
Continuous Improvement
28 min read
Mastering Total Quality Management in Manufacturing (TQM) | Strategies and Insights
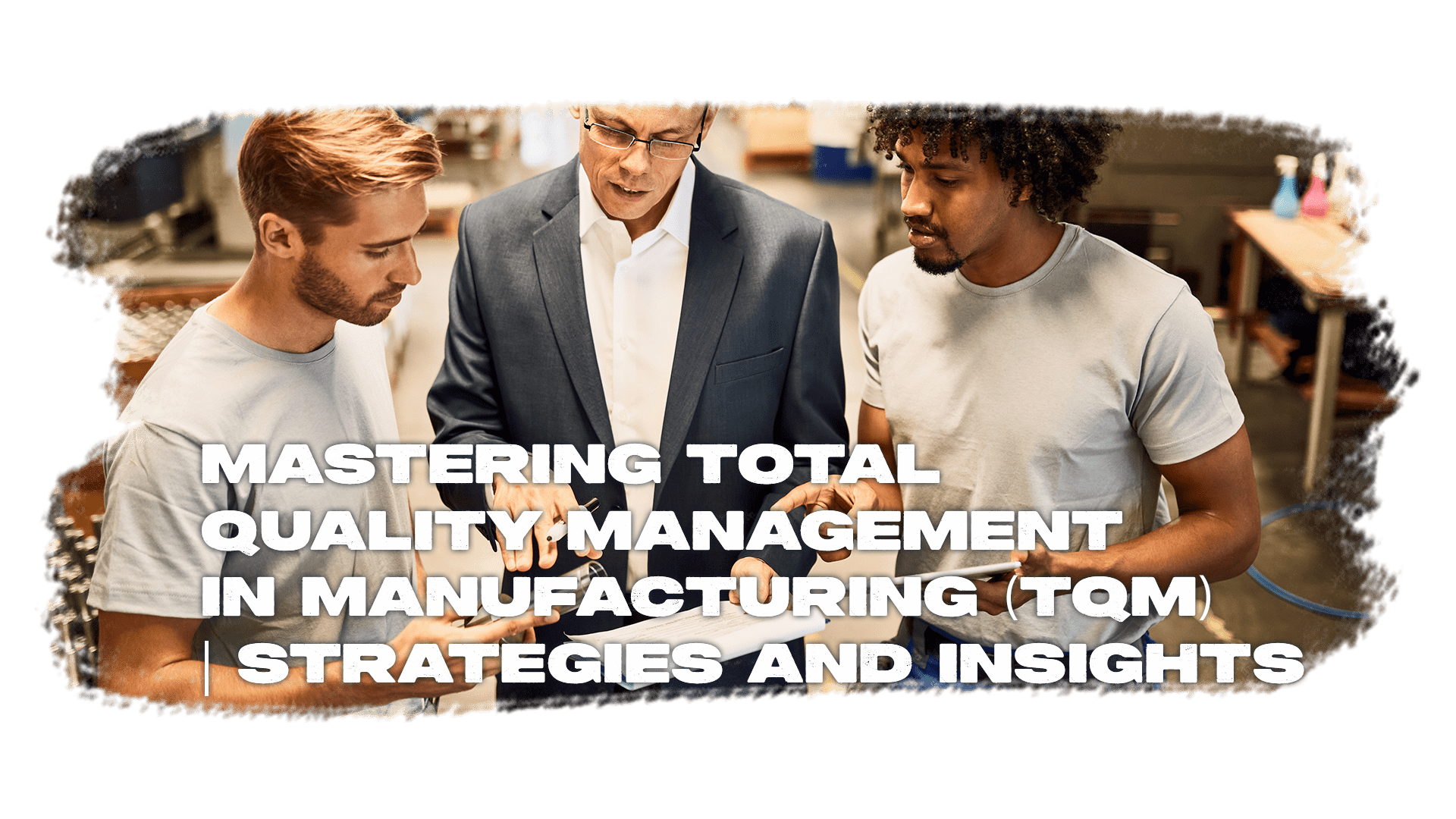
If there’s one consistent thread that unites every manufacturer worldwide, it’s quality. The need to produce a quality product that meets or exceeds the needs and expectations of customers is a driving force in manufacturing.
Table of Contents
1. Benefits of Implementing TQM
3. Challenges & Pitfalls of TQM Implementation
4. TQM Implementation Strategies
7. Quality Metrics & Performance Measurement
8. Supplier Quality Management
9. Employee Training & Development
11. TQM & Continuous Improvement
Total Quality Management is a systematic approach that aims to improve the quality of a product or service. Sounds simple enough. If a company wants to produce the highest quality product possible, it must make a dedicated effort.
According to the ASQ Quality Glossary, quality management is "the application of a quality management system in managing a process to achieve maximum customer satisfaction at the lowest overall cost to the organization while continuing to improve the process."
This definition hits all the marks related to TQM. A systematic implementation that focuses on the customer and strives for continuous improvement.
What many organizations miss is that the need for a structure that supports quality must be present throughout every level of the business.
Businesses can implement TQM in all areas of an organization, including manufacturing, service, administration, and beyond.
And secondly, quality should be intertwined with the customer experience. TQM focuses specifically on customer satisfaction and continuous improvement.
This article will clearly define total quality management and offer some strategies and insights into how to make it work effectively for an organization.
Benefits of Implementing TQM
It would be hard to deny the benefits of a process that improves manufacturing quality.
Total quality management is an approach that is incredibly effective in this task. But more than enhancing the quality, TQM also helps manufacturers reduce costs and boost customer satisfaction. And that's just the beginning.
As for the manufacturing industry, research shows that quality could make a definitive difference. A return focus on growth and competitiveness within the key sectors would restore 1.5 million manufacturing jobs to the U.S.
Improved Quality
Putting systems in place to bolster the quality of products and services would have a far-reaching effect on the overall quality of the outcomes. Quality should be first and foremost at every production plant to remain competitive and keep customers happy.
Reduced Costs
Low-quality products can result in defects, which waste resources, materials, and time. A focus on reducing the potential for faults means manufacturers can cut costs by reducing or eliminating these losses.
Increased Customer Satisfaction
Customers demand quality products. With the market's competition, customers won’t be willing to settle for “almost” or “good enough.” Providing the highest-quality product possible will keep customers satisfied and returning for more.
Improved Employee Morale
There is a direct correlation between quality management and employee morale. Employees want to feel as if their jobs are providing something positive. Working for a company that cuts corners and provides a less-than-satisfactory product will damage employee morale and productivity in the long run.
Increased Productivity
When less time is spent mitigating the fallout from mistakes and dealing with defective products, the business can spend more time on other production tasks.
Better Decision-Making
A total quality management system incorporates everyone and everything within an organization. It relies on complex data, input from workers and supervisors, and statistical analysis. All this information can only help companies make more intelligent, more informed decisions.
TQM & Innovation
Total Quality Management requires an approach that encompasses an organization. Based on the principle of continuous improvement, TQM can help spark innovation within that organization by drawing on the ideas and problem-solving abilities of its most incredible resource – people.
Too many manufacturers put all their time and energy into improving processes and boosting productivity. The drive for those at the big table is always to do more with less.
And while this is the basis of business, a narrow-minded view focused on the numbers can often miss out on the creativity of the people on the front lines.
TQM puts people, and their creativity, at the forefront of problem-solving. With a focus on the needs and wants of the customer, TQM helps organizations pinpoint where those problems lie.
By leaning on and empowering the people within an organization, it allows for learning, creativity, and innovation to figure out how to build something better.
Challenges & Pitfalls of TQM Implementation
Poor implementation of a total quality management system can do more harm than good. The same can be said of virtually any program put in place at an organization without careful planning.
If everyone on the team isn’t on board, getting things moving in the right direction can be hard. And when it comes to quality management, involvement from every employee is essential for success.
Below are a few common challenges and pitfalls that manufacturers face when implementing a TQM system and why companies should be careful when starting a new quality program.
Failure from Management
All good internal programs at any business must start from the top. Management, executives, supervisors, and even the CEO must all play their part in setting the example.
And it comes down to this: do employees understand the why and how of the TQM system, and do they know how to play their part in a successful outcome? Managers must ensure they’re answering these questions.
Inadequate Employee Involvement
Without proper leadership, employees might push back against any new program. Employee push back is especially true if they lack the proper training and education.
Organizations that simply throw a bunch of new rules and regulations at employees without explaining the benefit to everyone within the company will find that employees may not take the changes seriously.
Poor Communication
At the heart of the TQM is communication between all levels of an organization. Employees must be free to express their opinions and come to managers with problems without fearing retribution or dismissal.
Managers must communicate back with employees regarding problem-solving techniques. And above all, organizations must communicate with the customer.
TQM Implementation Strategies
TQM is hard to define because it can look different depending on the specific company and its needs.
So, how exactly does an organization implement a total quality management system, especially when the TQM varies from company to company?
Below is a step-by-step guidebook to doing precisely that.
- Define the Goals
When kickstarting any new system or program, the first step should always be to figure out why. When it comes to TQM, the end goal is the customer.
But the reason needs to be more specific than that. Get into the specifics and look at the complex data. Where are the shortfalls happening? What precisely isn’t working from a quality standpoint?
Secondary to these specific goals should be organizational goals. Or, put another way, cultural shifts within the organization.
How should implementing a TQM change the company's culture, vision, and values? These are the things team members must recognize and accept if the outcome is successful.
- Get Upper Management Involved
As mentioned, nothing works without buy-in from the upper management folks. A TQM cannot be a system that puts forth the idea of “do as I say, not as I do.”
If upper management isn’t playing all-in, it won’t work. And that means dedicating time, resources, and energy to meeting objectives. And it means putting that same energy into the employees.
- Educate and Train Employees
This brings us to the most essential component of the TQM – the employees. These people are actively working to produce the products that will end up in the hands of your customers. These are the people that you are relying on to get it right.
Training workers in the principles of the TQM is the first step, followed by specific training showing them how to meet goals and objectives every day. Give them the tools to succeed, or everyone will fail together.
- Implement KPIs and Follow up on Performance
Once a plan is in place and employees are trained in expectations, the next step is to follow through. Remember to include specific key performance indicators to track progress.
Key performance indicators empower employees by giving them a measuring stick for their success. Ask questions. Get feedback. And identify areas where employees can make improvements.
Customer Centric Approach
Following through on a total quality management system by measuring specific KPIs within the organization itself is a great way to test the effectiveness of the strategies. But let's remember the goal of any TQM system: a happier and more satisfied customer.
Manufacturers must take stock of their progress internally, but more important is gathering customer feedback directly. Doing so maintains that goal of continuous improvement through the eyes of the customer.
It bolsters customer loyalty and helps organizations understand the needs and expectations of their customers.
There are numerous ways to do this, and we’ve listed some ideas below.
- Surveys
- Interviews
- Social Media Monitoring
- Focus Groups
- Feedback Forms
- Reviews
- Testimonials
- Suggestions
- Complaints
The avenues that manufacturers must communicate with their customers are numerous. Some customers will seek out a company with their feedback, especially if it is negative. Others will be happy to provide it if given the opportunity.
Remember that regardless of how an organization solicits feedback from the customer, the most critical part of the process is to act.
Take note of those aspects customers appreciate and value. And seek to improve or rectify those things resulting in less-than-satisfied customers.
Building a TQM Culture
We briefly mentioned company culture earlier regarding setting a goal for a total quality management system. And we’re reiterating it here because of its importance.
Quality should be at the forefront of an organization’s cultural structure and it’s vital to understand what the word “culture” really means.
A culture can be defined as a set of values, beliefs, and behaviors that a group of people commonly shares.
In terms of TQM, that culture should support the principles of a total quality management approach. Focusing on the following characteristics or goals will help instill this culture into the fabric of an organization.
Customer Focus
Putting the customer first is a core principle of the TQM strategy. While it’s easy to draft a company vision statement that claims to do this, following through on it isn’t always as simple.
Customer focus requires consideration of every action the organization takes and its effect on the customer relationship. That means every budget cut, every employee initiative, every change in the production schedule. Include the customer as a member of the team.
Continuous Improvement
A focus on continuous improvement should be at the core of every manufacturer’s culture. Striving always to find ways to improve is one of TQM's core principles.
Building this concept into an organization's fabric will profoundly affect virtually every performance indicator – increased productivity and efficiency, a higher-quality product, reduced costs, and a happier customer.
Employee Involvement
The culture of a company serves many purposes. It unites the employees under a single banner. It gives team members a common goal and vision. And it helps workers understand the positive values they’re working together to uphold.
Teamwork
Sometimes the idea of company culture gets lost in the jargon of business. Employees tire of hearing upper management members drone on in what they hear as "HR speak." That's why upper management needs to get everyone involved with the TQM. Employees need to see it in action, not just hear it from the higher-ups.
Quality Metrics & Performance Measurement
Every manufacturer understands the importance of KPIs. A key performance indicator is a measurable value that helps organizations visualize their success in achieving results.
Tracking KPIs is one of the most accurate and effective ways to ensure activities are aligned with a specific goal. And they're one of the most valuable ways to measure success.
Total quality management is a far-reaching goal. And because it's so hard to define, it's also hard to measure. That's why an organization needs to set specific goals within the framework of the TQM.
Those goals aren't immutable, of course. As the needs of the organization and the customer change, the plans should be revisited and realigned. But the overarching goal remains to provide a higher quality product for the customer.
Organizations can better track their progress by setting goals and defining specific KPIs related to those goals. And they can more easily identify those areas that need improvement. Below are a few helpful KPIs that relate directly to TQM.
- Customer Satisfaction
- Employee Engagement
- Process Efficiency
- Defect Rate
Supplier Quality Management
When discussing a total quality management system, remember that the quality of a product or service is dependent on every step in the production process. But what about those factors that lie outside of the factory floor?
The supply chain itself is an essential component of any TQM because it directly affects the quality of the outcome.
Does the TQM extend, then, to the supply chain and suppliers? It does. Bringing a focus on quality to the supply chain helps companies ensure that their products and services meet employee expectations.
And it provides that only the highest quality resources and materials are used in the production process, minimizing the risk of defects.
Applying TQM to the supply chain can initially seem tricky until organizations remember that many of the same techniques used on the factory floor can serve a similar purpose here. For example:
- Process Mapping
- Root Cause Analysis
- Corrective Action Plans
These tools are designed to uncover problems in a process and find a solution. Applying this kind of systematic problem-solving to issues within the supply chain can provide a significant benefit in the form of better overall performance and an improved ability to gain a competitive advantage.
Employee Training & Development
Employees are the backbone of the manufacturing industry. That’s a known fact. But within the structure of the total quality management system, employees are the fuel that makes the machine run.
Sure, you can put a plan in place for virtually anything, quality included. But without employee participation, that system is simply a stand-in – accomplishing little and just getting in the way.
However, if employees are considered a vital component of a TQM, everyone benefits.
TQM Benefits Employees
Employees allowed to operate within a company culture that prides on quality, thrive.
Employees are more engaged and motivated with their work when provided with the authority and responsibility to make decisions, which is at the core of the TQM. Employees working to bring a higher quality to their jobs are more satisfied overall and more productive within their roles.
The caveat is that this is true with proper training and development. Instilling the principles of the TQM into a labor force must start from the onboarding process and continue through the training process – and even further.
Employees who are provided the opportunity to learn, and apply what they have learned, will return the favor to the organization.
TQM Benefits the Organization
This concept of employee development goes both ways. TQM directly benefits employees. Employees, in turn, use the TQM system to benefit the company and its customers directly.
Given the proper framework and the tools to get the job done, employees can help create that culture of continuous improvement, learning to identify and solve problems to improve quality outcomes.
TQM Tools & Techniques
Instilling quality into every level of an organization is the goal of total quality management. The overarching principles should be instilled at the highest level and included as a sticking point within the company culture.
However, many organizations need help figuring out how to implement a quality management system in the right places.
Thankfully, manufacturers can use many tools, techniques, and methods to help improve the quality of their products and services.
Knowing which tools to use and where to use them will require a careful examination of the specific needs and requirements of the business and its customers.
Below are some of the most valuable tools when it comes to TQM.
- Flowcharts
- Cause-and-Effect Diagrams
- Pareto Charts
- Histograms
- Control Charts
- Check Sheets
The common thread between these quality tools is visibility. Many of these types of charts and graphs rely on data.
Effectively using that data can help organizations identify what's working and what's not. Spotting snags in the system is the only way to improve.
Use the tool that best fits the specific need and matches the analyzed data type. And don’t overlook the benefits of the last two on the list: control charts and check sheets.
Yes, improving quality is dependent on identifying and solving problems. But it must also be ingrained in the daily activities of employees. Putting the right checks and controls in place reinforces this as an expected standard.
TQM & Continuous Improvement
We’ve covered the basics of total quality management, how it benefits organizations and employees, and how it centers on the customer first and foremost.
What must be reiterated is the correlation between TQM and continuous improvement. One cannot exist without the other, and both play an essential role within any manufacturing organization.
Continuous improvement is a concept that encourages companies to look for ways to be better constantly. From a quality standpoint, that means focusing on the customer experience.
Remember that a manufacturer is more than just products from a production line. It’s a complex organism of designers, suppliers, managers, engineers, maintenance technicians, forklift operators, and operators.
It’s salespeople, the marketing department, and the customer service representatives. Every single individual under the umbrella of an organization affects the quality of the overarching customer experience.
And therefore, every individual should be tasked with understanding the responsibility of their role and how it relates to quality.
Continuous improvement is only possible with the employees. And it becomes virtually impossible when an organization fails to empower employees to take ownership of their roles and outcomes.
Final Thoughts
Much has been said here about total quality management and its importance in manufacturing.
Quality management is a concept that uses tools and methods to help organizations improve the quality of their products and services. But the most important takeaway is that TQM is about more than the quality of the actual products. It’s about the quality of the customer relationship.
The customer is at the center of the universe regarding business. Every action taken within the scope of an organization should revolve around its eventual effects on the customer.
Focusing on producing quality products will create a happier and more loyal customer, as long as the guide starts with that customer. Listen to the customer. They pay the bills.
Topic(s):
Continuous Improvement
Related Posts
View All Posts
Continuous Improvement
Streamlining Production: How Lean Manufacturing Can Revolutionize Your Business
23 min read
Manufacturing is a delicate process. So many moving parts must come together just right if the aim is to produce goods of the highest quality in the most cost-effective way...
Continue Reading
Standard Work
Quality Assurance in Manufacturing: An In-Depth Guide to Achieve Customer Confidence
23 min read
It’s time to talk about quality. In this industry, quality is everything, and competition between manufacturers is fierce. Table of Content 1. Key Principles of Quality...
Continue Reading
Continuous Improvement
The Most Common Manufacturing KPIs and Metrics to Track & Why | 2023
19 min read
Manufacturing is a highly competitive industry, and the road to success has been uphill for many businesses over the last several years. Table of Contents Criteria for...
Continue Reading