
Work Instructions
4 min read
Key Differences Between ISO 9001:2015 and 2008
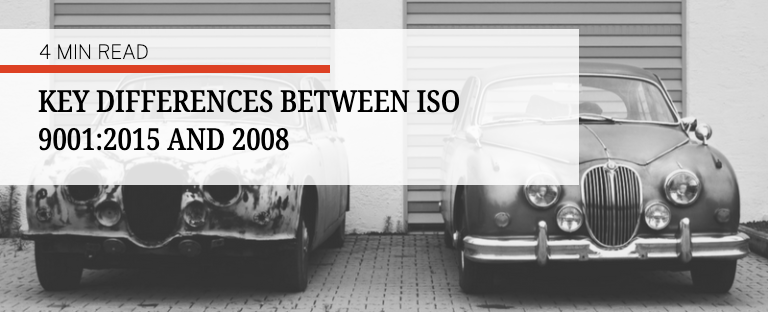
ISO 9001 is the world’s most commonly used standard for quality management systems (QMS).
About every 7 years, ISO updates their standard to reflect the changes in global business operations and new technologies. Two key priorities for this round of the ISO 9001:2015 update are: (1) increasingly global operation and supply chains; and (2) increased expectations from customers.
It’s All About Risk
ISO also places a strong emphasis on a new methodology for mitigating mistakes via “risk-based thinking”. Which, in correlation to the 2008 standards, is a direct replacement for the “preventive action/corrective action” strategies outlined in the past. In short, this new approach takes preventative action to a new level by getting ahead of process improvement strategies with preemptive risk analysis.
Goodbye Documentation Requirements
A significant byproduct of risked-based thinking is the elimination of certain documentation mandates. Rather than prescribing which documentation companies should include, the risked-based approach allows companies to assess key areas of risk, identify areas to mitigate said risk, and then develop implementation plans around those.
Hello Standard Work
They key distinction here is that documentation should only be required based on individual risk assessments. This helps companies avoid redundant or unnecessary documentation, instead allowing them to focus on documenting preventative processes. ISO found that when documentation is created just to check a box, it will remain stagnant and unused.
Documentation assumes a much more dynamic role in the new standards. Rather than responding and updating documents to retroactively reflect changes, documented processes in the 9001:2015 standard will be used as a part of the the continual improvement framework. Much like the Standard Work lifecycle, where documenting processes are an integral part of the process improvement strategy.
Getting Knowledge Out of the “Tribe”
This brings us to the next key component in the new ISO 9001:2015 standards — organization knowledge. Organization or “tribal” knowledge is the notion that knowledge of processes exists within only a few individuals, rather than shared across the company.
Clause 7.1.6 of the standards dictate that companies acquire and standardize this knowledge to avoid problems due to staff turnover or improper sharing of information.
Making Information Easier to Find
A crucial aspect of the new ISO 9001:2015 organizational knowledge element is the accessibility of documentation. That means that employees on the shop floor, in accounting, or in a manager’s office will have access to the appropriate knowledge whenever they require it. This is especially relevant to the new focus on globalization. Not only should documents be accessible, but they may also need to be shared and understood across multiple countries.
Of course, when we’re talking about accessibility, we must also focus on control. While it’s beneficial to spread organizational knowledge far and wide, limitations should be placed on documentation to control who has access to edit and ensuring that the most recent versions are in use.
Bringing ISO 9001 Into the 21st Century
While this isn’t the first ISO 9001 to be published in the 21st century, it is the first iteration of the standard specifically designed to confront technological advancements and increased globalization.
We can see that having a robust quality management system and Standard Work solution are critical for the new risk-based thinking approach. Additionally, digital tools like Dozuki are recognized as an integral part of business operations, reflecting the benefits that technology has brought to the global workforce.
Topic(s):
Work Instructions
Related Posts
View All Posts
Work Instructions
How to Get ISO 9001 Certified with Dozuki
6 min read
As the most commonly used standard for quality management systems (QMS), the ISO 9001:2015 standard implements a preventative, risk-based approach that puts documentation at...
Continue Reading
Training
What to Look for in QMS Software
5 min read
Traditional quality management system (QMS) software does exactly what it’s supposed to do. Like file cabinets for the digital world, they organize and control your company...
Continue Reading
Training
ISO 9001 Certification is Easier Than You Think
51 min read
Is audit anxiety holding your company back from ISO 9001 compliance? While it may seem like a daunting task, many businesses are closer to certification (and...
Continue Reading