
Continuous Improvement
23 min read
Streamlining Production: How Lean Manufacturing Can Revolutionize Your Business
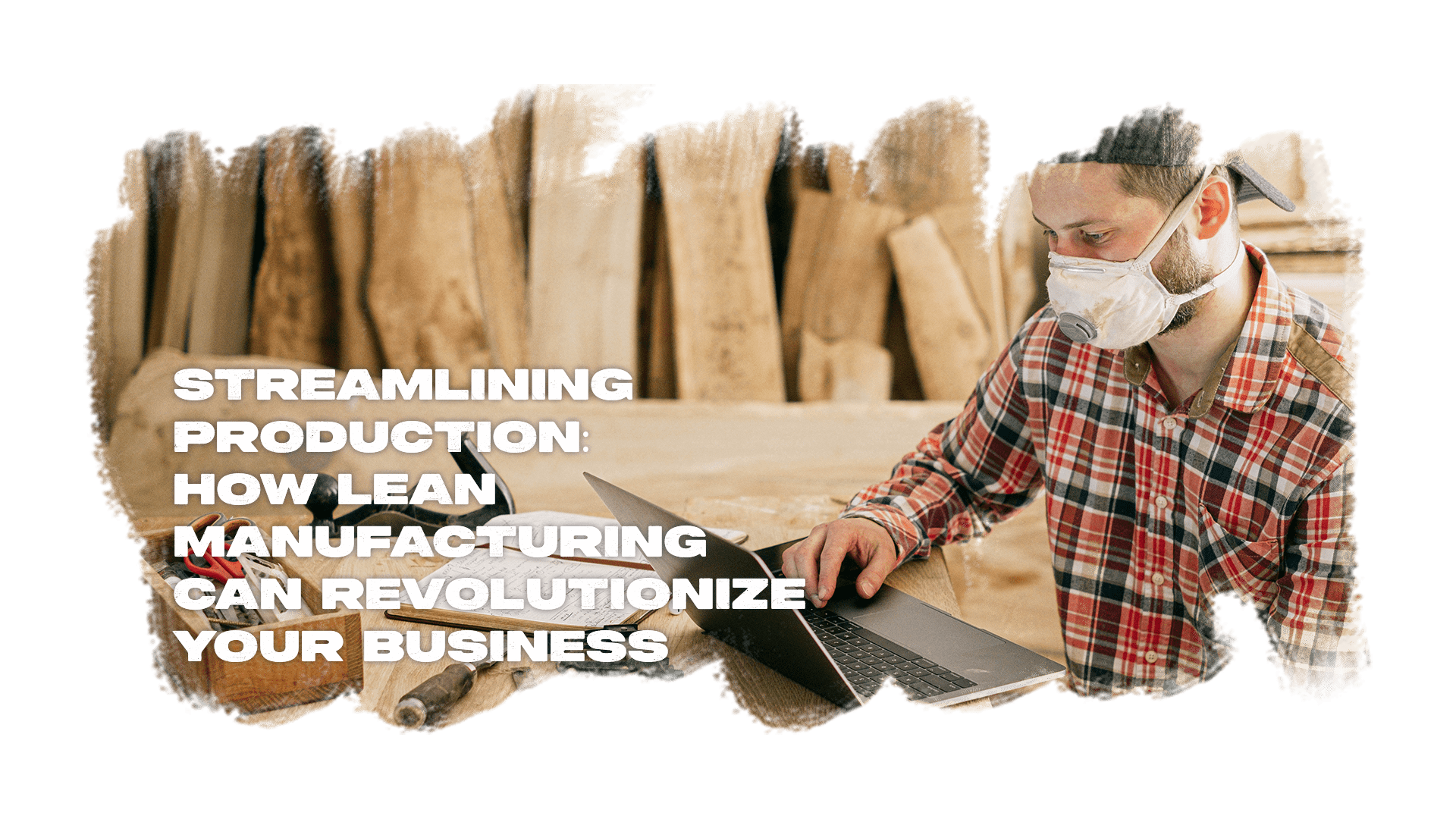
Manufacturing is a delicate process. So many moving parts must come together just right if the aim is to produce goods of the highest quality in the most cost-effective way possible.
And that is the goal, after all; to meet demand, satisfy customers, and keep costs low enough to make a profit simultaneously.
Table of Contents
1. Why is Lean Manufacturing Important for Business and How Does It Work?
2. The Benefits of Lean Manufacturing
3. The Five Principles of Lean Manufacturing
4. How to Create a Lean Culture in Your Business
5. The Eight Types of Manufacturing Waste
6. Lean Manufacturing Tools and Techniques
Due to this careful balancing act, manufacturing companies implement several methods designed to boost productivity and efficiency, decrease waste, and improve the quality of results. One of the best-known of these methods is called "lean manufacturing."
Lean manufacturing is implemented to reduce production time in the most efficient way possible, thereby reducing response times from the suppliers and the customers.
It is related to another production method known as "just-in-time manufacturing," which aims to match the production level to the demand. Lean manufacturing centers on the just-in-time methodology but with extra focus on efficiency, productivity, and waste reduction to meet profitability and quality goals.
The topic of lean manufacturing – what it is and how you can achieve it, is the topic of this article. We will cover the definition of lean manufacturing, explain its basic function, and give some tips on implementing it in your manufacturing processes for a better result.
Why Is Lean Manufacturing Important for Business and How Does It Work?
Lean manufacturing principles are an important part of a successful organization because they revolve around continuous improvement or the notion that a process can always be improved upon. In any business, doing more with less is a great principle.
Manufacturing takes that concept and expands it to include doing more “better” with less by focusing on ways that processes can be streamlined, improved, and perfected. And by eliminating any waste that doesn’t add value for the customer.
This includes physical wastes like defects and excess inventory and non-physical wastes like downtime.
The History of Lean
Many give much of the credit for process control and flow production to Henry Ford, who revolutionized production with the moving assembly line in the early years of the 1900s. However, the idea of lean manufacturing was first developed by the Toyota company in the 1930s and implemented even further post-WWII.
But the term itself was coined by an American businessman named John Krafcik in 1988. It was further defined in the 1990s in two books, The Machine That Changed the World (1990) and Lean Thinking (1996), to include its five key principles: precisely specify value by specific product, identify the value stream for each product, make value flow without interruptions, let customers pull value from the producer, and pursue perfection.
The Manufacturing Extension Partnership, or MEP, is a great example of how lean manufacturing principles can help organizations streamline their production processes for better results. The MEP National Network has implemented over 80,000 lean projects, saving manufacturers $18.8 billion in costs and earning them billions more in sales dollars.
Lean Manufacturing for the Future
The digital transformation taking place in the manufacturing sector over the last decade or so has taken the concept of lean manufacturing to new horizons. Now, digital tools, IoT, and innovation have made lean manufacturing more effective and more accessible for organizations of all sizes.
Manufacturing companies are always looking for ways to improve, and lean manufacturing is one of the most effective ways to do so.
Adopting lean manufacturing techniques can help organizations cut back on waste leading to lost profits and lost productivity, create higher-quality products, and even increase sustainability.
The Benefits of Lean Manufacturing
Part of what makes lean manufacturing so effective is its focus on reducing waste. In 2019, Forbes reported that 20% of every dollar spent in the manufacturing industry is wasted due to inefficiencies.
The total loss of this waste adds up to a staggering $8 trillion, and this number doesn’t even account for the actual physical waste produced by manufacturing companies.
Research estimates that manufacturing and industrial firms on the Fortune Global 500 lose a cumulative 3.3 million hours annually to unplanned downtime. The result is a financial loss of $864 billion, or about 8% of their annual revenue.
Lean manufacturing aims to reduce these wastes while increasing productivity and efficiency. The end goal is to shorten the production time and improve quality by only focusing on those things that add value for the customer while eliminating those that suck resources from the organization, whether physical resources like wasted materials or products or non-physical resources like time and effort.
Operating in this manner provides massive benefits for manufacturing companies. We’ve outlined a few of the big ones below.
Improved Customer Satisfaction
At the heart of any improvement lies the customer. A lean manufacturing environment improves the quality of products that the customer receives. It also reduces the cost of manufacturing, which trickles down to the customer in the form of better pricing. And it speeds up production, which means getting the right products for the customer when needed.
Time Savings
Increased productivity results in another huge return for manufacturers – time savings. Downtime is expensive, as previously noted. And reducing or eliminating that downtime gives valuable hours back to companies.
Cost Savings
A reduction in waste and an increase in productivity and efficiency will save organizations money on both ends. Better use of materials, fewer defects, a reduction in wasted labor hours – the list goes on and on- can save companies millions of dollars.
Adaptability
A focus on lean manufacturing leads to the implementation of innovation and technology. In turn, organizations get the benefit of being able to easily adapt to the rapid changes taking place in the industry and the ability to remain competitive in an evolving landscape.
Sustainability
Operating at a high level of sustainability has become more important for organizations due to increased public pressure and awareness.
Manufacturing companies are responsible for a great percentage of the emissions and waste globally every year. Reducing that waste helps companies save time and money, protects the environment, and increases organizations' public image.
The Five Principles of Lean Manufacturing
In 1997, The Lean Enterprise Institute, or LEI, was founded by James P. Womack and Daniel T. Jones, two of the authors of the books we spoke of earlier, who are responsible for fleshing out the definition of lean manufacturing and defining its core principles.
Those five principles help explain not only how lean manufacturing gets results, but how to implement those practices in any organization. They are as follows: Value, Value Stream, Flow, Pull, and Perfection.
Value
Value is something that is owed to customers by businesses. When there is demand for a specific product or service, manufacturers provide value to those customers by providing that product when it is needed. A high-quality product delivered at the right time for the right price increases value for the customer.
Value Stream
The value stream is the path manufacturers take to arrive at the final product and focuses on the activities that add value to the result. It involves all the steps taken, materials used, machinery and tools involved, and processes performed to get to that end goal.
Flow
Eliminating those steps that detract from the value of a production process can leave holes in that process.
Focusing on flow is the next step in lean manufacturing because it ensures that what’s left of the process after non-value-adding steps are removed still "flows" as necessary. The flow of a process starts at the beginning and ends with the customer.
Improving flow often requires organizations to break down siloed information and take a big-picture approach. Inter-departmental communication is key to keeping the processes flowing in the most effective and efficient way possible.
Pull
Pull refers to how customers “pull” the products from manufacturers when they’re needed the most. Think of it like demand. When there is demand, customers pull from inventory. Lean manufacturing focuses on providing the inventory to meet that demand without allowing excess to build up and forcing the customer to wait.
Lean manufacturing means providing the right amount of inventory at the right time, eliminating customer wait times while avoiding inventory stockpiling.
Perfection
The fifth principle of lean manufacturing goes back to the goal of continuous improvement. Is perfection in any system possible? Maybe, and maybe not. But focusing on reaching that glorious goal drives the ideal of continuous improvement.
Reaching perfection means adopting the ideals of lean manufacturing throughout an organization, from the board room to the plant floor, and through every employee in-between.
And it means constantly looking for ways to improve, improve processes, reduce waste even further, and add more value for the customer and the organization.
How To Create a Lean Culture in Your Business
Talking about lean manufacturing principles is one thing; implementing them in a real-world environment is another. Many organizations struggle with this part because they don’t know where to start.
Revamping and rebuilding entire processes can seem costly and overwhelming. But the result is worth the effort. And it doesn’t have to be as hard as it seems.
Implementing lean manufacturing principles in an organization requires building them into the culture. Suppose every employee understands that these principles are an expected way of life on the plant floor. In that case, lean manufacturing becomes a part of daily operations and is much easier to implement.
Training and More Training
Putting lean manufacturing at an organization's core starts with a people-first approach. The employees are the front line of any business and can make or break any initiative. Training workers to understand the foundation of lean principles and how to apply them in their daily tasks will help create that culture.
People are the driving force of the processes. They build the designs. They create the processes. They look for ways to improve. They work the machinery. Proper training is the only way to create an organization that is value driven truly.
Monitoring Performance
Standards and expectations, when built into the culture of an organization, help drive value. But expectations aren’t enough if employees and processes are being monitored correctly.
Monitoring the performance of employees is a typical practice in businesses. But to truly build a lean culture, that monitoring needs to extend to all aspects of operation and include the results of each step in the processes themselves.
Creating a Culture
Building lean manufacturing principles into an organization's culture means creating a unified vision – a purpose behind what you’re doing. The end goal is to provide value for the customer, but a true vision and culture go beyond that.
It involves the organization's goals, what it is trying to build for its team members in terms of career opportunities, and the value it adds to their daily lives. And it centers around the mission of the organization itself, what it stands for, and what it aims to be today and in the future.
Face the Challenges
Part of implementing any new system is navigating the challenges that come with it. Nothing is ever as easy as one, two, three: go. There are bound to be obstacles, but the best way to face them is to see them as learning opportunities.
Encourage Open Communication
The bigger the organization, the bigger the siloes of information. Those siloes can help departments better focus on their specific tasks and talents but can also create barriers to improvement.
Breaking down the walls between departments can keep lines of communication open and can help identify areas where improvements are needed and necessary. This includes communication between upper management, supervisors, designers, engineers, and plant workers. Having everyone speaking together on the same party line is essential.
Try and Try Again
Continuous improvement requires a system of trial and error. Old and inefficient processes are eliminated and replaced by better, more value-driven processes. And you won’t know how well those processes work until you test them in real-time.
Don’t think of this as another opportunity for waste but to an end. Trial and error are the best way to see the real results of a change and should be seen as an opportunity to learn, gather data, and make even further improvements.
Manufacturing Waste
At the core of lean manufacturing is waste reduction. But to apply this concept the correct way, it’s vital to understand what “waste” really means. In the most applied definition, waste refers to wasted materials and defective products. But in building a lean culture, waste refers to anything that doesn’t add value to a product or service.
The Toyota company originally identified seven types of waste when creating the ideals of lean manufacturing, and an eighth type was added along the way. They are:
- Transport
- Inventory
- Motion
- Waiting
- Overproduction
- Overprocessing
- Defects
- Unutilized Talent
The Eight Types of Manufacturing Waste
Transport
The unnecessary movement of materials or products is considered transport waste. Wasted steps can take up time that could be spent elsewhere and waste the resources required for that transport. This type of waste is often the result of poor planning and facility layout, unorganized scheduling, and poor production planning.
Inventory
Inventory waste refers to any supply that exceeds the requirements for the just-in-time method and occurs when the concept is abandoned or poorly executed. Inefficient demand forecasting and inventory management, as well as poor production planning, can result in excess inventory and wasted time, money, and resources.
Motion
Transport waste refers to the unnecessary movement of materials, while motion waste refers to the unnecessary or wasted movement of people. Extra steps, movements, bending, and lifting that could be avoided are considered motion waste, as are wasted steps in the production process.
This type of waste takes a huge toll on not just the organization but the health and well-being of the workers themselves.
Waiting
Downtime is a value-killer. Waiting for waste refers to any time a process is stalled because of a breakdown in the system itself.
This type of waste often occurs as an unplanned event due to equipment breakdown and production bottlenecks. But it can also occur because of poor planning. A lack of standard procedures and inefficient processes can result in one party waiting for another or an operator waiting for equipment or materials.
Overproduction
Overproduction results in unnecessary inventory build and is once again the result of poor planning and forecasting.
Being more productive is great, but without careful planning and a focus on efficiently producing the products required to meet demand without wasting effort on unrequired inventory, that productivity is targeted at the wrong task and results in waste.
Overprocessing
Poorly built processes include steps that are unnecessary and don’t add value for the customer. Overprocessing is, unfortunately, often the result of poorly implemented lean manufacturing. More doesn't always mean better; too much data and information can have a bounce-back effect. Poor decision-making, over-analyzing, redundancy, and inefficient process building result in overprocessing and wasted effort.
Defects
The most thought-of type of waste in manufacturing is defects. Defect waste could refer to defective final products, lost materials, and the rework or repair work required to remedy a problem.
Human or mechanical error can lead to defect waste. But so can poor production planning and processes, lack of standards, training, excess inventory, storage, and unsafe transport processes.
Unutilized Talent
The last type of waste was added to the list to pinpoint the waste of human resources and the under or unutilized talents of the workers.
Whether it's due to an unintentional oversight that allows talent to go wasted, poor production planning that leaves workers performing tasks below their skill level, or a lack of communication between departments, it all results in a loss of value for the organization and the customers.
Lean Manufacturing Tools and Techniques
There are many tools and methods that organizations can use to help them navigate the principles of lean manufacturing. Many have been around for decades and are common terminology within manufacturing facilities.
Kaizen
Kaizen revolves around continuous improvement and requires organizations to focus on activities that further that goal. Kaizen starts from the top down and considers every team member's contribution and input. As problems occur, team members identify and seek to find solutions to those problems. This is Kaizen.
Total Quality Management (TQM)
In a big-picture sense, TQM is an umbrella concept that touches on every system, person, material, and process in an organization. TQM keeps every member of the team accountable for results and drives lean manufacturing principles by tasking everyone within an organization to identify areas ripe for improvement.
This could mean better training and hiring practices, improved supply chain partners and practices, and improved processes, all aimed at identifying and eliminating waste and errors.
Kanban
Kanban is a production scheduling system that helps organizations promote lean manufacturing by tracking and optimizing production. Kanban uses a system of cards to communicate production needs further up the line. Kanban helps teams eliminate overproduction waste by targeting resources where and when needed.
Jidoka
Focused on catching and reducing defects as they occur within the production line, jidoka works in conjunction with both human and automation systems.
When an automated system detects a defect, it will cease operations and allow human intervention to identify and rectify the problem. This prevents unnecessary defect waste by halting production and pinpointing problems as soon as they occur.
Value Stream Mapping (VSM)
Organizations often use what’s called “value-stream mapping” to visualize the flow of materials through the production process.
This process starts at the beginning, with the design itself, and flows through every department that touches the production process. Eliminating steps that don’t add value is key to the lean manufacturing process.
Standardized Work Documents
The key to reducing variations in results is to have a set of predefined standards and ensure every team member understands how to achieve those standards.
Standard operating procedures and process requirements help employees maintain continuity and safety during operations, eliminate waste, prevent accidents, and add value to the overall system.
Final Thoughts
Lean manufacturing is a concept that has built momentum and importance throughout the last decade. Organizations have come to understand the importance of doing things better and continuously striving to add value for the customer.
Lean manufacturing principles center on this idea, and help organizations maintain a competitive edge in a rapidly evolving industry.
Reducing waste in any organization is beneficial. Increasing efficiency and productivity should be goals that are at the top of the chain of importance if manufacturers want to grow and be successful.
Adopting a lean approach to operations from the top down is the best way to reduce waste, reduce costs, improve profitability, streamline operations, and enhance the customer experience and overall satisfaction.
With the implementation of digital tools, Industry 4.0, the IoT, and automation in manufacturing facilities, lean manufacturing is changing.
These advancements make the ideals of lean manufacturing easier to accomplish when implemented correctly, but even progress can be wasteful if organizations aren’t careful. Proper planning and well-defined standards should remain constant in manufacturing facilities, not an afterthought.
Lean manufacturing is more achievable than ever before for manufacturing facilities. Focusing on maintaining and communicating standards, implementing innovation in the most effective way possible, and constantly striving for improvement will build a solid foundation for companies to carry forward into the new millennium.
Topic(s):
Continuous Improvement
Related Posts
View All PostsThe Most Common 8 Wastes of Lean Manufacturing & How to Manage Resources
23 min read
Manufacturing is all about making the highest quality products at the lowest cost. Reaching that goal means searching for and eliminating causes of wasted time, wasted...
Continue Reading
Continuous Improvement
Why Do Value Stream Mapping? | Benefits & Examples
22 min read
A successful business incorporates two critical factors, customers, and cost. The goal of any business is to provide the most outstanding value for the customer at the lowest
Continue Reading
Standard Work
How To Reduce Defects in Manufacturing in 2022
24 min read
Product defects are a pain at any manufacturing company. When all the time, energy, and money that is spent to produce a product is wasted due to defects in the final...
Continue Reading