
Continuous Improvement
4 min read
Navigating Processes: Standard Work vs. Work Instructions
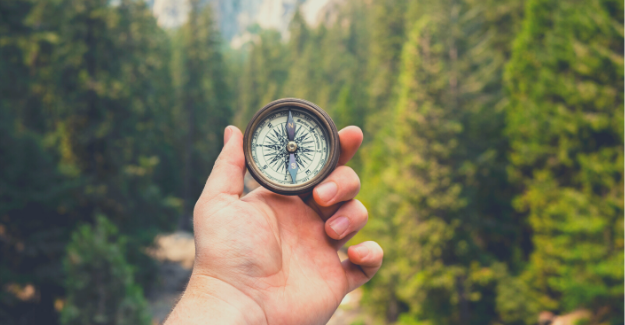
The manufacturing industry is a professional arena with an overwhelming variety of industry terms and acronyms. We’ve tried to make a list of the most common Lean terms before… we didn’t get very far.
Standard Work vs. Work Instructions
An unfortunate byproduct of all this jargon is that similar phrases can be used interchangeably, which muddles their meanings. This is mostly inconsequential, but the distinction between Standard Work and Work Instructions is worth clarifying.
Confusion surrounds these two thanks to a handful of very similar terms. Similar terms include: Standard Operating Procedures (SOPs), Quality Manuals, Procedures, Work Processes, Job Breakdown Sheets, Work Standards, etc… In the interest of time, this article focuses on the specific distinction between Standard Work and Work Instructions, because we believe these are the most crucial to continuous improvement.
Standard Work was first introduced in the Lean philosophies developed by Toyota and Taiichi Ohno. The notion of Standard Work contains many concepts, but at its core it is a way to observe processes, document procedures and identify value, then eliminate waste.
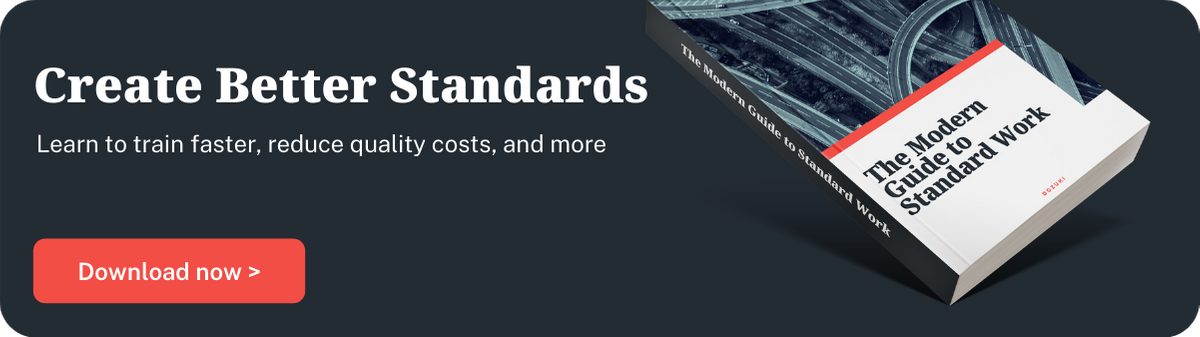
In his book, “Standard Work is Verb”, John Allwood describes Standard Work as the “GPS of the value-adding process.” In this analogy, Standard Work is the navigation system that helps direct you to the proper location; where value is being added.
Reduce Waste
If our starting point is a customer request, and the final destination is delivering value to the customer, Standard Work will give you the map to get there. A good GPS will also find the most efficient way to arrive at your destination.
In short, Standard Work is the least wasteful way to deliver value to the customer.
Work Instructions: Drivers Education
The GPS analogy also has limitations that help illustrate what Standard Work is not.
"A GPS system isn’t going to tell you how to drive, it assumes you’ve already been trained to do that."
“A GPS assumes certain skills,” Allwood states. In other words, GPS systems will give you a high-level overview of the route to your destination, but it’s not going to tell you how to drive. Google Maps isn’t going to tell you which pedal to press for the gas.
Unlike a GPS, which assumes certain abilities, Work Instructions assume little to nothing. They don’t just tell you how to do something, they include the technical information required for a process. With references to parts and materials, machine specs, and safety procedures, they go a few steps deeper than Standard Work.
Work Instructions will tell you which way to turn the ignition. They give you step-by-step procedures to maintain your vehicle, fill it up with gas, and operate it while driving. In this sense, Standard Work and Work Instructions are intimately related, but make no mistake: one is not a replacement for the other.
Standard Work 2.0
While Work Instructions are the meat of any procedure, Standard Work is the overarching process for evaluating and improving those processes. That’s why we built Dozuki.
With Dozuki, Standard Work becomes an integrated part of your operations. What was once an isolated process for improvement is now an integral component of your instructional practices. Improvements to work instructions can be approved and instantaneously released to employees.
Switching to work instructions with Dozuki has endless benefits, like supercharging the digital transformation of your organization, but the major payout comes from implementing Standard Work as a daily practice.
Related Posts
View All Posts
Continuous Improvement
What is Standard Work?
6 min read
Lean operations and manufacturers have used Standard Work for decades, yet many companies lack clarity when it comes to this fundamental lean methodology. How is Standard...
Continue Reading
Standard Work
In Conversation with John Allwood
6 min read
Standard Work is a concept that’s widely accepted among lean practitioners, yet doesn’t have a large body of text detailing its application. When used properly, Standard...
Continue Reading
Standard Work
Free Standard Operating Procedure & Work Instruction Templates
4 min read
Standard operating procedure (SOP) and work instruction templates help standardize processes and present information consistently. We’ve seen thousands of examples of these...
Continue Reading