
Continuous Improvement
23 min read
A Deeper Look Into Quality Assurance vs. Quality Control in Manufacturing
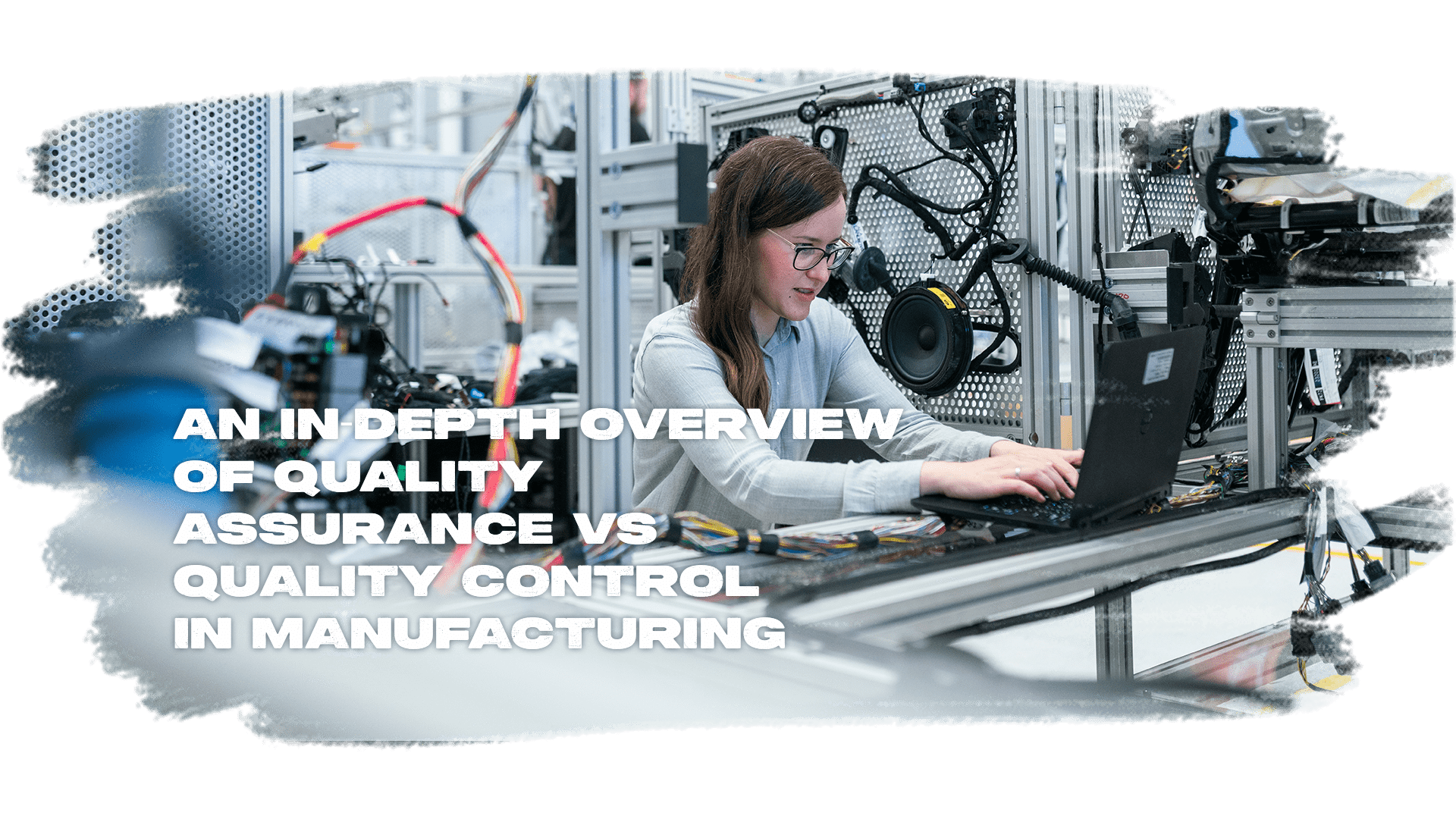
Manufacturing is taking raw materials and turning them into a product people need. Our industry makes the world go around.
But competition, which is in part responsible for companies constantly aiming to improve their processes and, therefore, their results.
Table of Contents
1. The Significance of Quality Assurance (QA) and Quality Control (QC)
2. Distinguishing QA and QC in Manufacturing Processes
5. Navigating the Process and Overcoming Challenges
6. Examples of Quality Assurance and Quality Control in Manufacturing
7. Benefits of Using Quality Control in Manufacturing
A better, higher-quality product is more desirable to buyers than an inferior product. Enter quality management.
Manufacturing companies use complex systems to maintain and improve the quality of their products. Both quality assurance and quality control play a part in the final look and performance of the product.
And while many people use them interchangeably (mistakenly), they have individual definitions and roles in manufacturing.
This article will take an in-depth overview of quality assurance vs. quality control in manufacturing, explain the importance of the role that each plays in the process, and offer suggestions on the tools that you can use to improve the overall quality management of your manufacturing company.
The Significance of Quality Assurance and Quality Control
Manufacturing uses a lot of technical terms to help define steps in the process. Two of the most common and most helpful are quality assurance and quality control. Both fall under the bigger quality management system, and while they may overlap at some points, they are distinctly different.
Quality Assurance
Quality assurance, or QA, is a process that falls under the umbrella of quality management and occurs as an overarching system designed to ensure that all parts of the manufacturing process result in high-quality products.
Processes, procedures, tools, and systems that come together to result in the manufacturing of products or the rendering of services include aspects of quality assurance to ensure that the outcome is satisfactory in its results.
Quality assurance considers the specifics of the design itself and the process used during assembly or manufacturing to ensure that output meets the requirements of the company, government agencies and regulators, inspectors, third parties, and the customers themselves.
Quality Control
Quality control, or QC, involves the job of inspecting and measuring the results of each process. When products fall outside of specified parameters, either because of fault in the process, the materials, the tools, and machinery used, or some other reason, quality control identifies the outliers, looks to pinpoint the problem, and then remedies the issue.
In essence, quality assurance and quality control is the difference between monitoring the materials, tools, designs, and processes used (QA) and systems designed to catch problems along the production line (QC).
Quality assurance is used to give the best chances of a positive outcome. When products don’t come out as expected, quality control takes over.
The Costs of Quality Failures
It’s hard to estimate how much is lost to quality issues because there are so many separate moving parts to every process. However, best guesses put the average percentage of losses at around 15%-20% of revenue, with the high end falling at as much as 40%.
These numbers underline the importance of implementing efficient and effective quality management systems from start to finish.
Distinguishing Quality Assurance and Quality Control in Manufacturing Processes
Distinguishing the difference between quality assurance and quality control starts by understanding the part they play in the quality management system. The former is an overarching idea that quality starts at the beginning of the planning process.
The latter is a safeguard against poor quality products making it out of the plant and to the customer and serves to identify problems that result in poor quality in the first place.
Processes versus Products
Quality assurance starts in the planning phase of any production line. Its job is to put the right designs, tools, and processes in place to ensure that every product that comes off the line is as high quality as possible. quality assurance is oriented on the processes themselves and the tools, materials, and supplies used in that process.
The goal is the prevention of defects and poor-quality results in the first place.
Quality control takes place at the end of each step in the production line and is designed to put a focus on the product itself. It involves checks and inspections designed to measure the quality of the products as they come off the line to identify defects and poor-quality results.
Quality control aims to identify products that fail to meet predefined standards and pinpoint the problem that resulted in those poor results so they can be rectified and improved.
Continuous Improvement Relies on Quality Management
It makes sense that quality management takes place at both the beginning and the end of the manufacturing process and throughout that process as well. Poor planning of any task is likely to result in a poor-quality outcome. That’s where quality assurance plays a part.
Manufacturing companies are using a preventative approach to quality management to ensure that the design, materials, tools, and processes are all chosen because they are the right formula for high-quality output.
Quality control is sort of fail-safe, put in place to measure the results of that output and identify outliers that fall outside of the quality standards.
Quality control identifies poor results and seeks to identify the cause of those results. This prevents defective products from reaching customers and saves companies money by correcting failed problems or processes.
Types of Quality Control
Now that we understand the difference between quality assurance and quality control in manufacturing, how do we execute them both? The answer lies in the tools of the quality management trade and the people responsible for implementing them.
Because quality control relies on checks, inspections, testing, and measurements of final products, those are the tools that you will see used in manufacturing plants. And these tools are needed throughout the process, not just at the end.
If a production process involves multiple steps and an error occurs after the first step, allowing that defective product to continue down the line to the very end is a waste of materials and manpower.
So, companies should apply a quality control check system that monitors each step of the production line to detect defects as soon as they occur. This also helps to pinpoint exactly where things went wrong.
Here are some of the most common tools and methods that companies use to execute quality control:
Statistical Process Control (SPC)
Statistics are a way to measure the specific metrics of each output. Using statistics helps companies quickly and efficiently identify products that fall outside the predefined high-quality requirements.
Six Sigma
Six Sigma was invented in the 1980s by the Motorola Company and has become a standard in manufacturing plants around the globe. It uses five key principles to help calculate the deviation percentage and failure rate of a product’s outcome.
Six Sigma aims to reduce total defects, minimize the variations in the process and output, and allow for continuous improvement.
Inspections
Inspection is at the heart of quality control processes. It allows manufacturing companies to set up a constant cycle of checks that can identify and prevent problems during every step of the production process.
Common types of inspections include:
Materials Inspection – A high-quality product requires high-quality materials. If there is a failure of the raw materials used during production, then the quality of the product is compromised from the very start.
These inspections vary depending on the materials used in the process. They might include things like freshness checks on consumable products or strength and durability checks for materials intended for non-consumable products. Materials inspection is one place where the processes of quality assurance and quality control tend to overlap.
In-Process Inspection – The inspections that occur throughout the production process are known as In-Process or During-Production Inspections (DUPRO).
In-process inspections are incredibly valuable for companies because they are designed to catch defects immediately. They also help to identify better which part of the production line is responsible for the failures.
Final Inspection – Once products make it to the end of the production line, they are subject to a final inspection. These inspections ensure that no defective, poor-quality products make their way out of the plant to the customer.
Since defective and recalled products can cost companies millions (or billions) of dollars in lost revenue, legal fees, and lawsuits if allowed to reach the public, the final inspection is one of the most important parts of the quality management system.
Shipping Inspection – The job of the quality control manager isn’t finished once products pass the final inspection. The shipping and logistics department are subject to their inspections, designed to ensure that products reach their final destination the same way they left.
Poor shipping processes and errors can result in a high-quality product turning into a low-quality product due to weather, breakage during transit, or spoilage because of faulty temperature or climate control.
Types of Quality Assurance
Quality assurance and quality control in manufacturing is a two-step process. The QC portion is designed to measure the results of the production process against a set of predetermined measurements and regulations.
The quality assurance portion is intended to reduce the percentage of products that are deemed defective by monitoring the tools and processes that result in that final product.
Quality Assurance is typically a four-step process and includes the Pre-Production Inspection (PPI), the During-Production Inspection (DPI), the Pre-Shipment Inspection (PSI), and Container Loading/Loading Supervision (LS).
Together, these Quality Assurance steps help to ensure the very best chance of high-quality results and reduce the chance of defects making it off the line.
Pre-Production Inspection – The inspection before production begins is a big part of the QA process. Checking the designs, materials, and processes used in production before any expenditures occur is the best way to ensure that results fall within the required specifications.
During-Production Inspection – Once production begins, the During-Production Inspection takes over. These inspections occur at multiple steps along the production line and pinpoint specific areas needing maintenance or improvement.
Even production processes that are limited in the number of steps should include DPIs early on to check the integrity of the batch before completion. If a defect is detected, losses can be minimized instead of amplified.
Pre-Shipment Inspection – The Pre-Shipment Inspection is sort of like a fail-safe. It gives manufacturers one last look at products before they leave for shipment and delivery. And it’s designed to inspect the quality and performance of the shipping process, including packing.
Container Loading/Loading Supervision – Inspections during the container loading process are vital for ensuring products arrive at their destination undamaged. If shipments are loaded incorrectly, it opens the door to damage and defects and puts plant and transportation workers at risk.
The Overlap
It should be clear now that quality assurance and quality control involves two individual parts of the quality management system – and that they overlap in many areas. The difference is that QA processes are planned to prevent errors, and QC occurs throughout the process to identify those errors.
Navigating the Process and Overcoming Challenges
Continuous Improvement is a concept that manufacturing companies apply to drive results upward constantly. Quality management is vital to that process and helps manufacturing companies reach that goal more consistently.
But that doesn’t mean that quality is without its challenges. When discussing quality assurance vs. quality control, understand that each comes with its own challenges and difficulties. Let’s look closer.
A Lack of Standardization
It’s vital that manufacturers have a documented and polished SOP, or Standard Operating Procedure, in place. The SOP should include detailed information about every step in the production process, focusing on providing the highest quality output possible.
If quality is not included in the SOP, or the SOP is inconsistent in its definitions and application, the results will likely be variable. These variables lead to poor quality results and potentially higher production costs.
Legacy and Siloed Systems
There’s been a lot of progress in the manufacturing sector and incredible changes that have occurred rapidly over the past several decades. These changes have put companies at risk – especially if they use outdated legacy systems that don’t provide an overarching picture of quality operations.
Siloed information doesn’t serve the quality management system and can lead to poor communication between departments.
Training Challenges
There’s no getting around the people portion of quality management. Workers run the processes, tools, and equipment that result in output, and their intervention can be either a hindrance or a benefit to production quality.
If employees are poorly or improperly trained or lack an understanding of the importance of quality management, then quality will likely suffer as a result.
Over Documenting
Documentation is a great way to monitor quality and is often important in terms of following certain governmental or regulatory requirements. But companies can get tied up in the minutiae of over-documentation, wasting time and resources.
Documentation should be done as a means to an end – to identify potential problems and find solutions. If employees feel overwhelmed by documentation requirements, they may lose the big picture and lose focus on the ideals of quality management.
Poor Communication
The quality management system comprises many moving parts and likely includes a group of Quality Managers responsible for overseeing inspections, checks, and testing of specific departments.
Having a narrow view of their role in the quality management system can lead to a failure to communicate - with each other, with upper management, and with floor-level employees.
Since each plays a part in the QMS, the interplay between them needs to be open and communicative. It should include brainstorming, problem-solving, and implementation instead of just monitoring and documentation.
Lack of Focus on the Customers
The entire goal of a QMS is to provide products to consumers that are of as high a quality as possible. Remaining competitive in a market and maintaining customer loyalty are key to success for any company, and quality is a huge component of both.
Employees can quickly lose sight of this end game when they get stuck in the day-to-day activities of quality management.
Examples of Quality Assurance and Quality Control in Manufacturing
Quality assurance and quality control in manufacturing involve overlapping processes and procedures designed to meet one goal: higher quality products and fewer defects. Each of these arms of the Quality Management System uses its own tools and standards to help identify potential problems. These tools are what allow the process of continuous improvement to occur.
Process Checklists
Process checklists are a way to ensure that everything used in the production process is in line with expectations and requirements before production begins. Reducing the chance that any part of the process lies outside of those requirements will prevent defects before they can occur.
Checklists also help employees focus on providing high-quality results and reduce the chances of human error, faulty machinery, or poor processes.
Project Audits
Project audits check the progress of production in real-time. These audits are responsible for providing data, measurables, and statistics that employees can use to predict potential problems before they occur or identify gaps in the quality system.
Methodology and Standards Development
Every process needs standards and methodology to be consistently successful. When everyone operates off the same standards and understanding, results will be closer to expectations. Quality Management should be a driving factor in every aspect of the methodology to ensure that processes are designed to provide the best results every time.
Inspection
Inspections are the driving force of quality control. They provide a way to measure results against predefined standards and ensure that output falls within those specified parameters.
Inspections are done throughout the production line at every step to help identify failures as they happen. This means pinpointing potential problems before they can escalate and preventing huge losses because of an oversight in the quality management process.
Testing
Testing can be done in numerous ways and will vary depending on the industry and the product. Still, it has one primary intention: to ensure that products and materials perform as expected.
Testing might happen pre-production and involve the raw materials used in the process. It might happen during production and involve individual parts of the process, the machinery or tools used, or the output itself. And they certainly should happen post-production to ensure that products meet standards and operate as required.
Deliverable Peer Reviews
The human aspect of manufacturing includes many variables that can affect the quality of output. Humans are responsible for numerous parts of the production process, and they can introduce the possibility of error into production that can easily result in poor quality or defective products.
Peer reviews, oversight, and supervision are integral to the Quality Management System. Identifying employees who are under-trained, poorly performing, or reckless on the plant floor can prevent more than defects but also injury, downtime, and even loss of life.
Benefits of Using Quality Control in Manufacturing
We’ve explained the intricacies of quality assurance and quality control and touched on the potential benefits. For companies involved in the production of products, or even non-tangible services, quality management is more than beneficial – it's crucial. Here are a few reasons why:
Customer Satisfaction
At the top of the QMS pyramid is the customer. Every action taken from a quality management standpoint should include a thought of how it benefits the customer in the long run.
The entire point of manufacturing is to provide a product that meets the consumer's needs. And consumers have high expectations regarding the products they purchase. Maintaining satisfaction for those customers will keep them loyal and increase returns and revenue when they keep coming back for more.
Reputation
Companies work long and hard to build a reputation. It only takes one setback to destroy or permanently damage that reputation, and quality can play a part in that. A product recall that makes the news can harm a company’s public image, lead to expensive lawsuits, and forever damage public trust.
Increased Productivity and Efficiency
Continuous improvement is the idea put into practice that we can always do better. Quality Management plays a large part in that goal by preventing losses before they occur, identifying problems that need intervention, and pinpointing areas where improvements are needed. These improvements will inevitably lead to increased productivity and greater efficiency in the process.
Cost Reduction
Poor quality output quickly eats into a company's profit margins. Whether the losses occur on the plant floor in the form of lost products or materials or happen after the customer receives a damaged or defective product, those costs add up. Focusing on preventing defects before they occur and identifying them before they reach the consumer can save companies a significant amount of cash.
Innovation and Improvement
Quality management activities can illuminate parts of the process that are ripe for innovation. There have been incredible advancements in automation, smart tools, integrated management systems, and more in today's manufacturing industry. QMS can help identify areas where implementing new technologies and processes will make the biggest difference.
Final Thoughts
The topic of quality management, quality assurance and quality control in manufacturing is a big one in the industry. Quality has always been an inclusion in the manufacturing process, and for good reason. It helps companies stay competitive. It provides a more satisfied and loyal customer. It builds a positive reputation instead of a negative one. And overall, it helps companies cut costs, keep losses under control, and strive for that ideal of continuous improvement.
Advancements in the way that manufacturers do business have changed the way that businesses are thinking about quality management. Implementing technology, automation, and integrated data systems can only help bolster quality management activities. Companies that take advantage of these innovations and invest in furthering QMS activities will excel in the future.
Manufacturing companies are riding a wave of growth and improvement right now, partly driven by these advancements. Technology can help companies maintain that competitive edge and keep up with a rapidly changing landscape. But they must apply that technology and innovation to all parts of production. And every part of production should be designed with quality management at its core.
Topic(s):
Continuous Improvement
Related Posts
View All Posts
Standard Work
Quality Assurance in Manufacturing: An In-Depth Guide to Achieve Customer Confidence
23 min read
It’s time to talk about quality. In this industry, quality is everything, and competition between manufacturers is fierce. Table of Content 1. Key Principles of Quality...
Continue Reading
Standard Work
5 Ways To Improve Quality Control in Manufacturing
22 min read
In manufacturing, quality is everything. Businesses need to focus on creating products that are high quality enough to meet or exceed the customer's needs if they want to be...
Continue Reading
Continuous Improvement
Mastering Total Quality Management in Manufacturing (TQM) | Strategies and Insights
28 min read
If there’s one consistent thread that unites every manufacturer worldwide, it’s quality. The need to produce a quality product that meets or exceeds the needs and...
Continue Reading