
What is Frontline Digital Transformation?
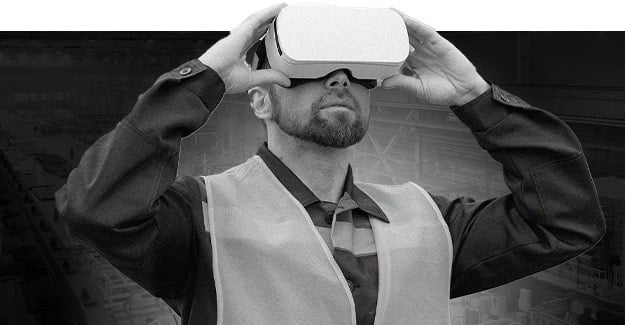
Manufacturing leaders agree that adopting digital technology is essential to future success.
Despite this mindset, 84% of digital transformations fail to improve performance and equip businesses to sustain changes in the long term.
84% of digital transformations fail
For manufacturers, this can be especially challenging because the frontline workforce comes with unique challenges and requirements.
"Digital Transformation" is an industry term that has broad application, but what does it mean for manufacturers and the operational workforce? How is digital transformation different... on the frontline?
Different Buying Practices
Manufacturers are familiar with traditional buying cycles such as purchasing a new machine, for example. The purchase is usually handled by a single department and once deployed, it's the job of maintenance technicians to keep it running.
Digital tools demand a more catered approach.
"It really has to be a cross-functional team to make it go from pilot to deployment a lot smoother. But it's initiated by what we call an 'Operational Technology Team'"
Michael Muilenburg, Director of Operational Technology, 3M
It's time to rethink traditional buying practices. To remain competitive, manufacturers need to align digital initiatives across the entire organization and take a cross-functional approach to evaluating/deploying new tools. Companies need to dedicate the proper resources and tackle digital initiatives with focus.
Changing Technology and Behavior
New buying practices aren't the only distinction of digital tools on the frontline. After solutions are chosen, behavioral changes must occur for the benefits to be realized.
72% of tasks are still performed by people
72% of tasks on the factory floor are still performed by people. Even though the industry has made strides in automation and robotics, the modern factory is still reliant on human performance.
Adding digital tools to the mix doesn't automatically change how those people work. Frontline Digital Transformation (FDX) requires people in your business to behave differently in order for it to be successful.
Successful frontline digital transformations tap into the right workforce needs and communicate changes with them strategically. If you ignore their experiences and communicate poorly then the workforce won’t adapt properly to leverage the benefits of the new (and often expensive) tools. Manufacturers need to understand that digital transformation is more about changing behavior than changing technology.
Our Secret Playbook
Bringing digital tools to the frontline can be intimidating because of its unique challenges. We talk to manufacturing leaders every day who are looking to tackle Frontline Digital Transformation (FDX) projects but don't know where to start.
After years of helping companies find success with digital tools, we've finally released our exclusive guide for Plant Manager success in leading FDX projects.
Develop the skills you need to plan, build, and scale frontline digital transformation initiatives that have a real impact on performance.Become a leading Plant Manager in the modern manufacturing era.
Related Posts
View All PostsHow Smart Factories are Impacting Productivity
Deloitte research suggests that "smart factory" initiatives have yielded an average of 10-12% increase in labor productivity gains. Despite this success, a majority of...
Continue Reading6 Shocking Stats for Manufacturing Leaders
After years of research, our show producer, Corey Brown, shares some fascinating statistics that will shock many leaders in the manufacturing industry. In this special...
Continue ReadingTop Challenges Impacting the Frontline Workforce
Even with advancements in technology and automation, the frontline workforce remains essential to modern manufacturing operations. In fact, 72% of factory work is still...
Continue Reading