
Frontline Digital Transformation
8 min read
Frontline of the Future: Part 1
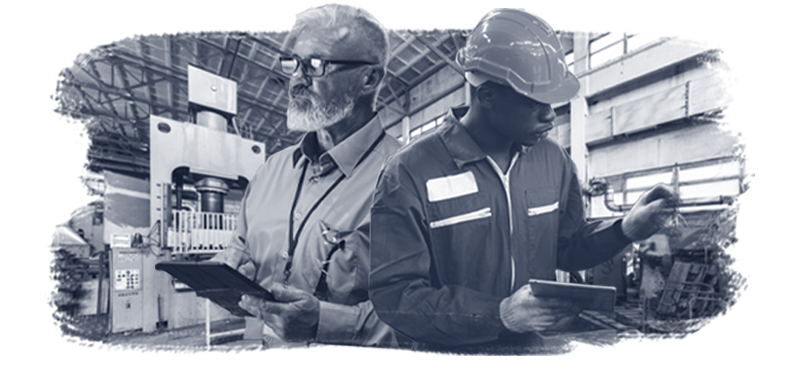
Historical Forces Impacting Manufacturing
At Dozuki, we have our finger on the pulse of manufacturing trends.
We believe it’s part of our mission to formulate clear insights into the future of this industry.
And in the next decade, we foresee technology evolving dramatically faster than most expect, and it will radically change the manufacturing landscape.
Dozuki has spent the last decade helping hundreds of industrial businesses across the world develop and scale their frontline digital transformation initiatives. We talk to leaders every day who are tackling digital projects, but have no idea where to start when it comes to the frontline workforce.
Many manufacturers have only scratched the surface of digital exploration. There is tons of work to be done to tie frontline workers, processes, and their systems together to operate at maximum efficiency.
That’s why we’re launching this new series. We’ve built out a manufacturing curriculum just for your team, called the Frontline Of The Future. Over the coming months, here’s what you can expect to learn:
Part 1: History
Part 2: Processes
Part 3: Accessibility
Part 4: Training
Part 5: Communication
Part 6: Analytics
Part 7: Technology
Part 8: Alignment
Part 9: Frontline
Part 10: Improvement
Please note, this article is only the beginning. You can read the entire series in ebook form right now:
In this foundational module, we’ll share our definition of the frontline of the future. Then we’ll review the evolutionary forces impacting the industry, and how you can thrive in the face of them.
What Is The Frontline Of The Future?
In manufacturing, the frontline is the intersection of people doing work, the process, which is the standard, and the ultimate production it drives.
The frontline of the future is connecting people and processes with digital tools for communication, standardization, training, reporting, and more. Here’s the model we use both internally with our team, and externally with our customers.
This model dispels the pervasive myth that technology will automate you out of people in manufacturing. That’s patently untrue.
People are an invaluable part of the process. Here’s proof:
- According to an analysis by Kearney, 72% of tasks in the factory are still performed by people. People aren’t disappearing, they’re simply evolving. All species do it.
- Wharton recently studied robot adoption and economists found that companies that adopted more robots hired more people, while also improving the quality of their products and services.
- NAM’s analysis showed that 77% of firms are having difficulty attracting and retaining talent
- Deloitte’s report showed that 68% of manufacturers believe there is a skills shortage in the industry
- McKinsey’s guide on people power showed that 97% of digital transformations that don’t engage the frontline fail.
In our experience, if you’re starting with technology, you’re starting wrong. The most successful and sustainable manufacturing companies start with people, and the technology comes later.
And before they do so, there are large forces to consider.
Evolutionary Forces Manufacturers Are Fighting
A key driver of the frontline of the future is timing. Numerous outside forces have converged to bring us to this critical moment in manufacturing history. In the past few years alone, there has been a confluence of social, economic, cultural and financial factors at work.
Consider the ever expanding list:
- Consumers reshaped habits in the pandemic
- Covid shutdowns created global supply chain disruptions
- Aging manufacturing workforce is leading to talent and knowledge loss
- Plant managers are fighting employee absenteeism and low retention
- There’s a batch of macroeconomic and regulatory headwinds increasing costs
- Operations managers struggle to retain young, engaged, self-sufficient frontline workers
- Labor has become more expensive and requires efficient, cross trained teams
- Geopolitical conflict has accelerated the reshoring of manufacturing
- Government reshoring demands more efficient technical training
- New technology is ushering in the fourth industrial revolution
Everyone is starting from behind.
And yet, manufacturers can’t solve this problem by throwing more technology at it.
Slapping an augmented reality headset on every frontline worker isn’t the answer. The concept of smart glasses on frontline workers is many years out into the future. Right now, it’s about layering familiar technology and digital tools on top of the manufacturing organization.
We believe the frontline of the future relies on current technology widely adopted today, not future technology that will be widely adopted thirty years from now.
Manufacturers (just like any company) can easily over engineer digital solutions. They might try to solve a quality problem with smart glasses, but then go overboard with the tech. And wind up with more process waste than they started with.
To paraphrase the wise philosopher, The Notorious B.I.G., “Mo tech, mo problems.”
But the industry is evolving.
The New York Times recently published a piece titled, Factory Jobs Are Booming Like It’s the 1970s, and the numbers show U.S. manufacturing is experiencing a rebound, with companies adding workers amid high consumer demand for products:
“American manufacturers cut roughly 1.36 million jobs from February to April of 2020, as Covid-19 shut down much of the economy. As of August this year, manufacturers had added back about 1.43 million jobs, a net gain of 67,000 workers above pre-pandemic levels.”
Dozuki is privileged to work with these remarkable and resilient manufacturing companies. It’s clear to the leaders we work with that frontline digital transformation is essential to future success.
And as your company pursues digital goals, we’re thrilled to be joining you on that journey.
We hope this introductory lesson has given you context for what the frontline of the future is, and why it’s necessary.
In our next installment, we’re going to dig into the meat of this series, starting with our favorite word in the manufacturing vocabulary. Process.
Read part 2, Digitizing Your Processes.
Topic(s):
Frontline Digital Transformation
Related Posts
View All Posts
Frontline Digital Transformation
Creating The Frontline Of The Future, Part 9
6 min read
Workforce Development You’ve probably heard the adage, the tool is as only as good or bad as the user. We believe this principle has broad applications in digital...
Continue Reading
Frontline Digital Transformation
Creating The Frontline Of The Future, Part 7
9 min read
Technology Enables Resilience Do you know what the first manufacturing technology was? Let’s go back to prehistoric times, over two million years ago. The Stone Age...
Continue Reading
Frontline Digital Transformation
Frontline Of The Future, Part 3
5 min read
Accessibility Creates Profitability Manufacturers that don’t provide broad access to essential knowledge are at a significant deficit. This form of content debt comes at a...
Continue Reading