
Frontline Digital Transformation
6 min read
Frontline of the Future, Part 2
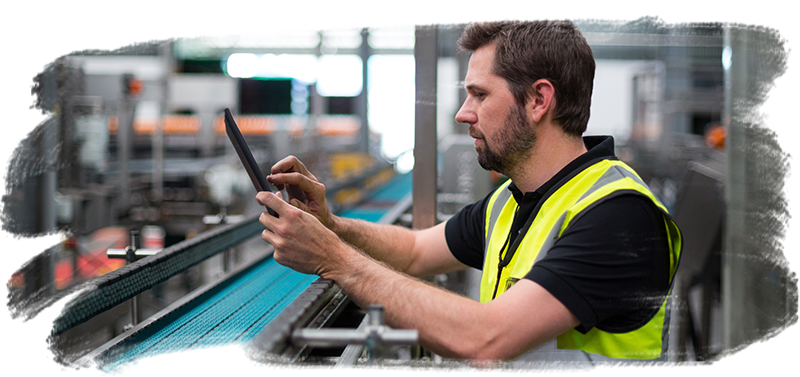
Digitizing Your Processes
Do you have a process for process?
Or are disconnected paper systems preventing valuable efficiency gains?
Most manufacturing companies would say the latter. They’ve one scratched the surface of digital exploration. And in order to operate at maximum efficiency, they need to start from the fundamental core of what makes manufacturing work, process.
In our industry, process is much more than a series of actions or steps taken in order to achieve a particular end. It’s also a vision for collaborative problem solving. Process is a human centric horizon that creates operational leverage for the entire organization.
And yet, outdated, inefficient and even nonexistent processes seem to be the norm.
Just recently we spoke with one of our customers, who runs a large transportation company. They’ve been in operation since the late seventies. We spoke with the director of IT, who has hundreds of employees and hundreds of million dollars in revenue. And she explained that only a few years ago, they were still acting like a mom and pop shop, as far as their processes went.
“Paper documentation would be scanned and stored on a server. It was a convoluted, jumbled mess, and was difficult for plant managers to find what they needed. And that work order flow hindered our ability to be proficient on the shop floor.”
Imagine your company had seven different engineering managers who were all doing the same task, but in seven different ways. How productive would your process be?
This customer case study isn’t unique, because this situation isn’t uncommon.
We see it all the time:
Documented standards? Few to none.
Process strategy? Not for creating or updating.
Updating protocol? Only manual revisions on spreadsheets.
Content types? Walls of text and low quality photos.
What’s your version of this?
Think about the standard for how process updates are distributed to front line workers.
Do you have nothing at all? Does it depend on the supervisor? Do you have a paper log to track when versions are removed from circulation?
Thankfully, that’s the old way. Over the next decade, we predict frontline digital transformation programs will look more like this:
Is your process ready for the frontline of the future?
Here’s what we recommend:
-
Leverage young workers to reach legacy workers. If your process documentation is subpar or nonexistent, use your incoming workforce to document processes being done by the outgoing workforce. Remember, every facility has both experts and non-experts, and now they can collaborate. If your legacy workers have spent their careers not documenting, that means they will not start doing it just because you told them to. But the young workers who have boundless curiosity and energy will. Ask them to record and codify those processes. Veteran workers will feel honored to have their ideas captured, younger workers will get training, and the organization will not have to worry about tribal knowledge leaving the building inside certain workers’ heads.
-
Embrace the productivity of constraints. All of Dozuki’s Guides look the same. No matter who builds it, and no matter which company uses it, there are only so many bullets and words available. This keeps instructions tight, lean and focused. We intentionally built our product to have such constraints, as it gives workers a standard framework for building processes. This ultimately leads to a unified strategy to leverage tribal knowledge. Whether you use Guides for procedural standards; or Wikis for knowledge capture, all the relevant information will be concise, accurate, updated and accessible to all.
-
Enlist third party support to do the heavy digital lifting. If you’re faced with the massive undertaking of transferring paper documents into guides, we’ve got your team covered. Many of our customers come to us with five hundred processes, and simply don’t have the manpower or time to dedicate to those projects. Dozuki’s Services team of technical writers who take on that endeavor. They will come on site and help put your processes into proper format for maximum usability. Dozuki’s document conversion services provide customers with an efficient and trouble-free way to launch new and existing work instructions to the platform.
Ultimately, the key to processes working for the company is, the newest people have to be trained on the latest and greatest version. You might have the latest version of a procedure written and documented, but if everyone is trained on old versions, it’s useless.
The good news is, if you tap into the resource of tribal knowledge, you not only make your company more agile, but more resilient, so you’re not so dependable on individuals. You can really share knowledge and make sure that everybody within the company as well. Every one of your team members can contribute learnings from their valuable experience as you define your perfect process.
Soon you’ll have a process for your process, ensuring your frontline of the future is resilient, adaptable and able to support the evolving industry.
The pillar of “process” is the human centric horizon that creates operational leverage for the entire organization. And we’re just getting started.
Next lesson: accessibility.
Topic(s):
Frontline Digital Transformation
Related Posts
View All Posts
Frontline Digital Transformation
4 Ways Digital Tools Improve Quality
9 min read
Twenty years ago, digital tools were “a thing.” Now they flow through all things. To some degree, every manufacturer is now a digital company. And with the right modern...
Continue Reading
Frontline Digital Transformation
Frontline Of The Future, Part 6
7 min read
How To Staff Your Front Line Without ExcelOne of our customers, a plant manager at a chemical manufacturing company, made this observation:“Getting the time to train every...
Continue Reading
Continuous Improvement
Operational Resilience Explained
11 min read
America was built on manufacturing.And manufacturing was built on resilience. Our country has proven to be a place where workers who are skilled with their hands (and have...
Continue Reading