Partnering With The Best
More than 580 companies in 38 countries have partnered with us on their frontline digital transformation journey. Join us.
Driving Heavy Equipment Manufacturing Operations
With manufacturers facing the compounding challenge of recruitment, retention rates, and retirements, it’s never been more important to look toward digital solutions to address these issues. Industry leaders are partnering with Dozuki to overcome their obstacles by capturing internal expertise, improving standardization and training, and increasing worker retention.



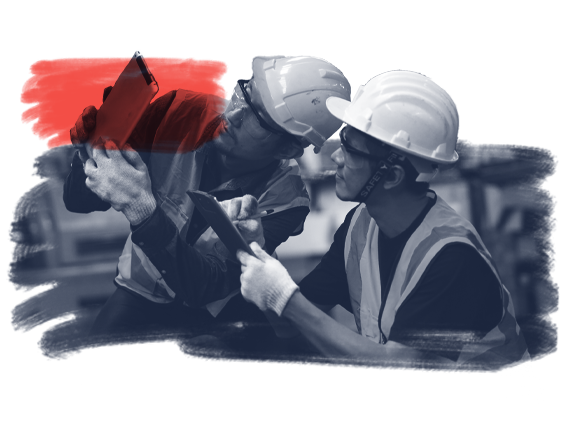
Optimize Performance
Empower your frontline workers to train better, share expert knowledge, and execute their best work.
-
Maintain Frontline Safety
Shore up safety when operators train to actual frontline procedures
Heavy equipment manufacturing has never been more complex than it is today. From the massive components hoisted through assembly to the extreme temperatures of the forge, there is no room for operator error.
Ensure that even your newest operators are performing to exacting guidelines on the floor. Dozuki manages ongoing training of frontline workers on the procedures they are performing day to day, tracks competency, and automatically retrains them on your terms. Systematically address knowledge gaps and empower better operators. -
Improve Continuously
Improve operations with the knowledge of your frontline
From your long established experts, to the new-hires with fresh eyes, significant untapped knowledge is available for improving and optimizing operations. Ideas for process improvement are too often undocumented, reticent to be shared, or lost when your information gatekeepers retire.
Dozuki incentivises your frontline to share knowledge and provide feedback on procedures – demonstrating their expertise, increasing sense of ownership, and helping you improve standards along the way. Process feedback can be put through review and approval workflows, where operations stakeholders can integrate it into updated standards. -
Standardize Training
Turn your standards into frontline training curriculum
Inefficient practices like job-shadowing and on-the-job training continue to be common training methods in heavy machinery. Both require an experienced mentor to be available for peer-to-peer coaching and in the end, the quality of training can be highly variable. Without a standardized system to manage training and knowledge transfer, best practices are left up to the experience, training technique and frankly, mood of each employee.
Turn the training instruction from your experts into standardized digital instructions in Dozuki, with video, images, and callouts. As the knowledge of your experts becomes your working standard – you can turn that information into your training curriculum. Standardize your training and scale it across your organization in one fell swoop. -
Capture Expertise
Extract the knowledge of your frontline experts
With a mix of legacy equipment that’s been around for decades, and an influx of advanced technology making its way onto the frontline, expert knowledge has never been more in demand. When workers leave or retire, critical operations knowledge is walking out the door with them.
Dozuki provides a purpose-built system for capturing the knowledge of your experts in an incredibly easy fashion. Expert knowledge can be rapidly turned into digital working standards that can be scaled across shifts, departments and facilities.
Shore up safety when operators train to actual frontline procedures
Heavy equipment manufacturing has never been more complex than it is today. From the massive components hoisted through assembly to the extreme temperatures of the forge, there is no room for operator error.
Ensure that even your newest operators are performing to exacting guidelines on the floor. Dozuki manages ongoing training of frontline workers on the procedures they are performing day to day, tracks competency, and automatically retrains them on your terms. Systematically address knowledge gaps and empower better operators.
Improve operations with the knowledge of your frontline
From your long established experts, to the new-hires with fresh eyes, significant untapped knowledge is available for improving and optimizing operations. Ideas for process improvement are too often undocumented, reticent to be shared, or lost when your information gatekeepers retire.
Dozuki incentivises your frontline to share knowledge and provide feedback on procedures – demonstrating their expertise, increasing sense of ownership, and helping you improve standards along the way. Process feedback can be put through review and approval workflows, where operations stakeholders can integrate it into updated standards.
Turn your standards into frontline training curriculum
Inefficient practices like job-shadowing and on-the-job training continue to be common training methods in heavy machinery. Both require an experienced mentor to be available for peer-to-peer coaching and in the end, the quality of training can be highly variable. Without a standardized system to manage training and knowledge transfer, best practices are left up to the experience, training technique and frankly, mood of each employee.
Turn the training instruction from your experts into standardized digital instructions in Dozuki, with video, images, and callouts. As the knowledge of your experts becomes your working standard – you can turn that information into your training curriculum. Standardize your training and scale it across your organization in one fell swoop.
Extract the knowledge of your frontline experts
With a mix of legacy equipment that’s been around for decades, and an influx of advanced technology making its way onto the frontline, expert knowledge has never been more in demand. When workers leave or retire, critical operations knowledge is walking out the door with them.
Dozuki provides a purpose-built system for capturing the knowledge of your experts in an incredibly easy fashion. Expert knowledge can be rapidly turned into digital working standards that can be scaled across shifts, departments and facilities.
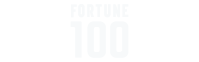
“
Dozuki gives technicians the information they need, where they need it.”
– Manufacturing Engineer
Fortune 100 Equipment Manufacturer
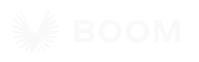
“
After comparing Dozuki to other options, it became a clear choice. The system is so intuitive and easy to kick-off... just like navigating a website.”
– Lead Manufacturing Engineer
Boom Supersonic
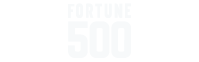
“
Our usual changeover took 4 hours, but the first time running it with Dozuki we did it in just 90 minutes. Plus we ran at 127% commit after the changeover, which usually runs at about 60%.”
– Training Coordinator
Fortune 500 Food Processing Company
See the Dozuki Difference
We help you capture and standardize knowledge to easily distribute it across your workforce, building simple and engaging training programs so everyone has the same guidance. The result is faster, safer, and better manufacturing.
Connected Work Instructions
Create standardized, audit-ready procedures that are easy to author and quick to implement.
Go
Operational Training
Distribute accurate knowledge across your workforce and track training progress, all from a tablet.
Go
Continuous Improvement
Capture insights straight from the floor to assess performance and discover opportunities for improvement.
Go
Transformation Services
Lean on our expert team to create an implementation plan, run change management, and help you deploy.
Go
Additional Resources
View All Posts
Continuous Improvement
How the Best Plant Managers Solve Production Challenges
6 min read
As a manufacturing plant manager, meeting production targets, reducing downtime, and filling empty roles are all ongoing goals. The best plant managers know that these goals...
Continue Reading
Work Instructions
The Cost of Bad Work Instructions
10 min read
Bad work instructions are the norm. Documentation is often created to check a box for audit or compliance purposes. But once completed, those work instructions get trapped...
Continue Reading
Continuous Improvement
How to Scale Technology Across Manufacturing Operations with 3M
42 min read
Most manufacturing companies don't have people dedicated to evaluating and deploying modern tools. At best, IT or HR takes responsibility for new technology and doesn't have...
Continue Reading