
Training
5 min read
What to Look for in QMS Software
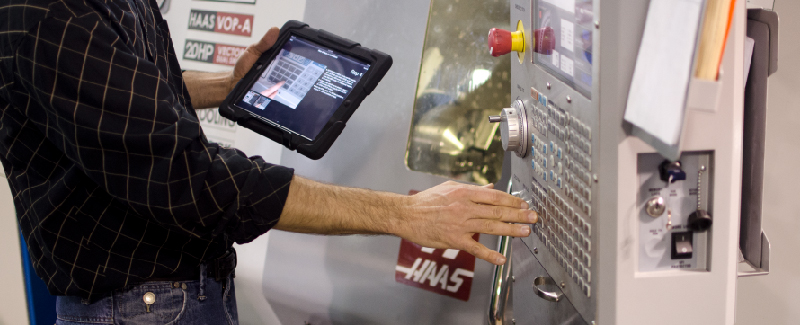
Traditional quality management system (QMS) software does exactly what it’s supposed to do. Like file cabinets for the digital world, they organize and control your company standards.
But for the same reasons that file cabinets don’t increase process efficiency or reduce waste, their digital counterparts can be equally as ineffective.
Quality Means Always Improving
QMS software performs the important job of centralizing information, managing access, and leaving a record of revision history. This works well for audit trails and record keeping, but falls short when it comes to continuous improvement.
A conventional QMS software stores processes like museum artifacts - safely, securely, and with a detailed record of history. This blanket approach may work well for some file types, but any documented process is a unique type of documentation — Standard Work. In order to continuously improve processes we can’t treat them processes like artifacts. Standard Work requires us to engage with and improve documents on a consistent basis.
4 QMS Features That Improve Processes
1. Intuitive Usability
Tools shouldn’t create friction, barriers, or require intense learning curves—especially for people who regularly engage with documentation. Accessing and understanding documented material should be easy for any employee.
Key Insight:
If an untrained employee was asked to access and start a safety procedure, could they intuit how to find the correct information, or would it require oversight? Making process information accessible and easy to use is a top priority to ensure that Standard Work will receive the engagement that it requires.
2. Streamlined Feedback Loops
Giving your employees the ability to provide feedback or suggestions is the first step in creating a lean culture. Without this, the continuous improvement lifecycle can’t begin. Collecting insights from the location where work takes place (gemba) provides you with the most valuable feedback.
Key Insight:
How do employees provide feedback at your organization? Suggestions should be collected and controlled in the environments where the Standard Work is occurring.
3. Integrated Content Creation
Most QMS tools allow you to manage documents, but when it come to the creation of processes, companies have to rely on other methods. This requires unnecessary changeover and doesn’t leverage the quality control capabilities that a QMS is intended to provide.
Key Insight:
QMS software should always allow for content creation within the platform. This allows organizations to create and update processes from directly within the QMS, rather than being forced to import from an outside system.
4. Precise Revision Control
Most auditors are looking to ensure that organizations have an effective system in place for document control. Their primary motivation is to prove there is a regulated way of protecting and recording changes. Without integrated content creation, most QMS software can only control the uploading or removal of documents, not the revisions themselves.
Key Insight:
Controlling what gets changed and for what reasons is critical for quality control, ISO 9001:2015 certification, and continuous improvement. Your QMS tool should allow users to know why a process was updated and how the changes were implemented.
QMS Software for Continuous Improvement and Standard Work
Our mission is to make Standard Work an industry standard. We approach this by integrating Standard Work and continuous improvement into our software; giving you all the tools to manage your documents and implement an effective QMS tool.
Submit Rework Forms with Operator View
This allows your teams to capture quality data, photos, and notify managers for signatures.

Integrated Content Creation
Allow privileged users to create and edit documentation in a user-friendly interface, with custom document controls to require approval of new versions or changes.

Digital Feedback Channels
Employees have the ability to provide specific feedback while using the Standard Work, and notify key personnel of their insights.
Detailed Revision History
Keep records of all edit histories, making audits and version tracking a breeze.
Ease of Access
Provide intuitive access to key processes for users across your organization. Restrict access to documentation based on user role or team.

Related Posts
View All Posts
Training
A New Model For Manufacturing Hiring
14 min read
Constraint, Currency & Clarity What invention had the most profound impact on manufacturing hiring? Not the steam engine. Not the assembly line. Not lean practices. Not...
Continue Reading
Standard Work
Free Standard Operating Procedure & Work Instruction Templates
4 min read
Standard operating procedure (SOP) and work instruction templates help standardize processes and present information consistently. We’ve seen thousands of examples of these...
Continue Reading
Training
Using Digital Tools as a Recruitment Tool in Manufacturing
7 min read
Manufacturers are being squeezed in both directions these days. Demand for products is outpacing their ability to secure raw materials for production, and they don’t have...
Continue Reading