
Industry News
6 min read
How Digital Tools Enable Rapid Communication for Manufacturing
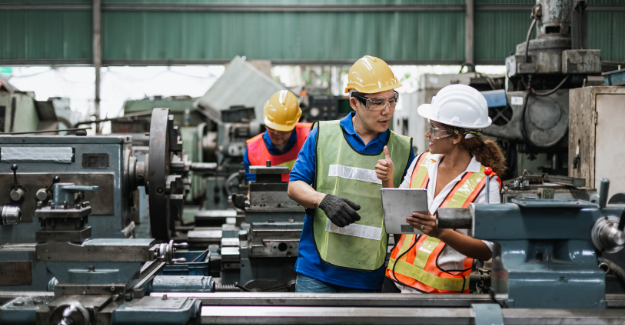
The ongoing global COVID-19 pandemic has forced companies of all types to rapidly update policies and procedures governing how they share information in response to a world that is constantly changing around them. For the manufacturing sector in particular, their workforce is more spread out than it has ever been.
Many knew that telecommuting was the future of the workforce in this country — it's just that few could have predicted that "the future" would have come along quite as quickly as it did. In April, at the height of the first wave of the pandemic, a massive 51% of people were working from home. While that number has dropped to 33% as of October, it's still enormous, creating a challenge for the manufacturing sector in particular.
At the same time, communication remains essential for manufacturers, especially in times of fast change. Thankfully, a wide range of digital tools have emerged for manufacturing companies that not only enable the rapid communication need right now, but that may very well put them in a better position from a decision-making perspective than they were in before all of this began.
The Rise of the "Smart" Manufacturer
Luckily, this new set of challenges that the industry is facing coincides with the rise of the Industrial Internet of Things (IIoT), a vast network of industrial devices and communication tools that put more actionable information at someone's fingertips than ever before.
The major benefit here is that these devices, many of which are located all over the shop floor, are not only constantly collecting data but they're also sharing it as well. This gives organizational leaders an almost unprecedented level of real-time visibility into what is going on in their organization at any given moment.
Globally, the IIoT in the manufacturing market size is projected to reach $45.3 billion by as soon as 2022. With these types of digital tools, manufacturing company leaders can get instant updates on everything from production schedules to resource allocation. They can see exactly what is happening on the shop floor at any given moment and if certain production quotas aren't being met, they'll finally be able to dive deeper and uncover the reason why. They'll be able to see which employees are performing as expected versus those who aren't, thus making better choices in terms of things like training and ongoing education.
Rapid Change Requires Better Communication
More and more organizations not only recognize the need for centralized monitoring and predictive maintenance tools, but the need to upgrade communication technologies as well.
It’s difficult for manufacturers to communicate best-practices effectively when you’re unable to walk someone step-by-step through a process at their desk or shop workstation to show them in person. Rapid communication is required in order to maintain operational efficiency while adapting to the shifting global market.
According to one recent survey, respondents said that the IIoT will not only help them better understand machine health, but it will also change the way plant maintenance personnel work and communicate with all levels of operation. This, coupled with the fact that this intelligence will help to better predict (and more importantly, avoid) plant shutdowns, creates a coalition that couldn't have come along at a better time.
(Dozuki users benefit from instant communication of procedures via a quick scan of a QR code)
Short Term Investments Generate Long Term Benefits
The opportunity of IIoT, coupled with other digital communication tools like ERPs and electronic work instructions, finally bring smart, data-driven communication and collaboration systems to manufacturing organizations during a time when all this is essential to continued success.
The amount of oversight now available is incredible, as a single consolidated system can now be used to collect customer contact details, to track supplies, to better understand the status of the shop floor and more. All of this can then be used to support and empower not only project planning, but also quality control as well.
These digital tools can also generate instant alerts when something goes wrong or when production conditions deviate outside the accepted norm. In other words, they won't just know that there is a problem - with the instant alerts generated from vast amounts of sensor data, they'll know exactly what happened and why. They'll be in an excellent position to not only address a small problem now before it has a chance to become a much bigger one, but they'll also be able to prevent it from happening again in the future.
A New Era of Communication
In the end, these new digital tools will enable people who need information access to perform their jobs better and safer — bringing a new era of communication and collaboration to any organization. By streamlining processes and better managing supplies, these digital tools (and the rapid communication they bring with them) will enable companies to offer greater quality products as a result. So not only do businesses get to enjoy an immediate boost in terms of communication and productivity, but they're also making a long-term investment in customer satisfaction and retention.
This of course brings with it the most critical advantage of all: a long-term boost of profitability.
That's not just how you create a genuine competitive advantage for yourself in the midsts of a global pandemic. It's also how you set yourself up for a new decade of success that will remain long after COVID-19 has finally passed us by.
Topic(s):
Industry News
Related Posts
View All Posts
Frontline Digital Transformation
Frontline of the Future: Part 1
8 min read
Historical Forces Impacting Manufacturing At Dozuki, we have our finger on the pulse of manufacturing trends. We believe it’s part of our mission to formulate clear...
Continue Reading
Training
Manufacturing Doesn’t Have A Hiring Problem, It Has A Retention Problem
10 min read
Consider two pieces of recent industry data: 75% of the workforce will be millennials by 2025. (Forbes) Thousands of experienced workers are retiring daily. The Silver Tsunami
Continue Reading
Frontline Digital Transformation
5 Ways to Get Wifi on the Factory Floor
6 min read
Here’s the reality, many industrial environments lack wireless internet. It’s not for a lack of trying. However, there are real, pragmatic reasons that some companies can’t...
Continue Reading