
Frontline Digital Transformation
8 min read
Frontline Of The Future, Part 5
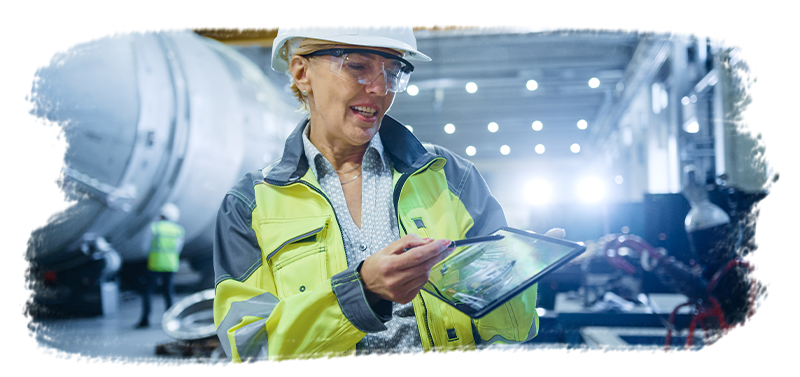
In any type of manufacturing, lubrication is essential.
It reduces wear, minimizes friction, dampens noise, dissipates heat, and absorbs shock on machine components.
Human beings operate similarly. Except instead of using silicone oil, they use communication. That’s what helps us navigate change and transformation. Communication is lubrication for manufacturers, especially during times of rapid change.
Along the journey of digital transformation, the culture is likely to resist change, so being thoughtful with how you communicate is paramount. Without efficient methods of sharing the right message at the right time to the right people, creating the frontline of the future will always feel like an uphill battle.
We often observe a lack of communication between functions at manufacturing companies we work with. It’s a significant barrier to the flow of knowledge and ability of the frontline workforce to feel empowered. Here’s a snapshot of what that gap looks like:
Exchange: Communication is limited to in person and written notes.
Format: New process updates are distributed to binders, without validation on receipt.
Channel: Operators, supervisors and management primarily communicate via email.
Dozuki recently compiled our “best of the worst” contest, which is a compilation of really bad work instructions, training, and other poorly communicated materials we’ve collected over the years.
We geek out on these case studies, but it’s all in good fun. Most submissions come from site visits with customers who haven’t implemented Dozuki yet, so we always keep the names anonymous to protect the innocent.
Here are few highlights:
“People are working with content written in the forties, working with notes written in the seventies, held together by dusty, heavy binders from the nineties.”
“Some instructions are only pictures. They're not poorly written; they're not written at all.”
“Instructions will casually say something can cause serious injury or death, but the text is cut off on the screen.”
Hopefully, your work instructions, procedures, and other documentation practices don’t resemble any of those communication mishaps.
We foresee the future of manufacturing communications as such:
To keep information flowing at your manufacturing operation, here are our recommendations:
Make giving feedback seamless and universal
Most frontline operators don’t have email accounts. They’re on the floor all day, where they are running production equipment during their working hours. And unlike knowledge workers who operate from offices, they don’t have company sanctioned devices. Supervisory roles will, but not operators.
And this is bad for communication. Operators are cut out of the feedback loop, which is detrimental to being able to improve processes. Imagine the operator who sees a process they believe is wrong.
If they aren’t empowered to help, it’s possible they will perform tasks the right way, but without updating the tablet. Dozuki is built around giving frontline workers the ability to give feedback seamlessly. At any point, their voices can be heard and used to improve the work
Crowdsource technical problem solving
When Dozuki first launched our Answers feature, we were inspired by Stack Overflow, a popular question and answer website. Wouldn’t it be great to have one of those inside your company?
Answers eliminates the need to tap coworkers on the shoulder, interrupt their work, and answer questions about the strange sounds coming from a machine. Now frontline workers can simply post their questions and crowdsource the support they need.
No email address required. No need to share logins. Every employee can participate.
Don’t start with why, but with how and what.
In our recent episode of The Voices of Manufacturing, podcast guest Patrick Graupp taught us a communication lesson. He suggested we “start with what”. Show operators the job from start to finish with no details.
First you do this, then this. Then, you perform it again. Here’s what you do and how you do it. Finally, now that they’ve seen it from start to finish twice, you do it again, and then you say, here’s the why in the process. Then you have permission to talk and let loose on details.
This approach develops an interest in the why. You create a foundation to drive continuous improvement and better the process within the constraints. If you start with what and how, you show a lot of respect. You build the story and value them as an individual.
- - -
Let’s close with a memorable quotation from William Whyte, the imminent sociologist and organizational analyst. He wrote perhaps the most famous proverb on the topic in his bestselling book, The Organization Man.
“The biggest problem in communication is the illusion that it has occurred.”
If you want your operations and workforce to grow more efficient, treat communication as the best industrial lubricant on the market.
Doing so will help you navigate change and transformation as you create the frontline of the future.
Our next lesson is Part 6.
Topic(s):
Frontline Digital Transformation
Related Posts
View All Posts
Frontline Digital Transformation
Frontline Of The Future, Part 3
5 min read
Accessibility Creates Profitability Manufacturers that don’t provide broad access to essential knowledge are at a significant deficit. This form of content debt comes at a...
Continue Reading
Work Instructions
The Cost of Bad Work Instructions
10 min read
Bad work instructions are the norm. Documentation is often created to check a box for audit or compliance purposes. But once completed, those work instructions get trapped...
Continue Reading
Frontline Digital Transformation
Frontline of the Future: Part 1
8 min read
Historical Forces Impacting Manufacturing At Dozuki, we have our finger on the pulse of manufacturing trends. We believe it’s part of our mission to formulate clear...
Continue Reading