
Standard Work
28 min read
Best Methods to Reduce Human Error in Manufacturing
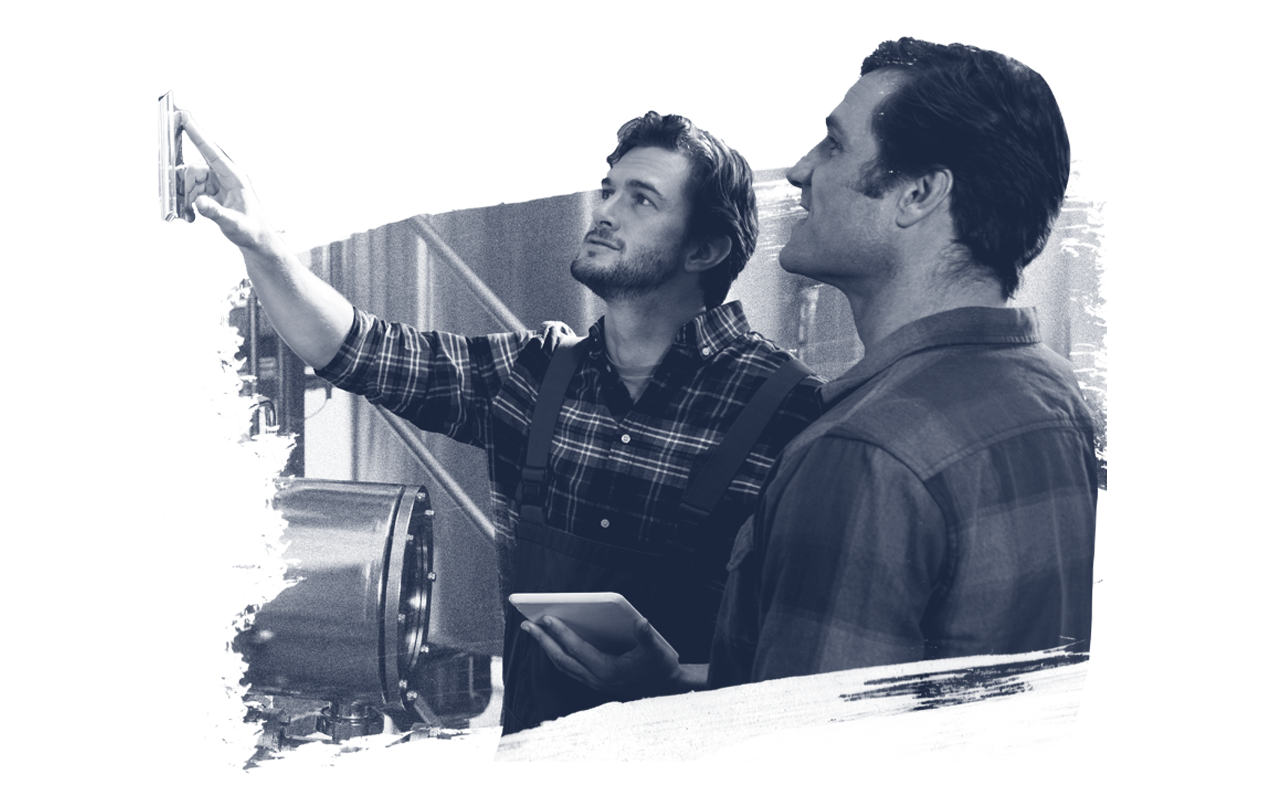
In manufacturing, many factors need to be balanced and aligned for companies to be successful. And one of those factors includes the combination of humans and machines working together.
The performance of the workforce must be considered at all points of the manufacturing process for companies to build the highest quality products at the lowest cost possible.
That equation is what makes manufacturing companies successful in the long term. But as most people know, whenever human beings enter an equation, mistakes are going to be made along the way. Human error is a fact of life and can cost manufacturers time, money, and profits.
But the risk of human error in a manufacturing plant can far exceed these things. Human errors and mistakes can lead to disastrous results for manufacturing companies, both legally and financially.
And that’s not to mention the risk of injury and possible loss of life when it comes to their employees.
In this article, we will explain the factors that contribute to human error and outline some ways manufacturing companies can improve their awareness. Doing so will help improve safety, increase productivity, and help companies to be more successful overall.
Defining Human Error in Manufacturing
To define how human error affects manufacturing companies, it's vital to understand what human error is and what contributes to it. Understanding the events that led to an employee making a mistake is the first step to avoiding the same mistake from being made in the future.
Human error can be defined simply as anytime a human being makes a mistake. But to break it down into causation, we need to look beyond that. Human error can be better defined as an action taken by a human being that results in incorrect or incomplete output, meaning the results gained are not what was expected or desired.
When examining ways to reduce human error in manufacturing, it’s important to first rule out other possible factors that may have led to incorrect results. Eliminating things like mechanical failure or breakdown, faulty or improper materials, and outside factors that did not directly contribute to the decisions made by the human allow companies to better identify when the issue lies with human error.
Types of human error do not fall into one neat category. As far as the manufacturing industry is concerned, it can be many different things. Some examples of human error would be:
- Incorrectly reading an instruction
- Using the wrong tool, or using it incorrectly
- Performing a process or activity incorrectly
- Improperly measuring something
- Failing to maintain safety procedures
- Taking an incorrect action or making an incorrect decision
Practically any process, skill, or activity that is undertaken within a factory can include a percentage of human error. That’s why companies need to seek to reduce human error in manufacturing whenever and wherever possible.
Mental and Physical States Affecting Human Error in Manufacturing
It’s a well-known fact that employee well-being should be considered in any working environment. Employees who are healthy, both mentally and physically, perform their jobs better and have better job satisfaction as a result.
What might not be as clear is that an employee’s mental and physical state directly affects their performance regarding mistakes, accidents, and errors. And this is something that companies should be aware of and try to mitigate when looking at ways to reduce human error in manufacturing.
The fact is that mental stress and physical fatigue can lead to unintended errors. According to studies, an average of 48.8% of human error in the manufacturing industry can be directly related to stress, repetition, fatigue, or the work environment itself.
Stress
Stress from pressure to meet deadlines or production goals can result in employees rushing to complete tasks and may result in mistakes.
Repetition
Repetition is defined as doing the same task over and over again. This can result in errors from employees gaining a false sense of security in the success of that task, leading to mistakes.
Fatigue
An employee who feels overly fatigued at work may find it harder to focus, leading to an increase in bad judgment or errors. Research shows that 40% of workers in the U.S. report feeling fatigued at work.
Poor Work Environment
The work environment itself can contribute to human errors if it is unorganized, distracting, unsafe, or simply not conducive to employee well-being overall.
Combating Mental and Physical Fatigue
So how can employers limit the effects of these contributing factors as they relate to human errors? One way is by focusing on what is known as ergonomics, or “human factors engineering.”
This term refers to how companies should consider human responses when designing a workplace or process, and when determining which tools, equipment, and technology can be implemented to help reduce human errors.
In essence, it’s the practice of designing systems that work as expected and then accounting for the fallibility of human beings as part of the equation.
Taking into account the four factors listed above that can contribute to human errors in manufacturing, companies can then take steps to help employees perform better.
Improper Use of Tools and Machinery or Not Performing Maintenance
Another major contributor to human error in the manufacturing industry relates to the prevalence of human beings coming in contact with machinery, equipment, and tools. Human error can occur very quickly and with incredibly devastating results when heavy or dangerous machinery comes into play.
It can be easy to blame the equipment itself when mistakes occur, but studies show that the majority of accidents or errors related to equipment failure are caused by mistakes made by humans somewhere along the line. Whether this is due to a mistake during assembly, a lack of training, improper maintenance, or incorrect use; these errors all relate to an action or inaction taken by an actual human being.
Here are some of the ways companies can reduce human error in manufacturing as it relates to tools and machinery:
- Always Use the Right Tool
- Always Use Equipment Correctly
- Establish Safety Procedures
- Maintain a Safe Surrounding Environment
- Don’t Shortcut
- Examine Procedures for Potential Improvement
The Importance of Proper Maintenance
Machinery wears out and fails eventually. Whether it’s a small part on a piece of heavy equipment or the power cord on a hand drill, it’s only a matter of time before parts needs replaced or repaired. But one would think that this fact is more related to mechanical failure rather than human error, right?
Wrong, and here’s why. When employees are forced to work with tools or machinery that is not properly maintained, it can lead to bad judgment calls that result in mistakes or accidents.
Employees may become accustomed to operating tools with faulty cords and simply chalk it up to “the way things are around here.” Not only is this an unsafe business practice, but it can result in human error that could lead to serious injury or even death.
Another human aspect to consider when talking about proper maintenance is the maintenance procedure itself. All manufacturing companies probably understand the importance of maintaining their machinery and equipment. Because without those things, there will be no production.
So, it’s safe to assume that there are already maintenance schedules and testing procedures in place.
The important part of reducing human error in this aspect is to make sure those processes and procedures themselves are being carried out regularly and properly. Failing to do so is a human error in and of itself.
Human Error Causes more Downtime in Manufacturing
Human error can lead to a long list of negative effects for companies. And one of the most detrimental effects for any manufacturing company is an increase in downtime. When machinery is not operating, and production is stalled, it can eat directly into the bottom line and cost companies both time and money.
Manufacturing companies understand the importance of keeping production lines up and running. But unfortunately, there will always be issues that unexpectedly arise that result in downtime. For companies that operate in the manufacturing sector, human error is a big contributor to unplanned downtime.
The Cost of Downtime for Manufacturing Companies
Studies show that 23% of unplanned downtime in manufacturing companies directly results from human error. Compare that to only 9% in other industries, and you can see why reducing human error in manufacturing can have a huge impact on a company's profits.
When you factor in the research that shows the average loss for a manufacturing company faced with unplanned downtime is $250,000 an hour, it becomes clear how vital it is for companies to reduce human error in manufacturing.
Experts say it’s not surprising that manufacturing companies face a bigger threat of downtime related to human error. Considering the prevalence and complexity of the machinery and equipment used in manufacturing processes, and the need for human intervention with that machinery daily, it’s inevitable that the risk would be higher.
Manufacturing companies can help reduce downtime related to human errors by mitigating the factors that lead to errors in the first place. One way newer technologies are being implemented on the factory floor is through automation and digital tools. Being able to track potential issues and outcomes in real-time allows companies the foresight to be able to solve many problems before they arise.
Examples of Human Error in Manufacturing
Reducing human error in manufacturing is important for so many reasons. It can benefit the company in the form of decreased downtimes, fewer defects, lowered risk of injury or accidents, lowered risk of legal litigation, and an increase in customer satisfaction.
But aside from those benefits, reducing human errors as it relates to the production of goods or products can have a huge impact on the environment, consumers, and the market as a whole.
As discussed earlier regarding the Chernobyl nuclear crisis, small mistakes can cause devastating effects. Human errors can look like a lot of different things, even as it relates to manufacturing. Here are a couple more examples of huge disasters which were caused by errors made by humans.
The Mars Climate Orbiter
In December of 1998, the Mars Climate Orbiter satellite was launched and tasked with the job of surveying the planet Mars from space. The idea was that it would take pictures of the surface of the planet and study weather and climatic conditions.
Halfway through the intended mission time, the Orbiter was lost and plummeted into the atmosphere of the planet, disintegrating along the way. The failure was caused by a simple mistake in calculations. Navigational commands were sent in the wrong unit of measurement, the result of human error. The total cost of the lost spacecraft was $327.6 million.
Wrong Methods of Correcting Human Errors
While discussing the ways companies can reduce human error in manufacturing, it’s important to pinpoint the factors that contributed to the error in the first place. Only then can companies strategize solutions and improvements that can prevent the same error from happening again.
But it’s also vital for companies to understand that there are incorrect responses to human error and wrong ways to go about exacting change. Using improper methods will not lead to the kind of beneficial improvements that are needed to minimize the risk and occurrence of human error.
Here are a few mistakes many employers make when attempting to correct workers that made a mistake:
Negative Encouragement
Addressing a mistake is the first step toward correcting it and informing employees of an error can help them recognize what they did wrong. But it’s important for companies not to use the wrong language when discussing an error. Directing them to try harder or be more careful won’t get the same results as giving them the actual tools and skills to make more informed decisions and perform better in the future.
Improper Punishments
While performance reviews are a valuable tool for companies to open lines of communication with workers and better understand where their strengths and weaknesses lie, employers need to use them correctly. Serious infractions regarding safety protocols should be addressed quickly and succinctly, but don’t attempt to make an example out of an employee who made an honest mistake.
Not Identifying the Root Cause
Every effect has a cause, and every cause has an effect. That’s why it’s important to examine each mistake or error that workers make and strive to identify that cause. Addressing the result without identifying what led to it will do nothing to stop the problem from occurring again. Ask questions about an employee's understanding of processes and procedures and inquire into their health and well-being.
Not Focusing on Safety Procedures
Maintaining a focus on safety procedures and ensuring that all employees understand and implement them regularly will go a long way toward keeping workers safe and lowering the amount of human error. A simple, clear, and defined focus on safety will build a workforce culture that values workers first.
Not Giving Workers Solutions
Once a root cause of an error has been identified, companies must develop solutions that effectively address the issue. And then employees need to be given the tools and knowledge to better perform their jobs and understand the risks involved with making bad decisions or mistakes.
The Danger of Rushing
An employee who is facing time constraints or feels pressured to increase output can make costly mistakes as a result. Company executives and supervisors are often driven by numbers, and it may be hard to see the big picture when they're not on the production frontline. Rushing to complete work can lead to short-cutting or inattention which can lead to errors.
Studies show that human errors and accidents tend to increase on Fridays, holiday weekends, and when production goals are behind schedule. This is a direct result of workers rushing to complete their work and making mistakes in the process.
Why Proper Training and Supervision are Important
Improper or incomplete training can be a big driver of human error. When workers don't receive the training and knowledge to correctly perform job tasks, they will be more likely to make mistakes.
Training Can Prevent Errors Before They Occur
Onboarding and training of employees upon hire are important for companies to prevent errors before they occur. If an employee receives the knowledge they need to perform skills correctly and safely from the onset, before work begins, they will better be able to make informed decisions and have the skills to do jobs the right way the first time.
Training employees on how to identify potential areas that are ripe for error can help them have foresight into the consequences of their actions. One way to do this is to include training that focuses not just on how to do the job, but also on why the job is important. When workers understand the importance of their role in the bigger picture of production and company success, they will be more motivated to make careful decisions and avoid errors.
Employees should also be trained on how to spot potential errors before they occur. Well-trained and experienced employees will be able to recognize scenarios where a mistake is about to be made and will have the knowledge to react proactively.
Learning Management Systems and Their Importance
Training methods can vary, especially in today’s workplace environment. Gone are the days of workers sitting in crowded classrooms and flipping through endless pages of manuals and procedures.
Workers will learn much better with a combination of virtual learning, micro-learning courses, and interactive hands-on training. This type of training can easily be achieved with advanced digital learning management software programs.
Supervision and Oversight Can Prevent Errors
If an employee is struggling or making mistakes consistently, they must be allowed to ask questions and receive guidance on how to prevent those mistakes. Having well-trained managers and supervisors available for employees to consult can help correct bad or incorrect behaviors.
It’s also important that any supervisors tasked with employee oversight have the proper training and skills to correct behaviors in a meaningful and appropriate manner. If a supervisor seems unapproachable and is consistently offering negative feedback, employees will be less likely to reach out with questions.
Companies should have over-arching supervisory systems in place that are tasked with monitoring and evaluating processes and analyzing their results. This can help companies pinpoint areas that have a high occurrence of error or failure. Only then will companies be better able to reduce human error in manufacturing.
Solutions That Help Manufacturing Companies Reduce Human Error
There are several strategies that companies can use to reduce human error in manufacturing. There is a simple three-step process that all companies should use to identify and correct errors or prevent them from occurring repeatedly.
Identify Errors
The first step to fixing any problems is recognizing the problem in the first place. A lot is happening at once on a factory floor, so it may be easy for errors to go undetected. That's why companies should have an advanced monitoring system in place that can red flag when processes deviate from standards or output baselines change.
Recognizing areas that have already experienced an error or drawing attention to areas that have the potential for errors to occur soon can help companies take the next step in correcting behaviors.
Identify Root Causes
Once an error has been identified, the next step to correcting it is to identify the reason it occurred in the first place. Each error should be given individual attention, including asking employees for direct feedback on what contributed to the error happening. Asking the right questions can help pinpoint causation:
- Was there a lack of understanding of job skills?
- Was there equipment or tools used improperly or incorrectly?
- Was there a decision made based on incomplete or incorrect information?
- Was the employee’s physical and mental well-being a factor?
- Was the employee rushing to meet production goals?
- Was proper supervision in place to allow guidance and feedback from management?
- Was the employee given the tools to limit the risk of error in the first place?
Form a Plan of Action to Correct or Prevent Further Errors
Once an error has been identified and the cause of the mistake is clearly understood, companies must form a clear plan of action that includes steps and mechanisms designed to improve results and reduce the rate of that error.
This plan will be heavily reliant upon the root cause of the problem and should include proactive steps that workers and supervisors can take to help identify future errors before they occur. It’s much easier to fix a problem that hasn’t happened yet than it is to repair the damage caused after the fact.
Additional Tips to Help Reduce Errors in Manufacturing
Open and Effective Communication
Having clear communication paths between workers, supervisors, and management can prevent confusion and misunderstanding and help prevent errors. There should also be a way for departments to communicate with each other quickly and efficiently, or for employees to communicate immediately from the plant floor.
Focus on Safety Protocols and Quality Standards
Ensuring that employees have a clear understanding of what’s expected of them on a day-to-day basis can help limit the risk of error. When workers know the expectations of performance and are held to a high standard regarding the most basic processes, they will be less likely to make decisions that could lead to errors.
Double Check the Important Parts
When an area of production has been identified as having a high probability of error for any reason, companies should pay extra attention to the processes involved. Using a system of double-checks and fail-safes will help limit the risk involved with actions that can result in errors. It goes back to the adage: measure twice, cut once.
Give Employees the Tools to Be Successful
Training and development are one of the most important aspects of well-rounded and engaged workers. And an employee who is engaged in their work will pay more attention to the details that are required to prevent errors.
Companies should also offer workers every opportunity to increase their physical and mental well-being while on the job. The ability to take breaks and a designated place to do so can help reduce stress and fatigue.
Offering workers things like gym memberships, free mental health counseling, and even company events and outings can improve employee well-being and foster a culture of caring that will drive employees to perform better.
Utilize Technologies to Help Mitigate Risk of Errors
Using the right software and technology solutions is a vital way to help companies reduce human error. From digital Learning Management Systems (LMS), automation opportunities, and real-time data and process analysis, the tools available for manufacturing companies are expanding at a fast pace.
Companies should take advantage of every available avenue that will lead to a reduction in errors.
Final Thoughts
Human beings are not infallible, and they will eventually make a mistake. It’s just a part of being human. This means that any industry which employs the use of human labor is vulnerable to mistakes caused by those humans.
Understanding the root causes of those errors can help companies avoid them and reduce the chances that they will happen.
Companies and their workers must understand the devastating impact that even the simplest error can have on accidents, injury, and even the potential loss of life.
It's shown that over 90% of errors and accidents that occur in the workplace are the result of human error. That percentage cannot be overlooked, especially when so much is on the line.
The most common causes of human error in the workplace are stress, fatigue, repetition, poor working environment, improper or incomplete training, and poor communication. Once companies understand the most prevalent causes of human error, they should take proactive measures designed to limit the risk of errors resulting from those causes.
Proper documentation is a great way for companies to manage and track the risk of potential areas. Documenting actual mistakes and even near-misses that had a potential for error can help companies see where improvements can be made and track progress over time. When incidents and accidents are investigated thoroughly, it leads to a safer workplace for everyone.
One of the best ways companies can reduce human error in manufacturing facilities is to utilize technology to recognize and correct issues before they occur. Comprehensive and hands-on training that includes up-to-date information and procedures can prevent errors from occurring due to knowledge gaps.
When companies take advantage of the best tools available and put proactive strategies in place aimed at lowering the risk and rate of human errors, they will see higher profits, an increase in productivity, reduced downtime and employee turnover, and greater overall success.
Topic(s):
Standard Work
Related Posts
View All Posts
Training
6 Common Manufacturing Facility Hazards & Effective Solutions
20 min read
Manufacturing facilities serve an important function in a country’s economy, as they create jobs, increase wealth through added value and taxes, promote trade, and support...
Continue Reading
Work Instructions
Benefits of Procedures & Work Instructions in Manufacturing
24 min read
Ah, the lingo of business. If there’s one thing that the world of business and industry loves, it’s terminology. Every industry has developed its own language, with specific...
Continue Reading
Standard Work
How To Reduce Defects in Manufacturing in 2022
24 min read
Product defects are a pain at any manufacturing company. When all the time, energy, and money that is spent to produce a product is wasted due to defects in the final...
Continue Reading