
Standard Work
6 min read
In Conversation with John Allwood
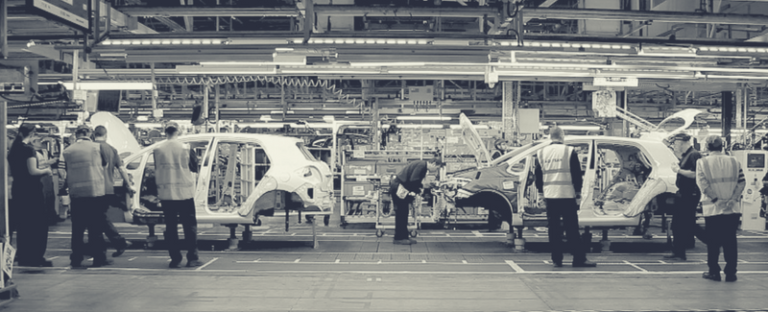
Standard Work is a concept that’s widely accepted among lean practitioners, yet doesn’t have a large body of text detailing its application. When used properly, Standard Work is an effective tool to reduce waste and solve problems within the value stream.
We were fortunate to sit down with John Allwood, lean expert and author of “Standard Work is a Verb,” to discuss his views on lean culture and process improvement, as well as how Standard Work can benefit from digital technologies.
How does the concept of Standard Work become a verb?
Standard Work becomes a verb when it is used and actively a part of the continuous improvement process. If Standard Work isn’t being used properly, the documentation becomes another form of waste.
The term ‘Standard Work’ pertains to what an operator is doing, on the plant floor (gemba), physically in the value stream. So if we’re talking about an operator that’s performing a task that’s repetitive and they’re doing it consistently—they’re doing Standard Work. They may not think of it that way, but it’s Standard Work being used as a verb, not a noun.
How can thinking of Standard Work as a noun create waste?
Standard Work only becomes a noun if we ignore it. When you talk about a document that represents Standard Work as the operator is doing it—it’s typically drafted by a manufacturing engineer, or someone not in the value stream. These kind of documents usually include a lot of technical jargon and other over-explanations that don’t actually represent what the operator is doing.
Because those documents aren’t actually reflecting the operator’s workflow, I don’t believe that operators are regularly checking them. These documents might get attended to a bit, but they end up in a folder. Those folders get dusty.
Now the Standard Work has become a noun, and is for all intensive purposes, useless. It’s become a burden rather than as asset. This means that we’ve used time and resources to create Standard Work that isn’t being engaged with; in other words, waste.
We wrote a recent post about your analogy for Standard Work as the GPS for processes, can you explain in your own words how Standard Work fits this analogy?
A GPS gives us a play-by-play for any sort of destination, but it also helps us find a destination if we are lost. Standard Work acts as a GPS because it can always answer the question, “Where do we go now?” Similarly, if an operator is unable to perform a task to a certain expectation, solving that problem can feel like being lost. You’re thinking, “Ok, I know there’s this problem, but where do we go now?"
Standard Work allows someone without any prior knowledge to observe the operator. From there they can explicitly identify the point of failure and where it differs from the Standard Work—which gives you an accurate starting point for your process improvement roadmap.
How do you think technology can help with these common obstacles?
Standard Work isn’t effective when it’s only in the hands of industrial engineers or people at their desks, far away from the gemba. When the idea of Standard Work was originally brought over by the Japanese, the holy grail was a paper document written by the operator. I think that the biggest way technology helps is by making the Standard Work more accessible and easier to use. Operators need to be able to easily access and interact with it at any time.
I’ve seen tools, whether or not they’re software, create barriers between the operators and the people implementing them. With technology, the aim should be something that is accessible and has a ease of use within the value stream, as opposed to something that creates distance. In that sense, technology has a tremendous opportunity to remove those barriers and provide more transparency.
On a day to day basis, how should operators be interacting with Standard Work?
Most operators aren’t going to be referring to the Standard Work after they perform multiple successful cycles. For operators, the Standard Work sticks best when it is integrated into three critical conditions:
- When learning how to complete a process.
- When being prevented from doing a process correctly.
- When revising the process.
Other than that, Standard Work can be fairly hands-off, you just need to make sure that it’s engaged with during those three crucial circumstances.
What one thing can readers immediately do to start improving their organization with Standard Work?
For a company that’s considering implementing any lean initiatives, take the time to fully understand what it means to create and sustain those programs. Also, realize that these programs will require company-wide buy in, from management all the way to operators.
Where can people find you if they want to learn more about your book and what you’re doing?
I share sample materials used in the book and additional free documents on my website, standardworkisaverb.com. I’m always free to talk to people or companies that are considering lean or Standard Work initiatives, I enjoy those conversations.
Are there any other resources that you would recommend for further reading on these topics?
Both The Toyota Way and The Spirit of Lean are great books to learn about the history and some of the foundational concepts of lean.
About John Allwood
John Allwood was first introduced to the Toyota production system while working at Tuthill Pump in Alsip, Illinois in the 1990’s. There, he met Bob Pentland, who was featured in the seminal book, “LEAN Thinking.” Currently, Allwood acts as a consultant, helping companies across the United State successfully implement Standard Work.
To learn more about John and his work, visit standardworkisaverb.com
Topic(s):
Standard Work
Related Posts
View All Posts
Continuous Improvement
Navigating Processes: Standard Work vs. Work Instructions
4 min read
The manufacturing industry is a professional arena with an overwhelming variety of industry terms and acronyms. We’ve tried to make a list of the most common Lean terms...
Continue Reading
Standard Work
What's Wrong with Standard Work?
8 min read
66% of companies fail in their attempts at Standard Work. This begs the question - what’s wrong with Standard Work? How can a seemingly simple methodology be so challenging...
Continue Reading
Standard Work
11 Benefits of Standard Work
5 min read
Taiichi Ohno, a founder of the Toyota Production System (TPS), had this to say about Standard Work, “without standards, there can be no Kaizen.” As the foundation for all...
Continue Reading