace injuries reported in the U.S. alone.
Safety matters. It’s the backbone of your operation. Not only does it maintain focus on your people, it also has a direct impact on efficient production. If an accident occurs, it can have lasting effects across your organization, including employee morale, machine failures, recruitment, and more.
How to Maximize Workplace Safety
There is opportunity here to be proactive in communicating safety procedures. Proper communication will build a culture where safety is prioritized at every level of the company. Below we’ve highlighted six practical ways to maximize workplace safety within your organization.
1. Keep the Facility Clean
One of the most common forms of accidents in the workplace are slips, trips, and falls (STFs)—accounting for nearly 15% of all workplace fatalities. While each day might fly by, and the need to work at the fastest possible speed to meet outputs, many accidents can be easily prevented.
In a facility where dozens of people operate dozens of machines, it’s understandable that tasks involving organization and cleaning are pushed to the back burner. To avoid unsafe situations, simple cleaning tasks can be incorporated into daily activities. Fast and effective tips include moving boxes that obstruct walkways, wiping up spilled liquids, or putting away materials when tasks are completed.
Safety can be improved by leaps and bounds when cleanliness becomes more of a focus. By acting on spills or obstructions as they happen, and encouraging each team member to pitch in, major advances are made. It’s always better to be proactive in these ways rather than waiting for a serious injury before taking meaningful action.
2. Conduct Regular Machine and Building Safety Checks
Routine safety checks are central to any safety-focused facility. By devoting a recurring date each month or quarter to spend a large amount of time to evaluate protocols that enforce safety. By conducting regular internal audits like this, it can help build a sustainable culture of safety, where every worker feels safe and responsible for the safety of others.
Some important things to regularly include in a safety check include:
- Are walkways clear of obstructions?
- Are employees using proper PPE where required?
- Are liquid spills cleaned up?
- Have all visible holes or trip hazards in floors been marked or covered?
- Are maintenance checks being performed?
- Are all emergency exits clearly marked and unlocked?
- Are employees aware of the process for reporting incidents?
3. Communicate Safety Protocols Clearly and Frequently
Any safety initiatives that fail to focus on how workers are trained to identify and control hazards in the workplace are almost certain to fall flat. A key in communicating safety protocols is making them easy to access and updated as conditions change. The likelihood safety protocols are taken seriously gets a boost when information is within reach.
Consider taking safety training out of the classroom and onto the floor—where jobs are actually done. When these protocols are shared in context, they become much more effective. This type of recurring safety training is most successful when it’s reinforced in regular intervals, resulting in a more proactive approach.
4. Create Preventative Safety Measures
The National Institute for Occupational Safety and Health (NIOSH) has created an industry standard for how to create preventative measures for known hazards—the hierarchy of controls.
This method provides a clear path forward for companies who want to make a meaningful impact on safety metrics, with the most effective methods listed at the top of the chain:
- Physically ELIMINATE the hazard
- SUBSTITUTE or replace the hazard
- ISOLATE people from the hazard through engineering controls
- CHANGE the way people work through administrative controls
- PROTECT workers with personal protective equipment
While the most effective long-term solution, elimination also can be difficult to administer for existing processes. If considering an elimination control, it’s best to do so while a process is still in its design or development stage. Isolation controls are often favored over change and protect measures because behavior changes are notoriously tough to sustain in the long-term. By removing the hazard from the source, as is true in isolation controls, it removes risk before it comes in contact with workers.
5. Prioritize Preventative Maintenance
After enough wear and tear, even the most expensive well-built machines come to a breaking point. The old adage “a dull knife is more dangerous than a sharp one” is applicable to industrial machines as well. As equipment runs close to recommended limits it’s important to pay close attention to both its condition and performance, otherwise it can easily cause easily preventable accidents.
Simple maintenance that minimizes safety risks includes regular inspection and lubrication. Not only do these tasks reduce the likelihood of accidents, they also extend the lifetime of essential operating equipment. Take the time to document these preventive maintenance procedures, since they are often done across long periods of time and the risk of losing expert knowledge when a worker leaves can decrease their impact severely.
6. Make it Clear How Incidents are Reported
In environments where documenting safety incidents is difficult, correlating accounts to other factors in the facility becomes highly difficult. This conflict in reporting leads to unreliable, inaccurate information. Creating changes to processes to mitigate and avoid future incidents based on unreliable notes is a losing proposition.
Giving workers a standard way to report incidents, especially minor ones, will lead to accurate information by which to enact future preventative measures. These standard processes for reporting will give visibility to management so that they can easily monitor problem areas. No, this doesn’t mean reporting all incidents to OSHA, it simply means communicating a clear way for workers to report internally in order to prevent future accidents and hazards.
Safety is Essential to Operations
A safe workplace is the backbone of your operation. Without it, you are prone to both accidents and machine downtime. As you consider your approach to safety, it’s important to remember the central role it plays in creating efficient outputs. Providing workers with a safe place to do good work will no doubt lead to success.
Topic(s):
Frontline Digital Transformation
Related Posts
View All Posts
Continuous Improvement
11 Essential Workplace Safety Tips for a Secure & Healthy Environment
24 min read
Workplace safety is a topic that businesses simply cannot overlook. For one thing, employers have an obligation to their employees to provide a safe work environment and to...
Continue Reading
Training
6 Common Manufacturing Facility Hazards & Effective Solutions
20 min read
Manufacturing facilities serve an important function in a country’s economy, as they create jobs, increase wealth through added value and taxes, promote trade, and support...
Continue Reading
Frontline Digital Transformation
OSHA's Recommended Strategies for Improving Safety Programs
5 min read
Workforce safety is non-negotiable for any industrial business. When mistakes can cause serious harm or bring operations to a halt, companies can’t afford to take safety...
Continue Reading