
Frontline Digital Transformation
7 min read
Frontline Of The Future, Part 6
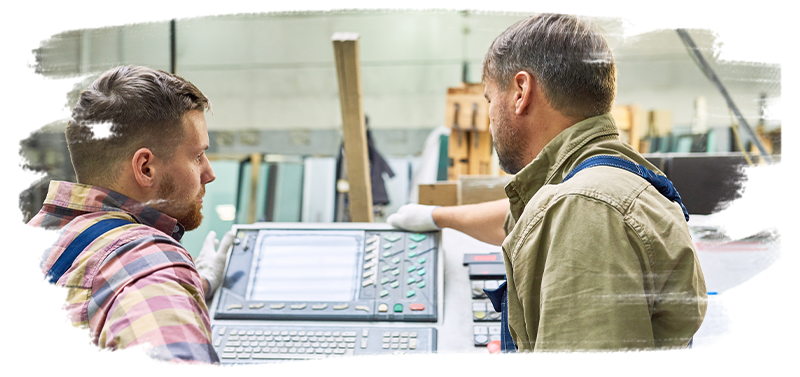
How To Staff Your Front Line Without Excel
One of our customers, a plant manager at a chemical manufacturing company, made this observation:
“Getting the time to train every crew when you're on 24/7 can be a challenge, and tracking it is even harder. But am I a secretary or an engineer? I'm entering data all the time.”
This complaint is more common than you might think.
Everyone from engineers to human resource managers to plant supervisors find themselves trapped in spreadsheet land. They’re tracking the training status of every employee on the factory floor using outdated Excel files.
These Excel training matrices are impossible to keep up to date. Even a facility with a hundred workers, all of whom have to be trained (and retrained) on a dozen procedures a piece each year, we’re talking thousands of columns and rows.
Even with effective job shadowing, that still doesn't lend itself to visibility intowho is properly trained.
Just recently, a member of the Dozuki team was conducting a site visit at one of our medical device manufacturing clients. During this training audit via the customer’s “homegrown training tracker,” their compliance team found outdated records which could have led to a service delay penalty for an upcoming ISO audit.
This is not an isolated incident. We’ve encountered this situation at hundreds of manufacturing organizations. See if any of these characteristics of poor analytics sound familiar to you:
What is the format? Data is stuck in paper forms.
Who’s been trained? Data is manually tracked in spreadsheets.
Where are the records? Only available at select workstations.
Implementing a proper training reporting system can avoid this costly mistake, helping you keep track of who needs to get up to speed and when. What’s more, to circle back to our previous article in this series on communication, data insights need to be shared proficiently and prolifically with company leaders.
We’re not talking paper sheets shared in bulky binders. Not spreadsheets shared via email or shared drives. Here’s what’s coming next around data analytics for the Frontline Of The Future.
To ensure your data analytics are advancing your manufacturing operations, here are our recommendations:
1. Expedite and simplify learning with data
Dozuki can capture all kinds of data from your frontline operators. Easily capture per step timing, overall process timing, really anything you want to collect from your operators.
For example, if your workers have to write down a serial number of a machine, or the torque value of a bolt, there’s no need to write those metrics down on paper, carry them around the plant, and calibrate them against the work order. With Dozuki, only one step at a time is presented.
This focused view ensures workers enter required fields before moving onto the next step in a process. This simple but essential metric makes pacing training much easier and simpler. Both for the trainer and trainee.
2. Use data from digital forms for sign offs
It’s imperative to include supervisor sign offs within steps. The old way of running back and forth to managers for approval is inefficient and unreliable.
But now supervisors receive pings on their devices, they come over to someone’s work station, sign off, and then push the process forward. This ensures a second set of eyes reviews the work, but doesn’t hold up the line for unnecessary amounts of time.
Remember, manufacturing workers are non unlike pit crews for stock car racing. Those teams are measuring their changeovers in seconds, and manufacturers measure in minutes. It adds up, a few minutes can halt production.
3. Capture timing data for continuous improvement
Do you know exactly how much time it takes each of your frontline workers to execute their tasks? Dozuki customers do.
The frontlines of the future capture metrics on all critical processes —both the individual steps, and the entire process itself. Wouldn't it be useful if you could analyze that data in real time?
Perhaps step four of ten at your beverage processing facility is a time suck. It takes forty minutes when it should only take five. Now you can send someone to the production line to watch what’s going on. Supervisors can download timing across all work orders to learn where friction points are, where time can be improved and what causes time increases.
Better yet, learn which operators are performing tasks in half the time, and whether or not that’s a good thing. Dashboards in Dozuki dashboards are granular and can be optimized to your heart’s desire.
Or you can work with our Services team, who can help advise and structure your data analysis needs.
- - -
As you can see, standardizing processes isn't enough. Doing training isn’t enough. Communicating the approvals isn’t enough.
You also have to test if employees are competent in the work at hand, and monitor who is trained on what. Dozuki ensures you have full visibility into who is trained to the standard. Ultimately making sure your audit trail will be airtight.
With proper manufacturing data analytics, you have the heartbeat of your processes at a glance. You can manage tracked and untracked processes, hit and missed goals, average cycle times, or whatever other metrics are mission critical for production.
Time to move on to Part 7!
Topic(s):
Frontline Digital Transformation
Related Posts
View All Posts
Frontline Digital Transformation
4 Ways Digital Tools Improve Quality
9 min read
Twenty years ago, digital tools were “a thing.” Now they flow through all things. To some degree, every manufacturer is now a digital company. And with the right modern...
Continue Reading
Frontline Digital Transformation
Frontline Of The Future, Part 3
5 min read
Accessibility Creates Profitability Manufacturers that don’t provide broad access to essential knowledge are at a significant deficit. This form of content debt comes at a...
Continue Reading
Industry News
Dozuki and TWI Institute Partner to Empower Frontline Workers
4 min read
We’re excited to announce a powerful new partnership between Dozuki and the TWI Institute, combining our strengths to empower frontline workers with effective, hands-on...
Continue Reading