
Standard Work
20 min read
Push vs. Pull System in Manufacturing: A Complete Overview for Optimizing Production
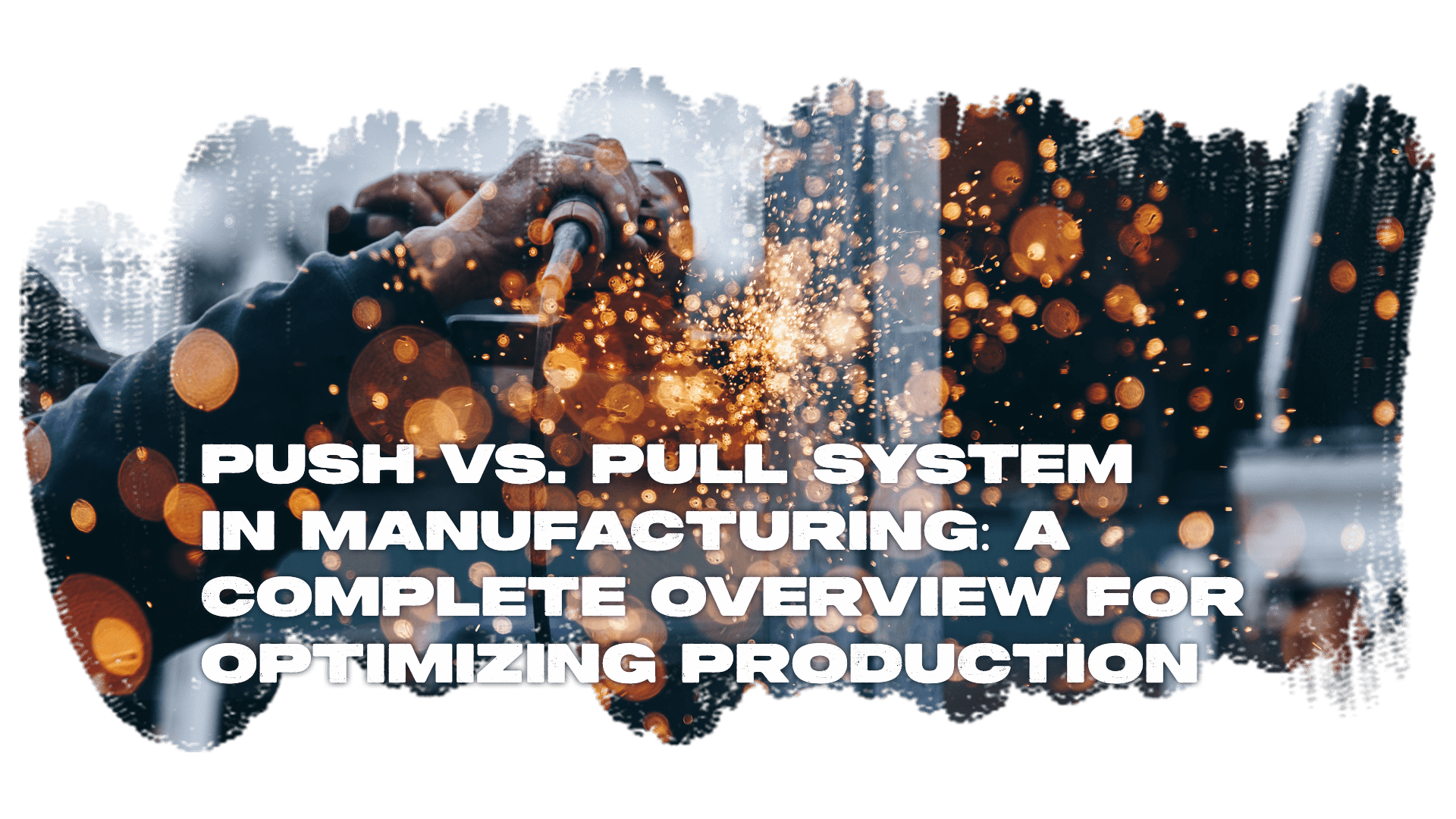
Manufacturing companies must carefully balance expenditure and revenue to remain profitable. It might sound simple when put that way, but every manufacturer knows that the dance is an intricate one. Throw in the goal of lean manufacturing, and it becomes even more so.
Table of Contents
1. Key Principles of Push & Pull Systems
4. Comparison & Contrast: Push vs. Pull
5. Demand Forecasting & Planning: Push vs. Pull
6. How to Choose Between Push vs. Pull
The Covid-19 pandemic threw the manufacturing industry into a sort of tailspin in more ways than one. Suddenly, materials were in short supply or delayed by shutdowns and transportation snags.
Customers were left wanting products that were not available. And many manufacturing companies reacted by stockpiling inventory, spurred by a sudden panic state.
Rather than be left without products to sell, they overproduced and stockpiled inventory to guard against losses.
Now that the pandemic pandemonium has diminished somewhat, manufacturers are reevaluating their production models and debating the benefits and costs of a push versus a pull system.
A push system relies on market demand and forecasting to dictate production levels. A pull system, however, uses current customer demand to dictate what to produce and when.
Push systems are standard in industries that produce a wider variety of products and longer lead times. Pull systems are usually seen in industries with shorter lead times.
A pull system is a staple of a lean manufacturing model because it leads to lower inventory levels, less waste, and much faster response times to real-time customer demand.
This article will explore the fundamental differences between a push vs. pull system in manufacturing.
We will weigh the pros and cons of each and demonstrate how organizations can make the best choice for their customers.
Key Principles of Push & Pull Systems
Understanding how to choose between a push system vs. a pull system requires understanding some fundamental principles.
The difference between push and pull systems relates to when production occurs.
The product is pushed out in a push system based on projected demand. These projections might come from predictions based on market demand, historical sales data, or some other source. But the key is that production occurs because of a predicted need.
A pull system, however, is based on the just-in-time manufacturing model. It’s a lean manufacturing technique that seeks to cut waste by only pulling in materials and producing goods when there is an already-specified need.
The customer places an order, and that order is produced as needed.
In a pull system, work is only started at the moment it is needed. The ability to reduce waste and eliminate producing, managing, and storing inventory that is not yet (and may never be) needed is a massive benefit for manufacturers.
The pull system differs from the push system because of this reason and because the push system puts no limits on the amount of in-process work that can be in the system at any one moment.
Some manufacturers benefit from this structure, but many find that keeping production lines open when there is an actual need is a positive.
Principles of a Push System
- Sets production based on market and consumer demand projections
- Based on anticipated need
- Reduces the risk of product shortages
- Potential for wasted or overstocked inventory and materials
- Good for longer lead times
Principles of a Pull System
- Based on a Just-in-Time manufacturing model
- Production only occurs when there is an actual customer order
- Materials and supplies are ordered only when needed
- Lower risk of waste and overstock situations
- Higher risk of inventory shortages when demand fluctuates
- Good for shorter lead times
Push System Overview
A push system is more optimized for manufacturers who carry a large variety of products and have a need to meet a varied demand in the market.
Manufacturers never have to worry about running out of products or shuffling production schedules to meet fluctuating demand.
But manufacturers who use a push system risk producing more than is needed, raising production and inventory storage costs, and adding to the amount of waste.
The Pros of Push System
- Increased Flexibility
A push system uses predictions to create production schedules. When market demand is expected to rise, production ramps up to meet it.
This allows for more flexibility for all members of the supply chain and the production team itself. Push systems benefit manufacturers who deal with longer lead times.
- More Time for Planning and Problem-Solving
This flexibility means plenty of time for purchasing and replenishing raw materials. It allows for the time required for planning and organizing shipping and storage solutions.
And it means that supplier delays can be more easily mitigated – a benefit that has become increasingly important and apparent because of the upheaval of the pandemic.
- Faster Fulfillment
A push system provides a faster and easier way for manufacturers to get products to customers.
With a steady and reliable stock of inventory on hand, fluctuating market demand is not a roadblock to fulfilling orders. The product can be shipped without delay as soon as an order is received.
The Cons of Push System
- Risk of Inventory Overstock
Post-pandemic, many manufacturers are feeling the adverse effects of a push system. This includes sitting on piles of overstocked inventory that may no longer be in demand.
This is especially difficult for manufacturers who deal in perishable items or produce goods that tend to go out of demand very quickly.
- Difficulty Predicting Demand
Predicting market demand is often tricky, and getting it right 100% of the time is unlikely. Consumers are fickle, as is the market itself. Economic situations can quickly turn an expected demand into a costly overstock situation.
- Higher Costs and Investment
No organization wants to pay storage costs for inventory that is not selling. Not to mention that predicting market demand already represents an up-front cost. Businesses with limited resources may not have the operational funds to invest in these activities.
Pull System Overview
Pull systems are known for being much more efficient than push systems. That’s because manufacturers using a pull system don’t risk overburdening themselves with unnecessary materials or inventory.
What is produced is exactly what is needed at that very moment.
The Pros of Pull System
- Increased Efficiency
The Just-in-Time production model is designed to create the most efficient system possible. By only pulling in materials when needed and waiting to begin production until there is an actual need, organizations put their resources toward the most effective and efficient outcomes.
- Reduced Inventory Levels and Lower Costs
Without worrying about what to do with unnecessary inventory, organizations can save a substantial amount of money in the form of lower storage costs. Pull systems also lend themselves to reduced waste, improved efficiency, and in turn, greater productivity where it matters the most.
- Improved Quality
The basis for the pull system stems from the lean manufacturing ideal, which means producing more with less.
A higher focus on reducing waste means a more remarkable ability to make goods without defects. Fewer defects are a surefire way to end up with a higher quality product.
The Cons of Pull System
- Risk of Stockouts
Producing products only when an order comes in is a great way to reduce waste. But what happens when market demand takes that unexpected uptick and too many orders start flowing in?
Simple – stockouts happen. Without accurate demand forecasting, businesses using a pull system might be left unable to fill orders, which means fewer sales and unhappy customers.
- Increased Complexity
Producing goods precisely at the moment they’re needed puts manufacturers in a precarious position.
Getting it right requires excellent communication with suppliers and accurate demand forecasting. One slight disconnect in the supply chain can send the system tumbling.
Therefore, the risks of a pull system lean more toward poor production planning. Without careful planning, excellent organization, and superb supplier relationships, manufacturers relying on a JIT model might be out of time.
Comparison & Contrast: Push vs. Pull
Manufacturers debating between a push vs. pull system need to weigh the benefits of each. A driving factor in this decision is inventory. No manufacturer wants to waste money making products that don’t sell.
One study from supplier Avery Dennison found that manufacturers globally waste around $63 billion worth of inventory every year, or around 8% of surplus stock. All that wasted inventory equates to wasted time, energy, and money.
Another struggle brought on in part because of the pandemic is the challenge of finding warehouse space for all that excess inventory.
With manufacturers stockpiling goods to stave off product shortages during and after the pandemic, warehousing space is limited, and warehousing vacancies have become few and far between.
Anticipated Demand Vs. Actual Demand
Making the right decision in the matter often comes down to the types of products an organization sells and how they sell them.
A push system produced goods in anticipation of demand. This system can be a great fit for organizations that require longer lead times.
The anticipatory nature of market demand forecasting means a greater ability to prepare for scenarios, and more flexibility from a time-management perspective.
However, a pull system is often a better choice for manufacturers who must work with shorter lead times. Because a pull system relies on actual demand, as it happens in real-time, there is less time to prepare.
Materials must be procured quickly, and products must come off the line ready to ship as soon as possible. Customers who place an order won’t wait for that order to be filled simply because the manufacturer wasn’t prepared to go at the right time.
Demand Forecasting & Planning: Push vs. Pull
We’ve mentioned demand forecasting several times in our effort to explain the difference between push vs. pull. And for most manufacturers, demand forecasting and planning topics are not new.
Forecasting plays a vital role in strategic business planning. It plays a part in production planning and structuring the supply chain. Without accurate forecasting, manufacturers will struggle to balance supply and demand, regardless of whether they use a push or pull system.
Here’s why:
Demand Forecasting in a Push vs. Pull System
Push systems rely on demand predictions. The ability to predict consumer demand helps organizations see into the future and know what to expect.
In a push system, these predictions function as triggers for essential processes. Raw material planning and procurement, supply chain operations, logistics, and more all rely on market predictions in a push system.
A pull system relies on customer demand instead of predictions to trigger production. But that does not mean that organizations that use a pull system can get by without some form of demand forecasting.
Being able to meet production demand with careful planning and strategic actions at the right moment is crucial for a pull system.
Using demand forecasting effectively in both systems requires communication and coordination. The significant difference between the two models is when production begins – and what triggers that action.
In a push system, that trigger is predicted market demand. In a pull system, it’s the customer demanding a product.
Both systems require careful planning and execution – a push system to mitigate the risks of creating an inventory overstock situation and a pull system to avoid stockouts caused by bad planning and communication.
How to Choose Between Push vs. Pull
The goal of restructuring production models and supply chains is front of mind for many manufacturers. One recent study shows that 42.2% of organizations plan to do that in 2023, while another 46.7% say it’s a future priority.
The decision between push vs. pull systems is a consideration in this restructuring process.
Understanding how each system works for the manufacturer's benefit is half of the equation. The other half is dependent on the manufacturer itself. Every organization will have unique needs, as will its customers. Matching the production system to the organization's needs is the key to success.
Push systems rely on predictions of future customer demand to determine when to order materials or produce stock.
Pull systems only begin production when a customer requests it but require careful planning and great supplier and shipping relationships to get that product to the customer quickly. Here are a few factors to consider when making the choice:
- Type of Products
- Variety of Products
- Reliability of the Supply Chain
- Size of the Customer Base
- Operating Budget
- Organizational Goals
Making the Right Choice
Like most business decisions, the choice between a push and pull system is unique to the organization and its needs. Push systems are the more common choice because many manufacturers find safety from the dreaded stockout there.
However, push systems often result in higher costs and higher waste, especially if the accuracy of demand forecasting is subpar.
Pull systems are becoming more popular in manufacturing, especially as organizations face pressure to become more sustainable and reduce their environmental impact.
However, companies that rely on a pull system face a tough road if they don’t have the proper planning and procedures in place beforehand.
Making the correct choice comes down to answering a few key questions. Manufacturers need to consider the specific needs of the business, such as the type of products sold, the size of the customer base, and the available budget, before deciding.
Final Thoughts
Understanding the difference between a push vs. pull system in manufacturing is about understanding demand – and how to meet it.
Each system has drawbacks and benefits, and choosing the right structure for a business is crucial if the organization wants to remain competitive.
A push system is an excellent choice for organizations with the working capital to invest in things like demand forecasting and inventory storage. It comes with a higher price tag, often in the form of waste, but it can make it easier to navigate a fluctuating market.
However, wasting money on unused and unsold inventory can be a death blow for some organizations.
Especially when that organization does a large volume or deals in products that don’t necessarily maintain profitability (think food production, pharmaceuticals, or tech products).
On the other hand, a pull system is known for being much more efficient – but harder to pull off successfully. A pull system can result in unmet demand and unsatisfied customers without solid supplier relationships and a reliable supply chain.
How does a manufacturer decide? By carefully weighing the pros and cons of each and matching it with the needs and capabilities of the organization.
The goal, as always, is to produce goods at the lowest cost possible while maintaining quality and meeting customer demand. The right system, push or pull, is the one that provides the best outcome for an organization with these goals in mind.
Topic(s):
Standard Work
Related Posts
View All Posts
Continuous Improvement
Streamlining Production: How Lean Manufacturing Can Revolutionize Your Business
23 min read
Manufacturing is a delicate process. So many moving parts must come together just right if the aim is to produce goods of the highest quality in the most cost-effective way...
Continue Reading
Standard Work
Best Practices to Maximize Production Capacity in Manufacturing | 2023
24 min read
According to the numbers, manufacturing makes up around 12% of the U.S. GDP and provides jobs for 12.984 million Americans, or about 9.6% of all U.S. workers. In other words,...
Continue ReadingThe Most Common 8 Wastes of Lean Manufacturing & How to Manage Resources
23 min read
Manufacturing is all about making the highest quality products at the lowest cost. Reaching that goal means searching for and eliminating causes of wasted time, wasted...
Continue Reading