
Training
7 min read
How to Write Better Lockout/Tagout Procedures
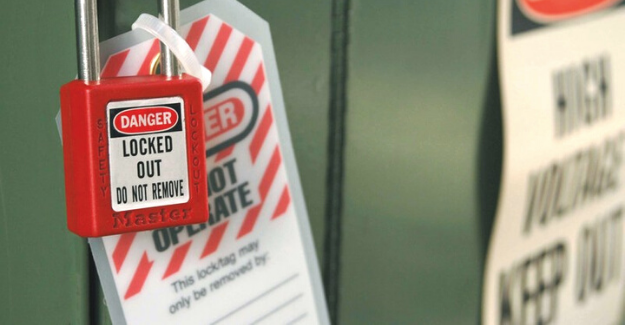
Lockout/Tagout (LOTO) procedures are some of the most common in industrial and manufacturing environments. Despite this, failure to adequately train employees on LOTO procedures continues to be one of OSHA's top 10 most frequently cited violations during federal inspections.
To write an effective LOTO procedure requires both an understanding of OSHA’s guidelines, as well as good communication and training practices. By combining these strategies, manufacturing companies can ensure the health and safety of their workforce while maintaining operational efficiency.
What is a Lockout/Tagout (LOTO) Procedure?
LOTO programs require that all sources of energy are controlled during any servicing or maintenance of a machine. The OSHA Lockout/Tagout Standard (29 CFR 1910.147) provides clear requirements for creating and training employees on safety standards. Properly documenting these procedures is required by OSHA to ensure that machinery is safely turned off and locked or tagged.
According to OSHA’s guidelines, lockout/tagout programs consist of any specific procedures designed to, “safeguard employees from the unexpected energization or startup of machinery and equipment, or the release of hazardous energy during service or maintenance activities.”
A “lockout” procedure ends with the use of a locking device, which ensures the machine remains in the safe or ‘off’ position unless a key or extreme measures (like a bolt cutter) are used to unlock it. In contrast, a tagout procedure ends with a tag fastened to the machine, warning employees to not turn on the machine.
OSHA’s Lockout/Tagout Procedure Guidelines
- Notify all affected employees
- Shut down the machine
- Disconnect or isolate the machine from the energy source(s)
- Apply the lockout or tagout device(s) to the energy-isolating device(s)
- Release, restrain, or render safe all potential hazardous stored or residual energy
- Verify the isolation and deenergization of the machine.
Tips for Writing Better LOTO Procedures
At Dozuki, we specialize in improving communication and employee performance. After working with hundreds of customers, we’ve learned how to write better procedures and work instructions that have huge impacts on quality, safety, and employee performance.
Clearly Define Safety Equipment
Define your safety equipment and PPE in your LOTO documentation using visuals. OSHA specifies that any required safety gear and personal protective equipment (PPE) be defined clearly and that the employee is provided proper training to use said equipment.
This is where companies sometimes make dangerous assumptions. Not everyone knows how to use a torque wrench. Don’t assume the skill or knowledge levels of your employees.
Identify LOTO Devices with Visuals
Illustrate the location of all LOTO devices using images or videos. Industrial machines, circuit breakers, plugs, switches, push buttons, and valves are just some of the items that often require lockout and/or tagout devices.
Clearly communicate these items in your written procedures by including images and detailed descriptions. One study found that groups following specific technical procedures performed 65% better when following material with visuals. Text-only work instructions are insufficient when it comes to essential processes — your employees deserve better.
Use Direct and Concise Wording
Lockout/tagout procedures aren’t suggestions, they are meant to be followed. Use the active voice by starting all sentences with a verb. This approach immediately sets the stage for the ‘who’ and ‘what’ of the procedure. As a result, the employee clearly understands what is expected of them.
To further improve clarity, say what you mean without wishy-washy words. Words like "mostly," "slightly," "seems," and "somewhat" are built-in loopholes. Avoiding these words give your instructions more authority and clarity.
Record Verification Methods
When a machine has been de-energized, operators must verify that the machine will not turn on or re-energize. This is typically done by attempting to turn the machine back on or checking indicator readings.
Record successful lockouts and note if anything was different or challenging. This system of record is invaluable for troubleshooting future incidents and identifying areas for improvement.
Include Troubleshooting Information
Many times documentation only informs on how to perform a task if everything goes well. Unfortunately, this isn’t always the case. Where most LOTO procedures fall short is in their ability to solve for problems.
While it can become an information overload to include solutions for all possible scenarios, connecting your LOTO procedure to essential troubleshooting information can save thousands of dollars in unplanned downtime and quality costs.
Use Modern Tools to Notify Affected Employees
Before beginning any lockout/tagout procedure, operators should notify all affected employees that the machine will be shut down and locked out to perform service, maintenance, or a changeover.
In your written procedure, specify who needs to be notified and clearly describe how to notify said employees. Digital tools have an advantage here because they can communicate notifications instantly and ensure that you’re reaching the right people.
Good Procedures are Accessible Procedures
It doesn’t matter how well you write your Lockout/Tagout procedures if your employees can’t access them. Finding the proper LOTO information should be simple and intuitive.
Traditional stacks of paper binders no longer meet the demands of the modern manufacturer. Use a digital system that prioritizes ease of use and accessibility. This will ensure that the LOTO procedures are used, provide adequate training, and are always up-to-date.
For more tips on communicating essential procedures, download our free Guide to Better Work Instructions.
Related Posts
View All Posts
Training
Deadly Instructions: Using Visuals to Train Safely
7 min read
In 2016 OSHA reported 2.8 million workplace injuries, with 440,000 of them occurring in the manufacturing industry alone. For manufacturers, that means for every 100 workers,...
Continue Reading
Product
How to Use Dozuki for Work Instructions
7 min read
Dozuki is the leading digital work instruction tool for industrial businesses all over the world. Our platform enables better employee performance by improving how you...
Continue Reading
Training
6 Common Manufacturing Facility Hazards & Effective Solutions
20 min read
Manufacturing facilities serve an important function in a country’s economy, as they create jobs, increase wealth through added value and taxes, promote trade, and support...
Continue Reading