
Training
20 min read
6 Common Manufacturing Facility Hazards & Effective Solutions
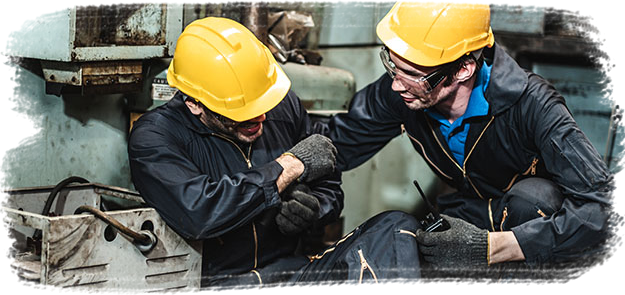
Manufacturing facilities serve an important function in a country’s economy, as they create jobs, increase wealth through added value and taxes, promote trade, and support other industries and services that rely on manufactured goods.
One of the biggest threats to a stable manufacturing industry is a lack of safety standards for common facility hazards.
Manufacturing facility hazards result in time off, lowered production, and serious injury, illness, or even death for employees.
In this article, we will discuss the significance of enforcing health and safety standards and the role that risk assessment plays in helping manufacturing companies manage both routine and unanticipated threats.
We will better understand the six of the most common manufacturing facility hazards and tips for eliminating or reducing them in the workplace.
What Are Manufacturing Facility Hazards?
The health and safety hazards present in a manufacturing facility include risks that are unique to the industry.
Certain hazards can be easily identified and rectified, while others result from the manufacturing process and must be managed through routine safety protocols.
A commonly occurring hazard, like the use of chemicals in a production process, can quickly escalate to an emergency. Some hazards pose an immediate risk to employee safety, while others may result in a cumulative effect.
Common manufacturing hazards include:
-
Safety Hazards – Physical dangers caused by the general environment and operation of heavy machinery include the risk of falls, burns, electrocution, amputation, and even death.
-
Chemical Hazards – Chemical dangers include, for example, the use of hazardous materials or their synthesis as a result of production operations. They can cause serious harm, including immediate danger resulting from exposure, or illnesses related to long-term exposure.
-
Biological Hazards – Mold, bacteria, and viruses are examples of biological hazards. Managing biological contaminants has become even more important, since the rise of the Covid-19 pandemic, and companies have had to rethink safety protocols to protect workers.
-
Ergonomic Hazards – Repetitive motions, lifting heavy objects, and exposure to repeated vibrations or loud noise can cause long-term damage to employee health.
OSHA (the Occupational Safety and Health Administration) has resources available to help companies identify, assess, and manage the risk from manufacturing facility hazards.
Keeping detailed information about workplace hazards, such as safety data sheets, inspection results, and incident reports can help companies identify and assess specific health and safety hazards present in their facilities.
Slips, Trips & Falls
The biggest manufacturing facility hazards come from injuries resulting from slips, trips, and falls.
Falls are the leading cause of injury and death among all American workers in the private sector and are consistently one of the top three causes of injury across all industries, and can lead to severe injuries like bone fractures and concussions.
How To Reduce the Risk:
- Enforce good housekeeping techniques.
- Keep walkways clear of debris and equipment.
- Clean up spills immediately and make spill kits readily available to employees.
- Enforce rules about appropriate footwear, like non-slip shoes or boots.
- Install proper signage or permanent, highly visible markings in areas of uneven flooring.
- Install guardrails in elevated areas or locations where falls may happen.
- Ensure proper lighting in all areas of a facility.
- Utilize weather mats in high traffic areas, entrances, and exit ways.
Complacency In The Workplace
The overwhelming majority of manufacturing facility hazards, accidents, and injuries that occur in the workplace are not the result of willful actions.
These hazards result from complacency surrounding safety procedures, usually initiated by stress, fatigue, or rushing to meet production requirements.
This complacency leads to mistakes and errors, which can result in serious injury to employees.
When longtime employees operate the same equipment every day, they quickly become comfortable and may begin to rely on safeguards as the only line of defense against accidents or injury.
Every time a risk is taken without adverse consequences, an employee builds a belief that the action may be an acceptable risk.
Management must take the lead in encouraging employees to slow down and do things correctly, stressing the value of human life and safety over production results in all scenarios.
How To Reduce the Risk:
- Create a culture of risk management.
- Stress the importance of worker health and safety over all other enterprises.
- Provide proper training and education for employees on safety protocols.
- Provide oversight for staffing and scheduling to reduce worker overload and burnout.
- Utilize supervisors to be a liaison between the company and the employees.
- Reinforce the use of safety protocols before, during, and after every shift.
- Perform risk assessments for each employee, operation, or process.
Powered Industrial Machines
The use of powered industrial machines definitely belongs to this list of manufacturing facility hazards.
Every manufacturing facility has different needs for powered industrial machines , but they typically have equipment such as: forklifts, power jacks, lift and reach trucks, and vehicles.
Manufacturing companies use these machines to raise, lower, or move heavy goods or materials. The greatest risk to human life regarding the use of these vehicles comes from improper employee training or operation.
OSHA has strict guidelines about the use and operation of powered industrial machines.
These include ensuring all machinery meets requirements and regulations regarding the allowed weight or type of materials transported or moved by said vehicle. They also require testing and certification for every powered industrial machine and the employees who operate them.
How To Reduce the Risk:
- Provide proper training and certification for any employee who operates a powered industrial machine.
- Ensure supervisors are performing consistent oversight of employees.
- Adhere to a regular maintenance schedule to ensure machinery is in working order.
- Perform frequent inspections to catch potential mechanical failures before they occur.
- Keep detailed records of incidents, accidents, and close calls.
- Utilize OSHA resources to guarantee that each piece of powered industrial machinery is tested and certified.
- Stress the importance of safe use and operation by balancing workloads to reduce mistakes caused by stress or shortcutting.
Electrical Hazards
Electrical hazards pose a serious risk to employees, products, and facilities.
Mismanagement of potential electrical hazards can result in serious injury, from electrocution to fires and burns.
Common causes of electrical accidents are un-planned contact with power lines, improper use of extension or power cords, and incorrectly grounded or poorly maintained power sources.
The ability of electrical equipment to function properly can be compromised by normal wear and tear.
Accidental exposure to water sources, improperly handling explosive or flammable substances, and overloaded circuits can lead to disastrous results.
Any workplace environment that exposes employees to potential hazards related to the use of electricity must be carefully managed.
OSHA provides resources for companies on how to identify, assess, and manage potential hazards related to electricity.
How To Reduce the Risk:
- Adhere to strict safety policies whenever work is performed around or near power lines.
- Choose non-flammable materials whenever possible.
- Ground all power supply systems, circuits, and electrical equipment and install proper ground-fault circuit interrupters (GFCIs).
- Use double-insulated tools and equipment and provide employee training on proper use and operation.
- Perform visual inspections of all electrical tools and equipment before use, and properly tag any defective tools for maintenance.
- Perform frequent inspections and testing of all electrical supply systems.
- Ground all exposed metal parts of equipment, including non-electrical equipment like frames, tracks, or hand-operated parts of machinery which come in contact with electricity.
- Provide proper PPE for employees who are exposed to the risk of electricity.
- Have an emergency preparedness plan and evacuation procedures in place.
Machine Guarding
In a manufacturing facility, hazards from heavy machinery and equipment are a constant risk for workers. More than 800 people are killed and almost 18,000 are injured each year by machinery.
Any piece of machinery, equipment, function, or process that may cause injury to workers or persons in close proximity must include the use of proper guards. These guards must meet or exceed the original manufacturer specifications for the type of machinery or equipment.
When a machine guard is poorly installed or made from improper materials, it increases the risk of accident or injury to workers.
Another common issue comes from workers who get complacent when operating machinery with guards in place, which is caused by workers mentally zoning out when they continuously do routine work.
Employees may disregard safety protocols because they trust the machine guard to keep them safe.
How To Reduce the Risk:
- Employees should be educated and trained on the proper safety standards and operating procedures for each piece of equipment or machinery.
- Balance workload and production requirements for employees to avoid shortcutting or complacency due to rushing or stress.
- Educate employees on emergency procedures in case of a serious accident or injury from a moving machine.
- Use manufacturer-recommended materials for machine guarding and ensure proper installation.
- Utilize clear and visible signage on areas of machinery that may cause injuries, like moving parts or pinch points.
- Inspect machinery and machine guards regularly to identify areas of degradation and perform regular maintenance to prevent injury from damaged or deteriorating parts.
- Provide personal protective equipment, like eye goggles, gloves, and aprons, for employees operating any potentially dangerous equipment.
Manufacturing Facility Hazards from Poor Maintenance
Health and safety hazards that result from poor maintenance are the direct responsibility of companies themselves.
A lack of maintenance schedules or improper maintenance procedures increases the risk of accidents and injuries exponentially in a manufacturing facility.
Machinery and equipment require preventative maintenance to slow or eliminate risks related to mechanical failure.
A company that spends the proper time and resources to properly maintain machinery and facilities can better mitigate and reduce hazards. Any company that neglects these procedures opens itself up to liability.
How To Reduce the Risk:
- Utilize supervisors to create and uphold a strict maintenance schedule for machinery, equipment, and facilities.
- Properly train and educate employees and supervisors on safe and proper maintenance techniques.
- Perform frequent inspections and testing to identify areas that need maintenance or repair.
- Utilize fail-safe alarms and triggers for machinery to immediately cease operations when a potential mechanical failure occurs.
- Mark equipment, tools, machinery, or areas of facilities as out of service with clear signage.
- Keep sufficient stock of frequently used materials and replacement parts.
Solutions To Common Manufacturing Facility Hazards
Prevention is Key
When it comes to reducing, managing, or eliminating risk from manufacturing facility hazards, prevention should be the number one priority.
Nothing could be more important for a company than acting preventatively and aggressively when assessing and managing hazards in the workplace.
Failing to do so can cost manufacturing companies lost productivity due to missed work, high turnover related to worker satisfaction, and increased insurance premiums and workers' compensation payouts.
But above all else… taking preventative steps to protect workers from accidents, illness, or potentially life-changing or fatal injuries is the responsibility of every employer.
Companies must take immediate steps to identify and assess routine hazards in the workplace. They must have plans and procedures in place to instruct employees on how to respond to emergencies.
Preventative Hazard Control Measures:
- Identify and assess hazards using preexisting knowledge from industry standards, the National Institute for Occupational Safety and Health (NIOSH) resources, and OSHA. Complex organizations can request an on-site consultation program from OSHA to help with the process.
- Utilize automation for tasks that require handling of hazardous materials or require dangerous or repetitive tasks.
- Develop a hazard control plan to create and implement controls for individual activities and processes.
- Evaluate existing control measures and assess the need for improvements.
- Utilize employee knowledge and experience to identify potential concerns or problem areas.
- Consider alternative materials or machinery in place of harmful or hazardous choices wherever possible.
- Track results and outcomes to assess risk and identify processes that require additional safety controls.
- Create a detailed plan for each hazard that has the potential to escalate to an emergency situation.
- Utilize two-person teams for activities or processes which have the potential to cause serious bodily harm or injury.
Education and Training
Manufacturing companies rely heavily on humans to carry out work related to production.
According to the Department of Labor, roughly 4 out of every 100 workers in a manufacturing facility will face illness or injury every year.
The risk of severe injury or death is higher in the manufacturing sector.
Proper activity-focused training for employees can greatly reduce the risk for both companies and workers.
It is the responsibility of employers to guarantee that their workforce is extensively trained on safety procedures.
Below are some steps that companies should take to place a direct focus on instructing workers on safety procedures and protocols.
- Train supervisors and managers on proper safety training and oversight procedures.
- Educate and train employees on best safety practices and emergency preparedness.
- Implement safety procedures that are clear, precise, and easy to follow.
- Train workers to identify hazards in their environment.
- Track worker performance and adherence to safety practices and identify opportunities for retraining or additional education.
- Utilize targeted training courses or certification programs for employees tasked with operating dangerous machinery or handling hazardous materials.
- Appoint safety managers to help train employees and execute safety initiatives.
Emphasis on Responsibility
Employers are responsible for their workers and must prioritize health and safety measures, provide proper training before work begins, and create and maintain a safe working environment.
Employees are not without responsibility either. Each employee must understand that they have a responsibility to act conscientiously and precisely to avoid risks to themselves and coworkers.
The U.S. Department of Labor Statistics reports that increased awareness and focus on hazard reduction in the manufacturing sector is paying off.
Over the last decade, the average number of injury cases per one hundred workers has been cut in half. But the risk to worker safety and welfare is still present, and companies cannot afford to go backward on the topic.
Employer responsibilities concerning worker safety are not only important, but they are also highly regulated.
Employees must understand that they may be held personally liable for actions that endanger coworkers in a working environment.
Routine Maintenance
The manufacturing sector relies heavily on machinery and equipment and uses human interaction with that machinery in the production process.
Companies that do not place a dedicated focus on proper and prompt maintenance procedures open themselves up to all kinds of liabilities.
Improper maintenance schedules can lead to preventable and devastating accidents or injuries. Manufacturing facility hazards greatly increase when machinery, equipment, and facilities are not given timely and scheduled attention.
Companies are directly responsible for holding a high standard regarding routine maintenance procedures.
Maintenance activities may include:
- Inspection of machinery, equipment, tools, and facilities.
- Testing of machinery to ensure proper operation and function and identify areas where intervention may be necessary.
- Ensuring proper inventory of replacement parts and materials.
- Creating and adhering to a dedicated maintenance routine to prevent breakdowns before they occur.
- Increasing focus on maintaining safety measures like machine guards and fault detection.
- Maintaining good housekeeping around and inside machinery, including cleaning, lubricating, and servicing parts that create dust or debris during operation.
Final Thoughts
Manufacturing facilities face an incredibly high risk for employee health and safety.
Sometimes hazards are a planned and necessary risk, like using hazardous materials or utilizing dangerous heavy machinery in the production process.
Many times, hazards are unplanned events related to a lack of safety oversight procedures. Catastrophic accidents can occur when companies don't create, execute, and enforce safety procedures as a top priority.
The steps, mentioned in this article, can be taken to help identify, assess, and manage hazards within a manufacturing facility.
Companies should place worker safety above all else, including profits and production time.
Being proactive with maintenance, emphasizing proper training, encouraging adherence to best safety practices, and constantly looking to reduce workplace hazards are just a few ways manufacturing companies can keep employees safe while they're at work.
Topic(s):
Training
Related Posts
View All Posts
Continuous Improvement
11 Essential Workplace Safety Tips for a Secure & Healthy Environment
24 min read
Workplace safety is a topic that businesses simply cannot overlook. For one thing, employers have an obligation to their employees to provide a safe work environment and to...
Continue Reading
Frontline Digital Transformation
6 Strategies to Maximize Worker Safety
7 min read
In industrial companies, workplace safety is the #1 driver behind many key decisions. Not only is safety essential for protecting workers, it’s also essential for consistent...
Continue Reading
Standard Work
Best Methods to Reduce Human Error in Manufacturing
27 min read
In manufacturing, many factors need to be balanced and aligned for companies to be successful. And one of those factors includes the combination of humans and machines...
Continue Reading