
Work Instructions
6 min read
4 Signs Your Work Instructions Need an Upgrade
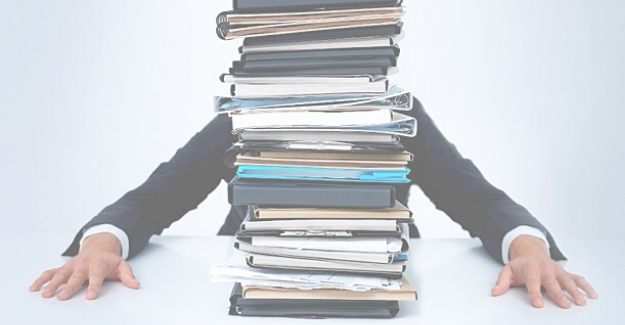
Knowing when to make the transition to a better documentation tool is a tough question to answer. The short answer is that there is no short answer. In Industry 4.0, a strategic approach to any digital transformation project will need to consider:
- Strategic Business Goals
- Resource Availability
- Customer Needs
Fortunately, there are 4 key signs that can be used to evaluate the state of your work instructions and indicate whether or not an upgrade is necessary.
Not Broken ≠ Good Enough
Manufacturers know that electronic work instructions are a necessary upgrade for continuous improvement and standard work. However, because documentation is so fundamental to most business processes, the idea of changing a system that underlies many core business practices can be intimidating and foster hesitation.
Furthermore, the manufacturing industry has historically been hesitant to adopt emerging technologies in general. This creates a lack of urgency from company leaders. After studying over 400 firms over a period of two years, MIT Sloan found that only 25% of industry executives believed that they would be impacted by digital transformation.
Many companies have a system (intentional or not) for documenting important information and processes but are unaware of how outdated their practices are. This creates the dangerous assumption that for manufacturing work instructions, “not broken,” is good enough.
A Different Reality
Imagine walking into a workplace and asking the staff if they have instructions for the work they are currently doing, their answer may sound something like this:
"Of course we have work instructions! They’re probably in the binder in that cabinet over there, or our engineer might have the files on his computer."
Then they search for quite some time and finally retrieve the document. You ask, “Is this an accurate description of your work?” A likely response:
"Yes, kind of... but with increased demand, we don’t have time to clean that part thoroughly anymore and we no longer use this machine setting. Oh, and I heard that this quality check is not that important."
In reality, the comparison between what is written and how work is actually done can vary quite a bit. Most companies wouldn’t be able to claim that employees always follow established standards.
4 Signs Your Work Instructions Need an Upgrade
Ultimately, deciding when to make the switch will be highly dependent on available resources, leadership support, and the type of system you’re currently using (paper-based or digital). Knowing that many companies are facing similar challenges will provide confidence when taking the step forward with a digital upgrade.
1. Nobody Uses the Documents
Probably the most common indicator that your work instructions are ineffective — nobody is using them. Many times, technical writers, engineers, or training specialists, go through the effort of creating and documenting standardized procedures, but the documents end up collecting dust because they are:
- Inaccurate
- Outdated
- Or difficult to access
2. Documents Are Difficult to Access
Finding the correct document may seem like a simple task, but if you’re like most companies, your organization has accumulated thousands upon thousands of files over the years. Large binders of dense, and likely outdated materials. Even if documents are digitized, when using multiple systems to create, manage, and store work instructions, finding the correct documents can be just as difficult their paper-based counterparts.
If you are struggling to find the right work instructions relevant to your job, then it might be time to upgrade to a system that is more streamlined in its approach to document management and accessibility.
3. Documents Are Always Outdated
Have you ever searched for SOPs or work instructions, only to discover that upon finding the document, it’s over 10 years old and probably not accurate anymore? A recent survey discovered 78% of manufacturers are using documents that are outdated or ineffective, causing a lack of standardization and quality control.
When documents don’t reflect the reality of the work, employees will resort to grandfathered knowledge and best guesses, rather than the approved standards. If your documents constantly feel like they’re outdated, this is a substantial indicator that your system for work instructions needs a faster method for revising and improving documentation.
78% of manufacturers are using documents that are
outdated or ineffective, causing a lack of standardization and quality control.
4. Updating Procedures is Cumbersome
Documentation should be a celebrated aspect of continuous improvement. However, many employees actively avoid documenting procedures because their system for creating work instructions is too tedious or difficult to work with. Documenting standards creates a baseline for continuous improvement, so when employees are discouraged from writing things down, continuous improvement will be negatively affected as a result.
When you document and standardize a process, by nature, it immediately starts becoming outdated. Operators naturally find better ways of performing tasks, new methods are introduced, parts and tools change, etc. If the process for updating procedures is bureaucratic and cumbersome, documents will quickly become outdated and ineffective.
Avoid False Confidence
While organizations may believe that their documentation practices are effective and even streamlined, the statistics would present a different reality.
In a recent survey that assessed the success rate at implementing different lean tools, standardized work and work instructions were the least successfully implemented lean methodologies of all.
66% of Lean organizations are failing at implementing standardized work.
This indicates that companies understand the value of good documentation practices such as standardized work, but are largely unsuccessful in sustaining those efforts. This false confidence can cause companies to ignore the signs of poor documentation practices until it’s too late.
Related Posts
View All Posts
Work Instructions
Electronic Work Instructions in Industry 4.0
5 min read
How do electronic work instructions factor into Industry 4.0 and your digital transformation strategy? With advancements in technology, it’s time to reevaluate how these...
Continue Reading
Standard Work
What's Wrong with Standard Work?
8 min read
66% of companies fail in their attempts at Standard Work. This begs the question - what’s wrong with Standard Work? How can a seemingly simple methodology be so challenging...
Continue Reading
Work Instructions
How to Get More Out of Your Work Instructions
6 min read
When leveraged properly, standardized work instructions can transform operational efficiency, quality management, employee performance, and more. All industrial businesses...
Continue Reading