The industrial engineering team at Husqvarna North America is responsible for drafting, updating, and distributing work instructions for final assembly of the hundreds of Husqvarna products handled in the Orangeburg, South Carolina facility.
A cumbersome mix of tools required the time of multiple departments in order to meet approvals and security guidelines. This combination of software solutions included QSI, Lotus Notes, Excel, and PDFs—all of which prevented streamlined approval processes and created issues with old versions still being used on the floor due to slow database updates.
As their team began researching how to improve the process and reduce waste, Dozuki stood out as a means of authoring and distributing work instructions for approvals and implementation.
Improving a “Cumbersome” Process for Managing Work Instructions
Brad Matthews, an Industrial Engineer for Husqvarna, described the process of creating and distributing approved work instructions as “cumbersome.” The convoluted process had severe limitations that prevented updates from being effectively pushed out due to a combinations of non web-based software tools.
With this inefficient system, considerable communication improvements were prevented from being implemented. “We used Excel to create our work instructions and had to make sure our formatting was perfect. Then we’d convert to PDFs to send to another department, who would then import them into a QSI database and pull into Lotus Notes.” Matthews takes a breath before he continues, “from there instructions ran through the approvals process. When any change needed to be made it had to go through that entire workflow. […] We would lose all the associated data when our original Excel instructions were converted to PDFs, so it wasn’t even searchable.”
He knew there was a lot of room to make the process move faster and make work instructions more effective. With the green light to find a new solution, Matthews began his search.
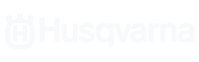
“
Updating work instructions with a phone on the fly has been really helpful. Before it would have taken an entire day to update an instruction, now we can do it on the fly from the floor.”
– Brad Matthews
Industrial Engineer, Husqvarna
Streamlined Work Instruction Management
When numerous software tools are linked together, creation and process improvements can quickly slow down version distribution, leaving outdated information on production lines. Says Matthews of the issue, “We were having problems with old versions being on the floor or newer versions being on the floor that weren’t visible to operators yet due to the system not updating fast enough.” Since implementing Dozuki, freshly approved versions are immediately sent to workstations on production lines—a process that previously took a couple days.
Now, line operators are always working from current versions, and incremental changes can be created on the fly using the Dozuki mobile app. This allows multiple team members to review critical work instructions on the line, providing an in context (kaizen) audit to accurately update instructions. Matthews recalls a specific instance, “I was able to implement the comments of all four auditors, take and upload new photos into the work instruction, and show them the updated version immediately—all from my phone. They were impressed that it got updated so quickly.”
Managing Implementation Quickly with Dozuki Services
Once Matthews and his team made the decision to move forward with Dozuki, the project of bringing existing and archived work instructions into the system fell on their shoulders—all while continuing to build and update the existing library of instructions. With a team of five this would be a nearly insurmountable task.
Rather than straining internal resources or jumping through hoops to hire an intern, the Husqvarna team turned to Dozuki’s conversion services to complete the migration. By leveraging the expertise of the Dozuki documentation team, existing instructions were able to quickly be created in Dozuki while Matthews and his team built new instructions in the system.
“There is no way we would have been able to get up and running with Dozuki as fast as we did without the conversion team, we just don’t have the resources to do it.” Matthews recalls it being both an easy decision for him and the management team, “it was a good price too, we just couldn’t pass it up.” Ultimately, this decision led to a much faster project implementation and significant staff time savings.